La realizzazione di forme complesse e la riduzione del numero di componenti sono due delle opportunità offerte dalla fabbricazione additiva
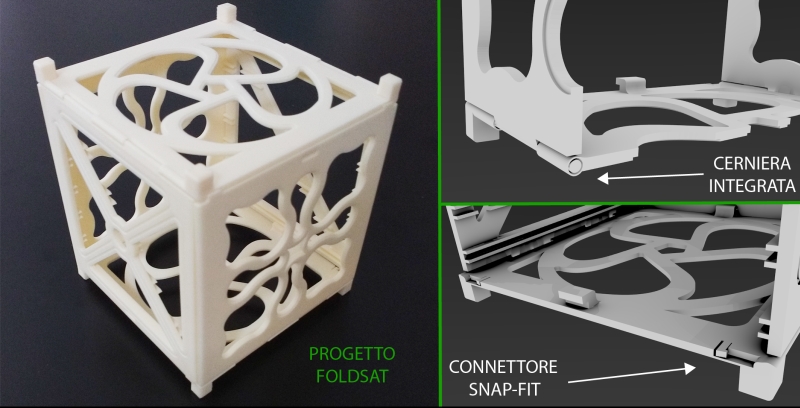
La realizzazione di forme complesse e la riduzione del numero di componenti sono due delle opportunità offerte dalla fabbricazione additiva
La complessità delle forme riproducibili mediante le tecniche di fabbricazione additiva ha abbattuto molte delle barriere che dal punto di vista geometrico hanno da sempre limitato la creatività di designer e progettisti. La progettazione, a fronte di minori vincoli geometrici, può focalizzarsi sulla funzionalità del componente e sull’utilizzo di forme più o meno complesse, non realizzabili mediante le tecnologie tradizionali. Un ulteriore vantaggio deriva dalla riduzione del numero di componenti, potendo fabbricare piccoli assiemi come un pezzo unico. A tale scopo occorre prevedere sul modello CAD opportuni giochi nei giunti o negli accoppiamenti tra le parti, che verranno realizzate già integrate. Ne deriva la possibilità di realizzare nuovi cinematismi, non soggetti ai vincoli derivanti dalla necessità di assemblare le parti che li compongono.
L’importanza dei giochi
Nella definizione dei giochi da assegnare tra le parti che si intende realizzare come assieme, è necessario considerare lo spessore di strato adottato e le caratteristiche del processo di fabbricazione additiva impiegato. Con riferimento alla produzione di componenti in materiale polimerico mediante il processo FDM, più comunemente noto come stampa 3D, occorre tenere conto della necessità di inserimento delle strutture di supporto nel volume dei giochi tra le parti. I supporti, che dovranno essere rimossi dopo la fabbricazione, possono essere realizzati nello stesso materiale del pezzo oppure in un materiale diverso. Nel primo caso, coincidente con l’uso di una macchina con un solo estrusore come la maggior parte delle stampanti 3D entry‑level, le strutture di supporto dovranno essere rimosse meccanicamente per taglio o abrasione e dunque devono essere accessibili e raggiungibili con utensili opportuni (scalpelli, sgorbie o simili). Nel caso di macchine con due o più estrusori, come tutti i sistemi industriali, è possibile fabbricare le strutture di supporto in un materiale polimerico differente da quello del pezzo. Il materiale dei supporti è generalmente solubile in una soluzione chimica che rimuove il supporto senza alterare il polimero utilizzato per il pezzo. Anche in questo secondo caso, le zone dei giunti devono essere in comunicazione con l’esterno attraverso piccoli fori, perché il bagno, nel quale viene immerso l’assemblato per alcune ore, deve poter penetrare e disciogliere il supporto.
La dimensione dei giochi tra le parti accoppiate deve essere un multiplo dello spessore di strato per consentire alla macchina di depositare almeno uno o meglio più strati del materiale di supporto. Ad esempio, adottando uno spessore di strato di 0.3 mm, i giochi dovranno essere almeno di 0.6 mm, ma il valore consigliato è di almeno 1 mm se si deve procedere manualmente alla rimozione del materiale di supporto mediante azione meccanica. Le strutture di supporto devono inoltre essere obbligatoriamente inserite qualora ci siano superfici sporgenti o aree del pezzo aggettanti rispetto alla direzione di crescita del pezzo strato su strato. Diversamente il materiale polimerico non sarebbe opportunamente supportato e tenderebbe a deformarsi o cedere sotto il proprio peso. Al fine di ridurre il volume dei supporti e abbattere i tempi di produzione è fondamentale studiare il design del componente anche in funzione del suo orientamento nel volume di lavoro della stampante 3D e della direzione di costruzione.
Soluzioni concrete
In un’ottica di progettazione per la fabbricazione additiva (Design for Additive Manufacturing – DFAM), quando possibile, è preferibile privilegiare lo sviluppo del componente nel piano di lavoro, rispetto alla sua crescita nella direzione di costruzione. Telai, involucri e in generale scatole cave all’interno, possono essere progettate con giunti o cerniere integrate che ne permettano la riduzione del numero di parti e lo sviluppo in piano ai fini della produzione. A titolo di esempio viene illustrato il progetto FoldSat (figura 1), con il quale il gruppo di ricerca sulle tecnologie additive coordinato dal Prof. Luca Iuliano del Politecnico di Torino ha vinto il primo premio del concorso “The CubeSat Challenge”. Il concorso internazionale promosso lo scorso anno dall’azienda americana Stratasys, una delle principali aziende nel mercato delle stampanti 3D industriali, richiedeva la riprogettazione del telaio di satelliti sperimentali di tipo CubeSat. Oltre duecento progetti hanno cercato di sfruttare e dimostrare i vantaggi della fabbricazione additiva per la produzione della struttura modulare CubeSat, standard di forma cubica con ingombro di 100 x 100 x 100 mm. Il telaio soggetto ai vincoli di produzione mediante le tecnologie tradizionali è generalmente composto da trenta a cinquanta parti, minuterie comprese. Il progetto FoldSat si distingue, invece, per il design pieghevole del cubo. Il telaio è composto da due sole parti, di dimensioni simili, ognuna delle quali definisce tre delle sei facce del cubo. Grazie alla presenza di cerniere integrate (figura 1), tre facce del cubo possono essere fabbricate allineate come pezzo unico all’interno del volume di lavoro di una stampante 3D. Le superfici estetiche non sono influenzate dalla presenza dei supporti, quindi la qualità estetica è la migliore coerentemente con lo spessore di strato impiegato. Inoltre il materiale polimerico viene depositato nel piano strato dopo strato, quindi la resistenza del componente viene massimizzata rispetto a quella di geometrie verticali che crescono nella direzione di costruzione e che sono maggiormente soggette alla delaminazione fra strati. Una serie di connettori snap fit (figura 1) consente di accoppiare fra di loro le due parti prodotte, dopo averle piegate grazie alle cerniere, per formare il cubo completo del telaio. La fabbricazione delle due parti nella configurazione dispiegata (figura 2a), con le facce allineate nello stesso piano, comporta una riduzione dei tempi di produzione, proporzionali al numero di strati da depositare. A seconda delle strategie di riempimento e deposizione adottate, i tempi possono essere ridotti fino al 40%, con un risparmio del materiale di supporto pari a circa il 30% rispetto alla produzione con le facce verticali (figura 2b).
Tali vantaggi, che si traducono in termini di costo, sono validi anche nel caso in cui la tecnologia produttiva sia quella della sinterizzazione laser su letto di polvere e vengono anche amplificati dalla possibilità di sfruttare il nesting 3D. Quest’ultimo corrisponde alla sovrapposizione di più pezzi nella direzione di costruzione della macchina, lasciando strati di polvere non sinterizzata tra un pezzo e l’altro con la funzione di supporto per i pezzi sovrastanti. La riduzione dell’altezza dei pezzi grazie alla configurazione dispiegata e sviluppata nel piano, consente di incrementare le quantità prodotte a parità di altezza del volume di costruzione della macchina.
a cura di Paolo Minetola
Condividi l'articolo
Scegli su quale Social Network vuoi condividere