Ottimizzare le prestazioni con affidabilità e risparmio energetico, nell’incontro con il general manager Juan Manuel Tejera Martinez.
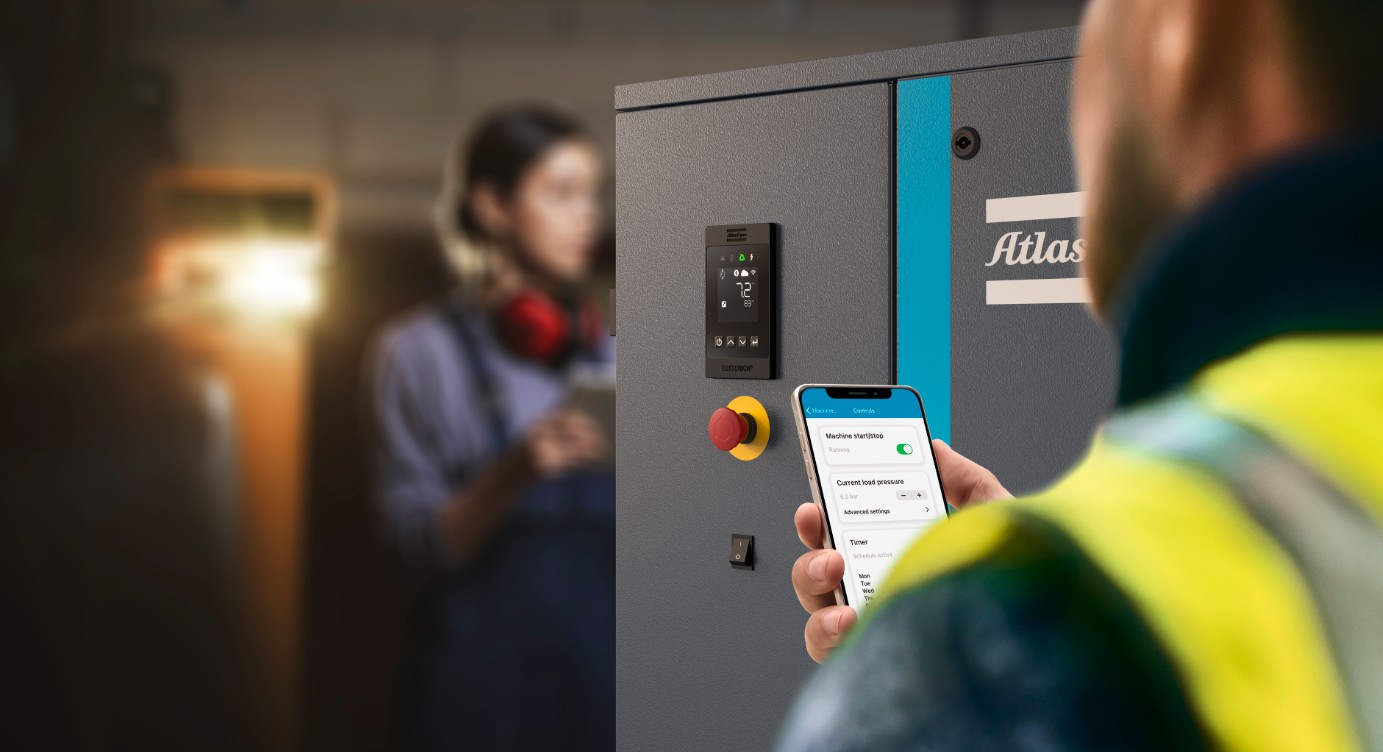
di Simona Recanatini
Ai vertici nel settore della produzione e del controllo dell’aria compressa, Atlas Copco consente di ottimizzare le prestazioni garantendo affidabilità, semplicità di utilizzo, risparmio energetico e manutenzioni pianificate, grazie a sistemi di ultima generazione con monitoraggio e controllo remoto dei dispositivi. Fondata nel 1873 a Stoccolma in Svezia, l’azienda ha segnato l’evoluzione tecnologica grazie a competenza, lungimiranza e spirito innovativo, trasformando le idee in soluzioni capaci di garantire vantaggi e benefici alle realtà produttive. Con una presenza in oltre 180 Paesi, è leader mondiale nella produzione di compressori, soluzioni per vuoto e utensili industriali. Dal 1950 è presente in Italia, con sede a Cinisello Balsamo (MI).
Per la produzione e il controllo dell’aria compressa si presenta alle imprese di numerosi settori industriali come unico partner proponendo soluzioni complete grazie a un’offerta che comprende compressori d’aria, soffianti, sistemi per il trattamento dell’aria compressa e generatori di gas industriali.
Per conoscere più da vicino questa realtà e il suo legame con l’Industria 4.0, abbiamo rivolto alcune domande a Juan Manuel Tejera Martinez, General Manager Atlas Copco Italia – Divisione Compressori.
L’Industria 4.0 è un elemento trainante per ottimizzare la produttività e l’efficienza delle imprese manifatturiere: qual è la posizione di Atlas Copco, in proposito?
Il tema Industria 4.0 è nato in Germania, con l’obiettivo di avviare la “quarta rivoluzione industriale” integrando il processo produttivo delle imprese manifatturiere con le più evolute tecniche di informazione e comunicazione digitale. Per aumentare l’efficienza dei processi, infatti, era necessario mettere in comunicazione l’apparato produttivo con il sistema gestionale aziendale. Elementi trainanti del piano erano, e sono tuttora, l’interconnessione dei macchinari di produzione e lo scambio dei dati fra di loro. Le tecnologie Atlas Copco rientrano perfettamente nello scenario ipotizzato da Industria 4.0, che prevede l’interconnessione delle macchine e la loro gestione con un sistema di controllo. Per generare efficienza, ridurre i consumi energetici e migliorare la sostenibilità ambientale è infatti necessario un sistema intelligente per la gestione dell’aria compressa, alla quale sono imputabili l’11% dei consumi elettrici con un’incidenza che può arrivare a rappresentare più del 30% dell’energia elettrica consumata da un’impresa. A questo si aggiunge che il 70% del costo del funzionamento di un compressore durante il suo ciclo di vita è dovuto al consumo energetico.
In che modo l’Industria 4.0 e digitalizzazione hanno influenzato lo sviluppo strategico dell’offerta Atlas Copco – Divisione Compressori?
La digitalizzazione dei processi è un elemento fondamentale per portare efficienza operativa nelle imprese, e questo si verifica anche nei sistemi di gestione dell’aria compressa. Da uno studio realizzato dal Fraunhofer Institute, l’uso di sistemi di controllo intelligenti permette di ridurre il consumo energetico dei sistemi ad aria compressa fino al 12%. L’evoluzione tecnologica dell’offerta Atlas Copco non poteva non tenere conto di questo aspetto, mi sento quindi di affermare che Industria 4.0 è, dal nostro punto di vista, un’opportunità per ridurre i costi di gestione dei nostri clienti fornendo loro elevati risparmi energetici, maggiore efficienza, e facilità nelle operazioni. I vantaggi di una gestione intelligente dell’aria compressa sono infatti la possibilità di gestire in modo automatico il sistema controllando il valore della pressione dell’aria e rilevando in tempo reale eventuali perdite. I dati provenienti dai sensori presenti sul sistema possono essere utilizzati per visualizzare da remoto le prestazioni del compressore e raccolti per effettuare valutazioni su come ottimizzarne il funzionamento. Nel loro insieme, tutte queste funzionalità rendono il sistema di aria compressa molto più efficiente, affidabile e compatibile con il concetto di impresa intelligente e automatizzata.
Quali sono i prodotti Atlas Copco che hanno come framework tecnologico di riferimento l’Industria 4.0?
Parliamo principalmente di Elektronikon, il sistema di controllo che utilizza la tecnologia IoT (Internet of Things) per abilitare il monitoraggio remoto e la conservazione di energia, di SmartLink, il sistema di monitoraggio remoto dei compressori, e di Optimizer, che si fa carico dell’ottimizzazione dei consumi.
Il regolatore Elektronikon è il “cervello” del compressore: raccoglie infatti i dati provenienti dai sensori presenti nel compressore e li elabora per fornire una panoramica del suo funzionamento. SmartLink è lo strumento che, insieme a Elektronikon, consente di monitorare la sala compressori 24 ore su 24 per 7 giorni su 7, da PC, tablet e smartphone, assicurando una visione completa della produzione di aria compressa e aiutando così a prevedere e quindi prevenire potenziali problemi. Questo permette di pianificare gli interventi manutentivi sulle base delle reali condizioni di funzionamento dei sistemi, di ridurre i rischi di guasto aumentando gli indici di disponibilità delle macchine e di diminuire anche eventuali sprechi o inefficienze causati da manutenzioni non corrette.
Grazie a SmartLink, i dati raccolti sono analizzati in tempo reale e, a fronte di eventi critici, vengono generate notifiche per consentire azioni immediate. Tutto ciò avviene in maniera automatica: i dati vengono raccolti, immagazzinati, analizzati sulla piattaforma online dedicata che si occupa di inviare periodicamente agli Energy Manager e ai gestori dell’impianto un’analisi dei consumi energetici conforme alla ISO 50001, lo standard internazionale che regola i sistemi aziendali di gestione dell’energia.
Optimizer 4.0 è invece dedicato alla gestione della sala compressori: grazie a un algoritmo proprietario, automatizza la gestione delle macchine e garantisce in ogni momento la produzione di aria compressa alla massima efficienza energetica. Si tratta di uno strumento fondamentale in presenza di più compressori, in quanto è in grado di distribuire uniformemente il carico di lavoro tra tutte le macchine presenti e di garantire che le ore di funzionamento rimangano uguali trai vari sistemi.
In tema di consumi energetici, in che modo i vostri prodotti possono risultare utili alle aziende?
Per migliorare l’efficienza energetica degli impianti ad aria compressa sono necessari, oltre ai sistemi di monitoraggio e controllo intelligente, dei compressori in grado di ottimizzare i consumi energetici. Fattore chiave in questo senso è la tecnologia di azionamento a velocità variabile VSD (Variable Speed Driver), grazie alla quale è possibile adattare la portata di aria erogata in base alle effettive necessità, riducendo così i costi energetici e l’impatto ambientale. Nel 1994, Atlas Copco è stata la prima azienda a integrare questa tecnologia nei compressori d’aria. Dopo circa vent’anni, ha poi introdotto la tecnologia VSD+ che ha fissato un nuovo standard di settore, portando il consumo di energia e la riduzione di emissioni delle aziende che lo utilizzano a dei livelli senza precedenti. Fra i sistemi in commercio con la tecnologia VSD+, ricordiamo i compressori a vite Oil-free ZT (raffreddati ad aria) e ZR (raffreddati ad acqua) che offrono una riduzione del consumo di energia fino al 35% (in relazione a sistemi con velocità fissa), garantendo un rapido ritorno dell’investimento.
Monitoraggio da remoto e predictive maintenance: qual è la vostra posizione?
Il monitoraggio da remoto è essenziale per poter fornire un servizio di assistenza predittiva, che si basa sulla possibilità di avere a disposizione e poter confrontare una grande quantità di dati da cui individuare le potenziali situazioni di malfunzionamento delle macchine. Un esempio concreto in questo senso è il nostro servizio di assistenza predittiva Diagnostic Service, che si basa sull’azione di 5 centri di controllo dislocati in diversi continenti che raccolgono e analizzano i parametri di funzionamento (temperature, pressione, consumi energetici e così via) delle macchine connesse tramite il sistema di monitoraggio da remoto SmartLink 2.0. Tali dati vengono confrontati con il loro andamento storico e viene generata una segnalazione qualora venga rilevata una potenziale situazione critica.
Il segreto di questo servizio è l’algoritmo di IA (Intelligenza Artificiale) che non solo identifica quando un determinato parametro è al di fuori di un range predefinito, ma effettua una valutazione complessiva dei dati di funzionamento del sistema sulla base del confronto con tutte le situazioni precedenti in cui si è verificato un certo fenomeno. Facendo tesoro dei dati storici e quindi dell’esperienza acquisita, il Diagnostic Service è in grado di accorgersi in anticipo di tutti i possibili malfunzionamenti: se la potenziale criticità viene confermata, il team di assistenza si adopera per condividere con il cliente una tempestiva strategia di intervento. Si tratta della nuova frontiera dei servizi di assistenza tecnica che, grazie a sistemi IoT, permettono di assicurare massima affidabilità ed efficienza operativa agli impianti di aria compressa, evitando lunghi e costosi tempi di fermo macchina.
a cura di Redazione
Condividi l'articolo
Scegli su quale Social Network vuoi condividere