Un gemello digitale riproduce l’intero processo produttivo e permette un intervento diretto nella lavorazione in ogni momento, creando un sistema totalmente intelligente.
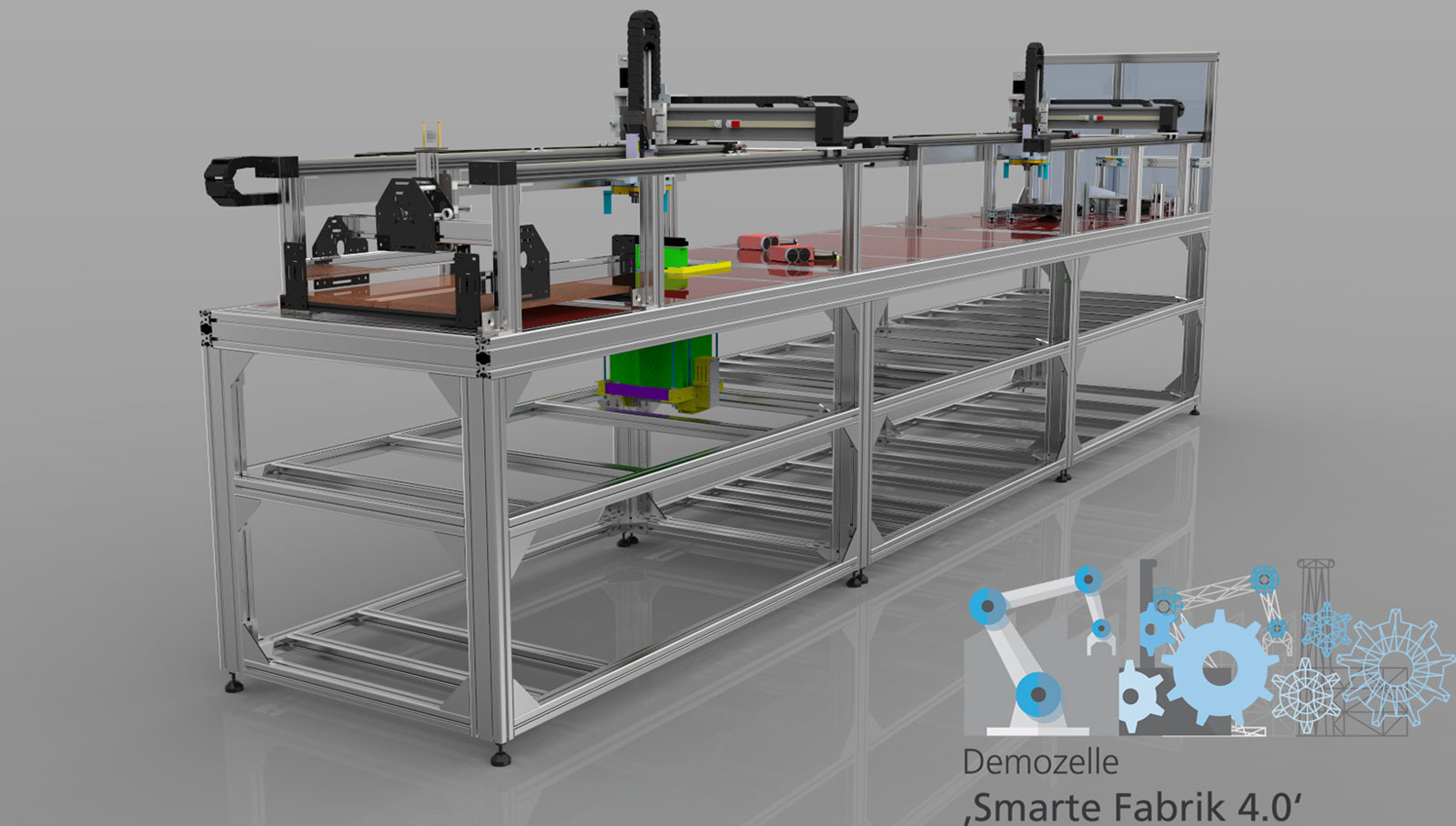
Un gemello digitale riproduce l’intero processo produttivo e permette un intervento diretto nella lavorazione in ogni momento, creando un sistema totalmente intelligente.
a cura dell’Istituto Fraunhofer IPK
Un controllo efficiente della produzione è un fattore tecnologico fondamentale nell’industria. In un primo momento, l’idea di costruire due fabbriche parallele invece di una sola può essere visto solo come un raddoppio dello sforzo. E se però una delle due fabbriche esistesse solo in forma virtuale? Questa è l’idea alla base di un concetto innovativo elaborato dall’Istituto Fraunhofer IPK per i Sistemi di produzione e le tecnologie di progettazione con sede a Berlino. La fabbrica “reale” è interamente riprodotta a livello digitale, creandone così un gemello virtuale che non solo visualizza il sistema di produzione con tutte le sue macchine, ma riproduce anche in tempo reale i processi dinamici e il comportamento dei componenti del sistema durante la produzione. Nel gemello virtuale, è possibile osservare nel dettaglio il processo produttivo. I numerosi sensori comunicano continuamente al sistema lo stato operativo delle singole stazioni di lavoro. Questo apre nuove possibilità per il controllo della produzione. I programmatori di produzione possono analizzare il processo produttivo nella simulazione virtuale e quindi ottimizzare o riorganizzare le singole fasi a seconda della necessità.
Un sistema reattivo
In ogni caso il concetto di gemello digitale va ben oltre una mera simulazione del sistema di produzione reale. Il sistema è in realtà bidirezionale. A livello virtuale, è possibile intervenire e apportare delle modifiche, che possono essere simulate immediatamente. Viceversa, si possono caricare nel gemello digitale i cambiamenti effettuati nel sistema reale. Un responsabile di produzione, per esempio, può attivare delle macchine aggiuntive per lavorare un pezzo o incorporare una fase di lavorazione aggiuntiva, nel caso in cui sia richiesta una personalizzazione. Per fare ciò, non è necessario interrompere la produzione e riconfigurarla, perché il sistema reagisce in modo intelligente alle singole modifiche e le riconosce in modo autonomo.
Unione tra produzione reale e digitale
L’unione tra la produzione reale e la produzione simulata in digitale crea un sistema complessivo che si auto-monitora, controlla e corregge senza interrompere la produzione. Ogni volta che è necessario, le macchine e il software comunicano autonomamente e mantengono attiva la produzione. Se, per esempio, interviene un errore, come il guasto di un sottosistema, il sistema può decidere autonomamente di risolvere il problema. Il supervisore si accorge del cambiamento nella produzione, ma non è obbligato a intervenire. Inoltre, considerato che il sistema continua a inviare dati al gemello digitale, è possibile tenere continuamente sotto controllo la qualità dei pezzi in lavorazione e del prodotto finale. Questa idea può anche essere usata per realizzare in tempi brevi piccoli lotti di produzione con parti personalizzate in modo tale da ridurre al minimo eventuali problemi alla produzione in generale. È persino ipotizzabile la produzione di pezzi unici (lotti di un unico pezzo) utilizzando il modello del prodotto per la creazione di un modello di produzione (ad esempio con i codici del controllo numerico).
Messa in servizio di nuovi sistemi di produzione più semplice
Un ulteriore vantaggio è che il gemello virtuale può essere usato in fase di progettazione e costruzione del sistema di produzione. Ancor prima di iniziare la lavorazione del primo pezzo, le fabbriche possono simulare in anticipo il flusso produttivo, identificarne le debolezze e ottimizzare i processi. Così facendo, il sistema viene virtualmente reso operativo e testato prima che inizi la produzione vera e propria. Questa prassi velocizza la programmazione e rende più semplice la messa in servizio di un nuovo sistema di produzione.
Di conseguenza, il progetto Fraunhofer fornisce un esempio pratico di come possa funzionare il megatrend dell’Industria 4.0. “Il nostro obiettivo non è solo quello di illustrare le tecnologie, i processi e i metodi alla base della Industria 4.0, ma di renderli davvero tangibili” dichiara il professor Rainer Stark, project manager di Fraunhofer IPK. Collaborando con i partner dell’industria, l’esperto di Fraunhofer e il suo team mirano a sviluppare progetti pilota che siano effettivamente pronti per il mercato in breve tempo. Per far sì che questa idea ambiziosa possa trasformarsi in realtà, gli esperti Fraunhofer hanno dovuto superare numerose sfide tecnologiche. Molte delle tecniche e delle applicazioni destinate al gemello virtuale non esistevano ancora, e quindi i ricercatori hanno dovuto svilupparle partendo da zero. “Vogliamo fare completamente a meno di componenti specifici e vogliamo che tutte le interfacce siano compatibili al 100% con gli standard industriali” spiega Stark. “Al tempo stesso, il sistema non deve diventare troppo costoso. Dopotutto, l’azienda deve poter recuperare l’investimento velocemente”.
Combinazione di sensori fisici e virtuali
La tecnologia dei sensori utilizzata è uno dei punti forti dal punto di vista tecnico. I ricercatori Fraunhofer usano una combinazione di sensori fisici e virtuali, grazie alla quale i sensori virtuali elaborano i dati di misurazione in complessi report sullo stato del sistema. Un elemento tecnico fondamentale è la trasmissione dei dati, che comprende un sistema ibrido per il trasferimento dei dati all’interno dell’impianto di produzione e al centro di controllo. Ciò significa che si utilizzano standard classici per i dati wireless come WLAN e LTE, e anche standard industriali come EtherCAT. Questa tecnologia è scalabile a seconda delle esigenze. È in grado di controllare sistemi singoli, ma potrebbe monitorare un’intera fabbrica. Gli unici limiti sono la potenza di calcolo e la capacità della rete, pure se anche il lavoro e lo sforzo richiesti per la riproduzione e la fedeltà ai dettagli o la precisione del gemello digitale sono anch’essi, in un certo senso, limitazioni. Infine, rimane la questione della sicurezza, che gli ingegneri hanno tenuto in particolare considerazione in fase di progettazione. L’intero sistema si muove all’interno della sua rete interna separata, che è protetta da un firewall oltre che da uno stretto controllo sulle autorizzazioni delle singole porte.
Nella figura in alto, il gemello digitale sincronizzato in tempo reale con il sistema di produzione reale. In quella qui sopra, la Fabbrica Intelligente 4.0: i pezzi lavorati vengono sollevati su un carrello a guida automatica (AGV).
a cura di Redazione
Condividi l'articolo
Scegli su quale Social Network vuoi condividere