Il protocollo OPC UA permette di cogliere le sfide della Fabbrica Connessa semplificando la comunicazione da macchina a macchina. La connettività e la comunicazione…
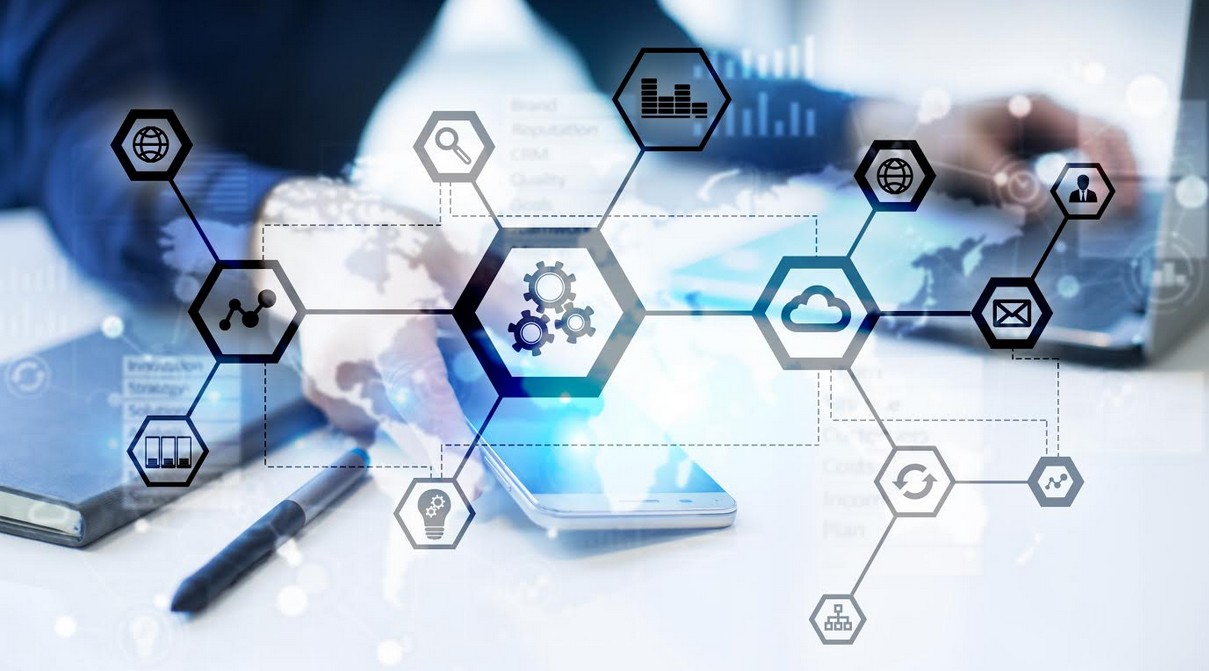
Il protocollo OPC UA permette di cogliere le sfide della Fabbrica Connessa semplificando la comunicazione da macchina a macchina.
La connettività e la comunicazione all’interno del processo produttivo sono tra i pilastri principali dell’Industria 4.0. Le fabbriche, effettivamente, sono sempre più digitalizzate e interconnesse, un requisito necessario e imprescindibile per rimanere competitivi sul mercato. Ciò comporta una crescente attenzione al potenziamento delle tecnologie che abilitano e semplificano la connettività nel settore manifatturiero, la centralizzazione dei dati prodotti in formati differenti e la loro interpretazione.
I detentori di questi dati – le macchine, i server, i dispositivi – anche qualora abbiano diversa provenienza, non hanno ragione di funzionare in maniera isolata, il valore viene creato dalla loro interazione e dallo scambio di tali informazioni. Per ovviare a questa esigenza entra in gioco lo standard OPC UA (Open Platform Communications Unified Architecture) che grazie alla sua interoperabilità contribuisce ad affrontare le sfide della Fabbrica Connessa, semplificando la comunicazione M2M (da macchina a macchina).
In cosa consiste l’OPC UA
L’OPC UA è uno standard di comunicazione M2M liberamente disponibile che consente lo scambio di dati tra controllori logici programmabili (PLC), interfacce uomo-macchina (HMI), server, client e altri macchinari. L’OPC UA è un protocollo successivo allo standard OPC Classic originale e ha diverse evoluzioni vantaggiose, tra cui l’importante caratteristica di essere progettato specificamente per l’automazione e di non essere più basato su COM/DCOM. L’OPC UA è realizzato per comunicare con i dispositivi e i sistemi industriali ed è ottimizzato per la gestione dei dati ai fini di soddisfare tutti i requisiti di un’automazione in continua crescita come quella attuale. Lo standard OPC UA ha un ampio range di implementazioni in tanti linguaggi differenti. In contesti che presuppongono macchine o sistemi diversi, e quindi la necessità di farli comunicare, l’OPC UA è un’ottima scelta poiché permette di non dipendere dai singoli fornitori.
Gli 8 principali vantaggi dello standard OPC UA:
1) Apertura
L’OPC UA è uno standard aperto: con il codice sorgente disponibile, il protocollo è implementabile sotto la licenza open source. Chi ha le competenze necessarie e volontà di costruirsi in autonomia il proprio server/client OPC UA, può avere a disposizione le specifiche e il codice (non è quindi obbligato ad acquistare un server OPC da un fornitore).
2) Versatilità cross-platform
Il protocollo OPC UA è indipendente dalla piattaforma specifica e quindi facilmente integrabile. Mentre il precedente server OPC funzionava solo sulla piattaforma Windows, l’OPC UA va oltre: mettendo a disposizione l’infrastruttura necessaria all’interoperabilità aziendale, è adatto per Windows, Linux, Mac, Android, Rapsberry Pi, e altre piattaforme. Questa caratteristica è fondamentale per il contesto industriale, vista la grande varietà dell’hardware e dei sistemi operativi oggi disponibili.
3) Sicurezza
È un sistema che soddisfa molteplici standard di sicurezza per quanto riguarda l’autentificazione, l’autorizzazione, la sicurezza intesa come integrità e privacy della trasmissione. Dal punto di vista della cyber-security, l’OPC UA permette di scambiare informazioni firmate digitalmente, crittografate, con algoritmi avanzati, anche all’interno dello stabilimento.
4) SOA alla base
L’OPC UA è stato concepito sulla base di un’architettura service-oriented (SOA). È un tipo di architettura che si utilizza nel gestire microservizi sul web e permette una gestione molto flessibile. Si predilige l’interoperabilità degli stessi, la flessibilità e la standardizzazione, per evitare implementazioni particolari e integrazioni personalizzate. Sviluppare tutto ad-hoc potrebbe portare a sistemi più ottimizzati ma a discapito dei tempi e costi di integrazione, oltre alla forte difficoltà a reagire rapidamente alle specifiche e ai requisiti in continuo mutamento.
5) Compatibilità
Il fatto che tantissimi grossi fornitori si siano allineati a questo protocollo lo rende uno standard de facto, il che vuol dire che mentre prima le aziende avevano propri protocolli, l’OPC UA è, oggi, largamente accettato e utilizzato nel mondo dell’automazione. Non riguarda soltanto il mondo dei PLC ma anche i prodotti IoT e quasi tutti i HMI, che sono compatibili con lo standard OPC UA.
6) Possibilità di svolgere azioni attive
Un altro vantaggio che porta l’OPC UA è la possibilità di gestire gli eventi e le azioni (metodi) al di là dei dati. Questo permette non solo di ricevere le informazioni ma anche di essere parte attiva della comunicazione grazie al fatto di poter comandare l’esecuzione di metodi. Il protocollo permette all’utilizzatore di definire eventi in base ai quali ricevere le notifiche. Inoltre, la gerarchia dei dati rende molto facile la ricerca delle informazioni necessarie.
7) Scalabilità
Questo vantaggio per i sistemi di nuova generazione unisce il concetto dell’open source con il concetto di cross-platform. Se un utente va a sviluppare un’applicazione o un’architettura, il protocollo offre il vantaggio di poter utilizzare un linguaggio di programmazione più adatto per implementarlo, a partire dal classico C++ o .net, Java, ma anche linguaggi molto leggeri come Python. Ciò consente di sviluppare i sistemi sia per i piccoli costruttori sia per grandi produttori. L’OPC UA di fatto vanta una scalabilità enorme, a partire dai piccoli sistemi fino ad arrivare ai sistemi molto strutturati e performanti.
8) Subscriptions e metadati
I due paradigmi che utilizza l’OPC UA sono il paradigma Client-Server (quello più “classico”) e il paradigma Publish-Subscriber che permette di sottoscriversi sotto certi criteri; quindi si può ricevere il nuovo dato se varia il valore o se varia l’istante in cui il dato è stato generato o se varia la sua qualità, cioè lo stato della comunicazione.
Oltre al dato, con l’OPC UA gli utenti ricevono tutto un pacchetto di metadati: informazioni riguardanti un dato specifico che aiutano a qualificarlo meglio (a differenza dell’OPC DA che forniva soltanto le informazioni stesse).
Bosch Rexroth e le funzionalità dell’OPC UA: un’implementazione completa
Bosch Rexroth è stata una delle prime aziende ad integrare l’OPC UA all’interno dei propri sistemi: a partire dal 2013 è lo standard di comunicazione dell’azienda. Ciò significa che Bosch Rexroth utilizza il protocollo anche per far parlare i propri sistemi e lo implementa in tutte le architetture, da quelle idrauliche a quelle dei controlli numerici. L’OPC UA è diventato il protocollo di punta dell’azienda grazie al fatto di non essere legato soltanto allo scambio dei dati in una logica di polling ma di essere invece ottimizzato con le funzionalità di Publish-Subscriber.
In Bosch Rexroth il protocollo viene usato a 360° in modo capillare: è presente nel ctrlX Automation, è di default su tutti i controlli motion a partire dal 2013, su tutti i controlli numerici dal 2015, sui controlli motion idraulici e come standard di comunicazione primario su tutti gli HMI. È utilizzato sia in lettura, sia per trasmettere i dati disponibili all’esterno nel prodotto IoT Gateway. Sarà presente anche negli azionamenti della prossima generazione con l’avvento del ctrlX Drive.
Per quanto riguarda, ad esempio, i controlli motion con il server OPC UA, Bosch Rexroth consegna ai clienti il prodotto con tante funzionalità già predefinite per semplificare il lavoro dell’utente. Il cliente riceve già disponibili tutti i parametri dei controlli, degli azionamenti e degli assi, insieme ad un elenco degli eventi e dei metodi con i quali è possibile dare i comandi agli assi senza dover scrivere codice. In altre parole, Bosch Rexroth ha costruito un’interfaccia di comunicazione completa sopra il server OPC UA. Questo consente di semplificare la costruzione degli HMI e velocizzare il processo di costruzione del software, perché una buona parte dell’interfaccia verso l’esterno è già fatta in automatico dal sistema di Bosch Rexroth.
Il ruolo dell’OPC UA nell’Industria 4.0
Avere un linguaggio comune rende facile, fruibile ed accessibile a tutti la raccolta dati da sistemi di provenienza arbitraria. Indipendentemente dal sistema specifico che si potrà avere nel proprio stabilimento o dispositivo, lo standard OPC UA fornirà all’utente un linguaggio comune per raccogliere i dati ancora più facilmente: un traguardo importante e una risorsa importantissima per lo sviluppo di una Fabbrica Intelligente.
a cura di Loris Cantarelli
Condividi l'articolo
Scegli su quale Social Network vuoi condividere