Con i sistemi di monitoraggio e controllo dell’aria compressa Smartlink e Optimizer 4.0 di Atlas Copco è possibile ottimizzare i consumi energetici e ridurre i fermi produttivi.
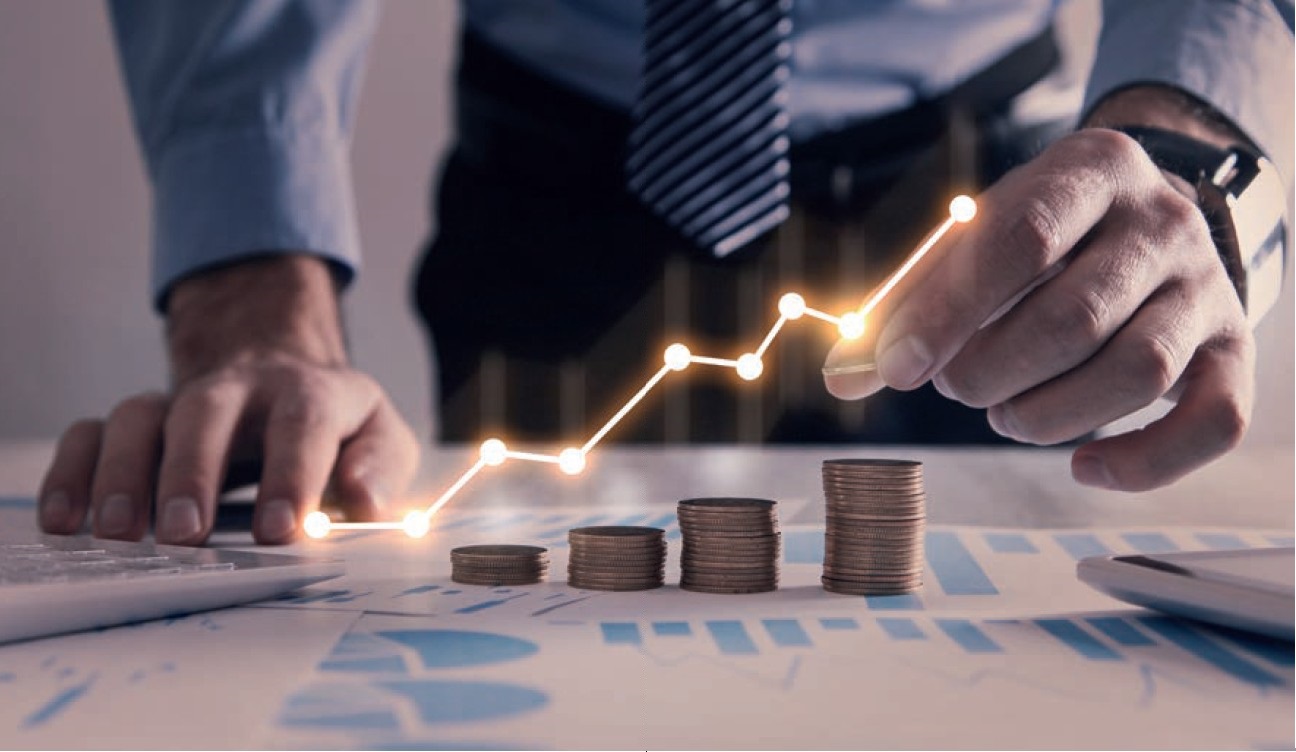
Con i sistemi di monitoraggio e controllo dell’aria compressa Smartlink e Optimizer 4.0 di Atlas Copco è possibile ottimizzare i consumi energetici e ridurre i fermi produttivi.
Da uno studio realizzato dal Fraunhofer Institute l’uso di sistemi di controllo intelligenti permette di ridurre il consumo energetico dei sistemi ad aria compressa fino al 12%. Un dato importante considerando che l’aria compressa è utilizzata in molti settori industriali, dall’industria meccanica a quella chimica e petrolchimica, dall’alimentare alle costruzioni, con un’incidenza fino all’11% nei consumi elettrici aziendali. In alcuni casi, per esempio nella produzione di polistirolo espanso o di bottiglie in PET, il consumo di energia ascrivibile all’aria compressa può arrivare al 30%.
Aria sotto controllo
I sistemi di monitoraggio e controllo intelligente, grazie alla loro presenza 24 ore su 24 e 7 giorni su 7, permettono di ottimizzare i consumi riducendo al minimo i costi di esercizio. I dati provenienti dai diversi macchinari possono essere analizzati per definire e tenere sotto controllo i KPI (Indicatori Chiave di Prestazione), prevedere potenziali problemi, gestire un piano di miglioramento continuo e aumentare l’efficienza energetica del ciclo produttivo. Fra i sistemi intelligenti rientrano Smartlink e Optimizer 4.0 di Atlas Copco. Smartlink è lo strumento che consente di monitorare la sala compressori, 24 ore su 24, 7 giorni su 7, da PC, tablet e smartphone assicurando una visione completa della produzione di aria compressa, aiutando a prevedere e quindi prevenire potenziali problemi. Grazie alla pianificazione degli interventi manutentivi basati sulle reali condizioni di funzionamento dei sistemi, l’abbattimento del rischio di guasto e il conseguente aumento degli indici di disponibilità delle macchine permettono di ridurre sprechi o inefficienze causati da manutenzioni inefficienti. In passato la manutenzione sui compressori era regolata da contratti di assistenza preventiva standard, che assicuravano visite regolari in base alle ore di lavoro stimate, o assistenza reattiva nel caso di un imprevisto che richiedesse un intervento urgente. Se un problema sfuggiva all’attenzione, poteva causare fastidiose interruzioni della produzione e richiedere tempi di fermo elevati, causando costi imprevisti. Con Smartlink i dati raccolti sono analizzati in tempo reale e, a fronte di eventi critici, vengono generate notifiche per consentire azioni immediate. Tutto ciò avviene in automatico: i dati vengono raccolti, immagazzinati, analizzati sulla piattaforma online dedicata, che si occupa di inviare periodicamente agli energy manager e ai gestori dell’impianto un’analisi dei consumi energetici conforme alla ISO 50001, lo standard internazionale che regola i sistemi aziendali di gestione dell’energia. Optimizer 4.0 è invece dedicato alla gestione della sala compressori: grazie a un algoritmo proprietario automatizza la gestione dei compressori e garantisce in ogni momento la produzione di aria compressa alla massima efficienza energetica.
Qualità e sicurezza nel food
Goglio è tra le principali aziende italiane nel settore del packaging alimentare. Per garantire l’assenza di contaminazione da oli durante l’imballaggio, e quindi preservare la qualità dei suoi prodotti finali, l’azienda ha scelto i compressori oil free di Atlas Copco che non utilizzano alcuna lubrificazione nella camera di compressione. L’efficienza energetica dell’impianto è garantita dal nuovo controller Optimizer 4.0 che, grazie a un algoritmo proprietario, è in grado di prevedere il comportamento del sistema e utilizzare la migliore combinazione dei compressori, così da garantire in ogni momento la portata richiesta e la massima efficienza energetica. Il monitoraggio dei compressori è stato affidato invece a Smartlink, il sistema che assicura una visione completa della produzione di aria compressa aiutando a prevedere, e quindi prevenire, potenziali problemi. «Goglio prevede di proseguire il suo percorso di innovazione nei prodotti e nei processi anche in futuro, incrementando la garanzia e la qualità offerte ai propri clienti – spiega Giorgio Soldarini, direttore ingegneria impianti, filmatura e HSE (Health, Safety & Environment) di Goglio – e riteniamo che questo sia un aspetto determinante per la nostra mission e condividiamo pienamente i valori di Atlas Copco, impegnata come noi nello sviluppo di prodotti e soluzioni per aumentare la produttività, l’efficienza energetica e la sicurezza dei processi produttivi». «Solo conoscendo a fondo come funziona il proprio impianto di produzione di aria compressa si possono apportare miglioramenti – ha aggiunto Alessandro Viola, Product Marketing Manager Advanced Services di Atlas Copco – e Smartlink mostra dove è possibile ottimizzare e risparmiare energia, mentre Optimizer 4.0 si fa carico dell’ottimizzazione dei consumi. Anticipare le esigenze del mercato è da sempre la nostra mission: per questo offriamo soluzioni finalizzate a migliorare la gestione e l’efficienza energetica della produzione di aria compressa, con l’obiettivo di aumentare in maniera sostenibile la produttività dei nostri clienti».
a cura di Loris Cantarelli
Condividi l'articolo
Scegli su quale Social Network vuoi condividere