A proposito di produzione e riciclaggio batterie, Comau e Festo collaborano per gestire al meglio l’impatto ambientale collegato al fine vita delle batterie. Una collaborazione che sottolinea quanto la tecnologia sia uno strumento essenziale per lo sviluppo e l’adozione di pratiche sostenibili e a basso impatto, anche in ambito industriale.
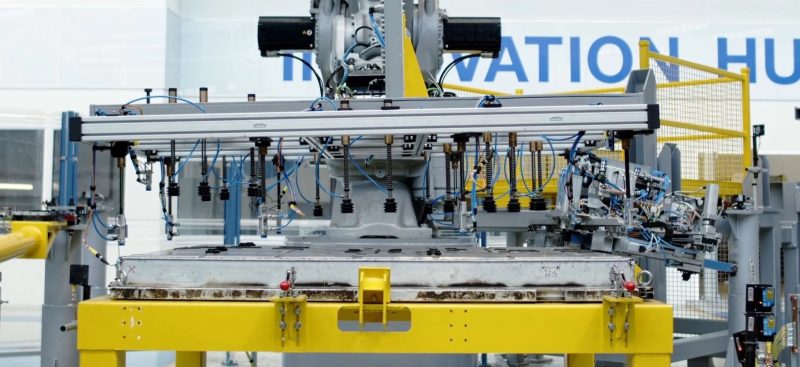
A proposito di produzione e riciclaggio batterie, Comau e Festo stanno collaborando attivamente per gestire al meglio l’impatto ambientale collegato al fine vita delle batterie, con soluzioni di automazione il disassemblaggio e il ri-assemblaggio di pacchi e moduli batteria. Una collaborazione che sottolinea quanto la tecnologia sia uno strumento essenziale per lo sviluppo e l’adozione di pratiche sostenibili e a basso impatto, anche in ambito industriale.
Con 50 anni di esperienza e una presenza globale, Comau – parte del gruppo Stellantis – è leader mondiale nella fornitura di soluzioni di automazione avanzate e sostenibili.
Oltre a progettare e sviluppare tecnologie innovative e semplici da utilizzare, “nel nostro portfolio ci sono prodotti e sistemi per la produzione di veicoli, nonché soluzioni avanzate digitali e di robotica, per rispondere alle esigenze produttive di mercati in rapida crescita, come la logistica, le energie rinnovabili e la cantieristica navale, solo per citare alcuni esempi”, racconta Francesco Beccarisi, Innovation & Process Technologies Comau.
Produzione e riciclaggio batterie
Il mercato dell’elettrificazione e della mobilità elettrica sta crescendo a ritmi sostenuti, “anche se le batterie agli ioni di litio resteranno nei prossimi 5-10 anni la tecnologia dominante, soprattutto nel settore automobilistico, il mercato inizierà ad assistere a un aumento sempre più marcato della domanda di batterie di nuova generazione, come le batterie allo stato solido”, spiega Beccarisi
Nuove tecnologie e processi di lavorazione più efficienti e sostenibili, oltre che meno onerosi, diventano necessari per supportare la produzione su larga scala di batterie di nuova generazione, con l’obiettivo di facilitare e accelerare la transizione energetica.
“La mobilità elettrica e gli importanti investimenti degli ultimi anni segnano l’inizio dell’evoluzione della mobilità”, spiega Claudio Giovando, Global Key Account Manager Automotive & Electric Vehicles Business Developer Festo.
“Oltre alle soluzioni utilizzabili per la creazione di celle, moduli batteria e motori elettrici, Festo si è interessata fin da subito alla chiusura del ciclo produttivo delle batterie stesse, in quanto processo utile a diminuire gli scarti e a favorire il riutilizzo dei materiali per produrne di nuove. Questo permetterà di ridurre l’estrazione di minerali, che essendo rari e limitati non riuscirebbero a soddisfare tutta la domanda di questo mercato in rapida espansione”.
La transizione energetica ed ecologica
La transizione energetica ed ecologica nel settore dei trasporti sta diventando realtà e il tema del riciclaggio batterie, molto attuale. “In linea con gli obiettivi di decarbonizzazione dell’Unione, la Commissione europea ha infatti adottato il pacchetto di proposte legislative ‘Fit for 55’, con cui mira a ridurre del 55% le emissioni di gas a effetto serra dei veicoli entro il 2030, arrivando al 100% entro il 2050”, conferma Beccarisi. “L’elettrificazione rappresenta, quindi, il futuro della mobilità”.
Incentivare una produzione più efficiente e sostenibile di batterie e motori elettrici è, senza dubbio, una delle sfide più importanti per le aziende attive nelle diverse fasi produttive dell’industria automobilistica e dei trasporti. “Affinché la transizione energetica sia realmente sostenibile, oltre a produrre in modo efficiente tecnologie all’avanguardia per l’elettrificazione, è necessario gestire l’impatto ambientale collegato al fine vita delle batterie stesse”, prosegue Beccarisi.
Per questo Comau ha aderito al ‘Progetto rigenerazione batterie’ promosso dalla onlus Class e da Cobat, piattaforma di servizi per l’economia circolare, “con l’obiettivo di promuovere una filiera italiana per il riciclo e il riuso delle batterie al litio”.
Flex-BD: riciclo e riuso delle batterie al litio
L’interesse per la sostenibilità ha portato Festo e Comau ad affrontare l’importante tema del riuso e riciclaggio delle batterie delle auto elettriche a fine vita. Da qui nasce Flexible Battery Dismantling (Flex-BD), ossia “lo sviluppo di una soluzione di automazione per lo smontaggio dei pacchi batteria per arrivare ai moduli”, racconta Beccarisi. “I moduli possono essere riciclati, attraverso il processo di frantumazione, per ricavare la BlackMass oppure riutilizzati per costruire nuove batterie”.
Il progetto, per il quale Comau ha ricevuto il premio innovazione nel corso di SMAU 2023, “consiste nel creare una stazione molto flessibile, in grado di disassemblare diversi tipi di batterie per veicoli elettrici”, continua Giovando. “Un’opportunità che ha messo in contatto diverse realtà europee, oltre a Festo e Comau, per creare soluzioni ad alto valore per un’economia più sostenibile”.
Le tecnologie Festo
Per realizzare la stazione Flex-BD sono state impiegate diverse tecnologie Festo, “dagli attuatori elettromeccanici con motori e azionamenti, agli avviatori progressivi certificati MS6-SV con funzione di scarico rapido che, in caso di emergenza, garantiscono la de-energizzazione della parte dell’impianto pericolosa”, spiega Giovando.
La scelta di questi componenti è stata effettuata per cercare di facilitare il riattrezzaggio e andare a compensare in modo automatico il posizionamento dei pacchi batteria. “Questo ha portato alla creazione di una stazione efficiente e innovativa, che risponde alla necessità di lavorare su differenti tipologie di pacchi batteria, riducendo gli interventi degli operatori”.
Flessibilità in primis
In tema di riciclaggio batterie, la principale caratteristica della stazione realizzata è la flessibilità, che consente di gestire differenti tipi di pacchi batteria e quindi essere potenzialmente utilizzabile da qualsiasi produttore. A questo si aggiunge l’utilizzo di soluzioni semplici e innovative, “con le quali abbiamo ridotto notevolmente i costi di realizzazione e di settaggio e il tempo ciclo, permettendo di processare un numero più elevato di componenti nello stesso arco temporale”, spiega Giovando.
“Inoltre, la stazione può anche essere utilizzata nella fase produttiva di assemblaggio dei pacchi batteria per operazioni di ripristino o sostituzione moduli identificati come difettosi, al fine di garantire come output un pacco batteria efficiente”.
Elettrovalvole VTUG a basso consumo elettrico
Tra le soluzioni utilizzate nella Flex-BD troviamo le elettrovalvole VTUG “con tempi di commutazione veloci, un basso consumo elettrico e portate elevate nonostante la loro leggerezza e compattezza, aspetto che le rende idonee per l’utilizzo in applicazioni robotiche”, continua Giovando. “Si tratta di soluzioni disponibili in diversi linguaggi di comunicazione bus, punto-punto, multi-pin, IO-Link. In particolare, la versione AP permette di creare una rete con topologia in linea, a stella o albero che comunica con il PLC cliente secondo i più diffuso bus di comunicazione”.
Per questo nella stazione troviamo CPX-AP-I nella versione Profinet che, oltre ai tempi di comunicazione rapidissimi, “permette di collegare fino a 500 componenti e integra la gestione di unità di valvole con l’auto-apprendimento della rete, così da ridurre e velocizzare sensibilmente il lavoro dei softwaristi”.
Flessibilità e adattabilità
A questa rete sono stati anche collegati due tipi di assi, ELGG a cinghia ed EGC a vite, per garantire posizionamenti precisi e, in futuro, processare moduli di diverse dimensioni. “Festo, infatti, ha indirizzato la scelta su tecnologie e soluzioni che garantissero elevata flessibilità e adattabilità”, conferma Beccarisi.
Un esempio è il muscolo pneumatico DMSP, “capace di garantire forze elevate, pur non avendo componenti meccanici con scorrimento reciproco”, spiega Giovando. “In determinate fasi, il muscolo ha permesso di recuperare velocemente tolleranze e giochi presenti nei pacchi batteria, garantendo un notevole risparmio in termini di tempo ciclo”.
Questa soluzione ha inoltre simulato “il comportamento umano per manipolare i componenti, consentendo un corretto accoppiamento tra gripper e robot, permettendo di staccare un modulo incollato applicando una forza impulsiva senza mandare in errore il robot a causa dell’urto”, continua Beccarisi.
Affrontare problemi complessi con scenari imprevedibili
“Inoltre, grazie ai motori elettrici Festo è possibile riconfigurare il gripper dei moduli. Un aspetto da non sottovalutare, in quanto smontare una batteria significa manipolare oggetti che possono avere dimensioni diverse perché nella loro vita lavorativa hanno subito deformazioni meccaniche e termiche”.
Con questo progetto “è stata messa in luce la capacità di entrambe le aziende di affrontare problemi complessi con scenari imprevedibili”, conclude Beccarisi. “Questa collaborazione ha sottolineato quanto la tecnologia sia uno strumento essenziale per lo sviluppo e l’adozione di pratiche sostenibili ed a basso impatto, anche in ambito industriale. Un approccio che consente alle imprese di fare un uso più razionale delle risorse naturali, di ridurre i consumi energetici e gli sprechi, contribuendo a preservare il Pianeta, per le generazioni attuali e future”.
a cura di Simona Recanatini
Condividi l'articolo
Scegli su quale Social Network vuoi condividere