Come le tecnologie avanzate consentono alle aziende di risparmiare tempo e denaro.
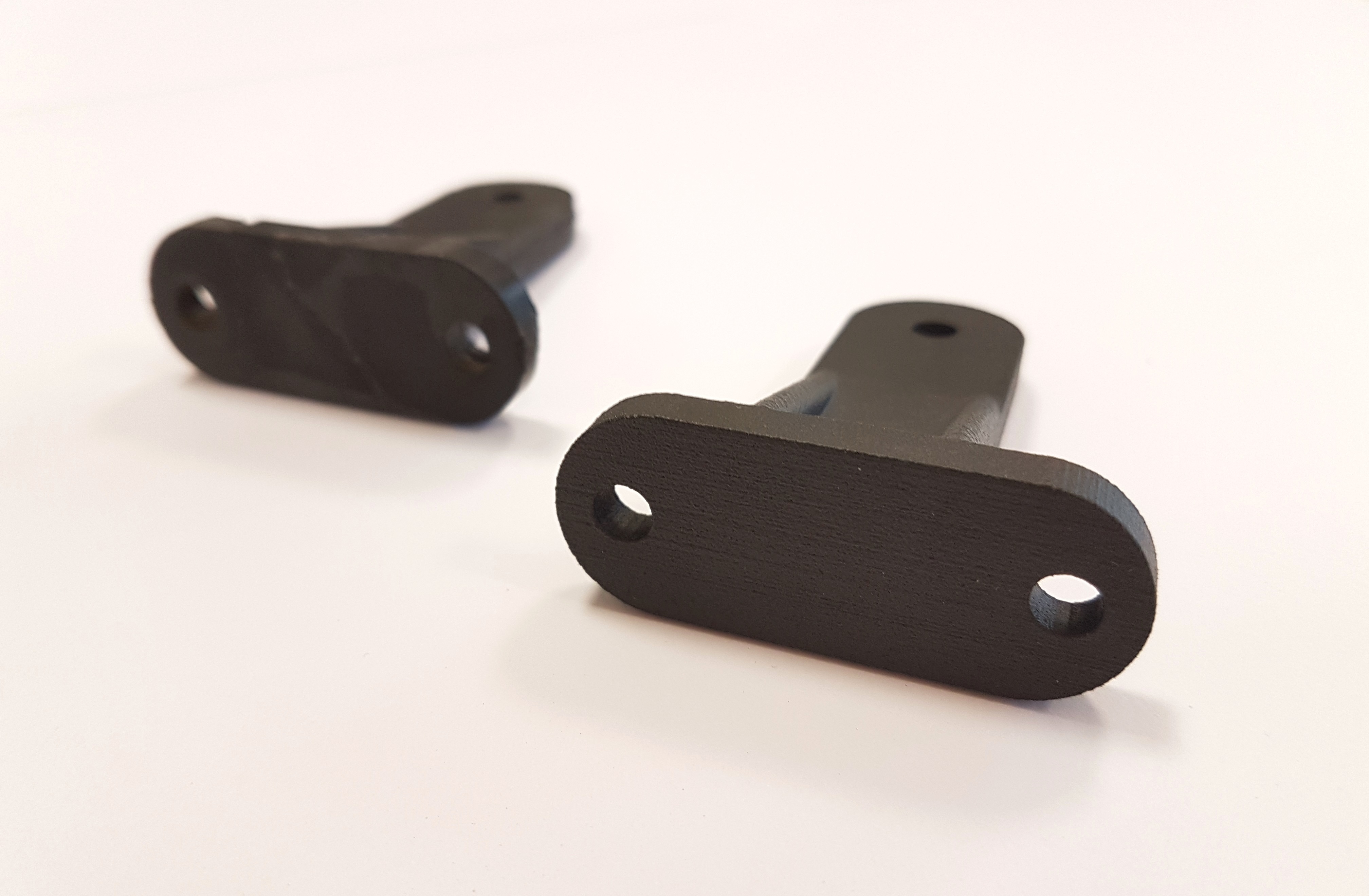
Come le tecnologie avanzate consentono alle aziende di risparmiare tempo e denaro.
Al giorno d’oggi non è facile reperire pezzi di ricambio, sia che si tratti di sostituti per componenti, meccanismi o, più in generale, dispositivi vari. Quando questa necessità investe le attrezzature di un sistema produttivo, le conseguenze possono rivelarsi dannose per l’azienda: l’attesa per il ricambio può infatti tradursi in un ritardo nel ciclo di lavoro, con ingente perdita denaro. È possibile superare questa problematica affidandosi a tecnologie e materiali avanzati: il loro sapiente utilizzo da parte di esperti permette di ricostruire in breve tempo ogni tipo di pezzo e/o particolare, consentendo un veloce ripristino dell’operatività.
Il caso applicativo che qui segnaliamo può essere preso d’esempio per spiegare meglio questo concetto e le varie fasi di ricostruzione di un particolare attraverso l’utilizzo di tecnologie innovative. È il racconto della ricostruzione di una staffa di fissaggio con attacco a T attraverso il processo di ingegneria inversa (o reverse engineering), la stampa 3D professionale (sinterizzazione laser selettiva) e materiale composito caricato fibra di carbonio.
La staffa in questione è fissata a un attuatore elettrico lineare per la movimentazione di un frangisole di grandi dimensioni. Per l’usura del tempo e il prolungato utilizzo, questo pezzo si è rotto in tre parti rendendo impossibile l’apertura e chiusura del sistema di schermatura. L’inconveniente è stato trasformato in un’occasione per attuare un test sul campo, finalizzato a dimostrare che è possibile affidarsi alle tecnologie più avanzate per creare, in tempi brevi, il sostituto di un pezzo che risulterà identico, in tutto e per tutto, all’originale.
CRP Technology, da oltre 25 anni ai vertici mondiali nel campo delle tecnologie più avanzate di stampa 3D e materiali compositi, ha messo a disposizione le sue tecnologie e soluzioni all’avanguardia per effettuare il test di ricostruzione del componente.
Il primo passo è la valutazione del file 3D del componente da costruire. Già a questo punto, però, gli esperti si sono trovati di fronte a un ostacolo: l’impossibilità di visionare il file 3D del pezzo. Grazie all’esperienza acquisita in tanti anni di attività, e alle tecnologie a disposizione internamente, il team è riuscito a superare la difficoltà affidandosi all’ingegneria inversa/reverse engineering: tale processo, infatti, consente di risalire alle geometrie dell’oggetto reale quando non si ha a disposizione la sua geometria 3D, e in seguito è possibile procedere a modifiche, adattamenti o semplicemente alla sua costruzione.
La staffa, rotta in tre parti, è stata incollata per ridarle la sua forma originaria e garantire così la corretta procedura di ingegneria inversa. Il team tecnico ha quindi applicato il processo d’ingegneria inversa, caratterizzato da alcune fasi: anzitutto il rilievo e scansione laser dell’oggetto (staffa di fissaggio). Questa fase consiste nell’acquisizione digitale delle superfici del pezzo (mesh: trama della superficie espressa da triangoli) via scanner. In questo modo si ottiene la forma 3D dell’oggetto rilevato con un grado di precisione che arriva al decimo di millimetro.
Segue la modellazione parametrica del file 3D STL e la creazione delle superfici. Dalla mesh, tramite utilizzo di software appositi, si procede alla creazione delle superfici (si tratta di superfici generate da curve espresse da modelli matematici). Le diverse parti ottenute vengono quindi unificate per generare una unica superficie che ricalca il modello originale scansionato, con una precisazione variabile da alcuni decimi di millimetro.
Ottenuto così il file STL, gli esperti han potuto procedere nella costruzione fisica del pezzo: dopo aver studiato il file, la squadra tecnica ha scelto i materiali compositi Windform Top-Line e la tecnologia di sinterizzazione laser selettiva. Come materiale di realizzazione, è stato scelto il Windform SP, materiale composito a base poliammidica caricato con fibre di carbonio della linea Top-Line di CRP Technology. Windform SP presenta elevati valori di allungamento alla rottura e di resilienza, oltre a ottime caratteristiche meccaniche e di resistenza al danneggiamento, urti e vibrazioni.
La realizzazione del pezzo, dalla scansione dell’originale alla costruzione via stampa 3D del nuovo, si è svolta in pochi giorni. Dai controlli effettuati sulla staffa, gli esperti si sono detti molto soddisfatti del risultato ottenuto. La staffa è stata comunque sottoposta a verifica dimensionale per accertarne la conformità all’originale. Terminata la fase di validazione, il pezzo in Windform è stato montato al posto di quello rotto: anche il test sul campo ha portato a ottimi risultati, e il corretto funzionamento del frangisole è stato ripristinato.
Il ricorso a tecnologie all’avanguardia ha quindi permesso la ricostruzione e messa in opera del componente in tempi brevi. Il materiale utilizzato, altamente performante, ha garantito il pieno ripristino delle funzioni originarie della struttura. L’efficacia del test effettuato dimostra che il processo di ingegneria inversa può essere applicato a molte casistiche, tra cui la difficoltà o impossibilità di trovare i pezzi di ricambio di componenti usurati o obsoleti.
Situazioni come queste sono sempre più frequenti al giorno d’oggi: l’impossibilità o i ritardi nel reperimento di tali parti di ricambio, possono compromettere la continuità del ciclo produttivo con conseguente perdita di tempo e denaro. Il processo di ingegneria inversa, unito alla stampa 3d professionale e a materiali compositi altamente performanti, consente di ricostruire e sostituire velocemente il componente usurato, consentendo al sistema di produzione di tornare subito operativo, con un ingente risparmio di tempo e denaro.
Nella foto in alto, una staffa di fissaggio a T per frangisole: sullo sfondo a sinistra l’originale rotto in tre parti e incollato, a destra il pezzo ricostruito tramite reverse engineering e sinterizzazione laser selettiva usando il materiale composito caricato fibra di carbonio Windform SP della linea Top-Line di CRP Technology.
a cura di Loris Cantarelli
Condividi l'articolo
Scegli su quale Social Network vuoi condividere