La collaborazione fra E.ON e Dow Italia crea un circolo virtuoso.
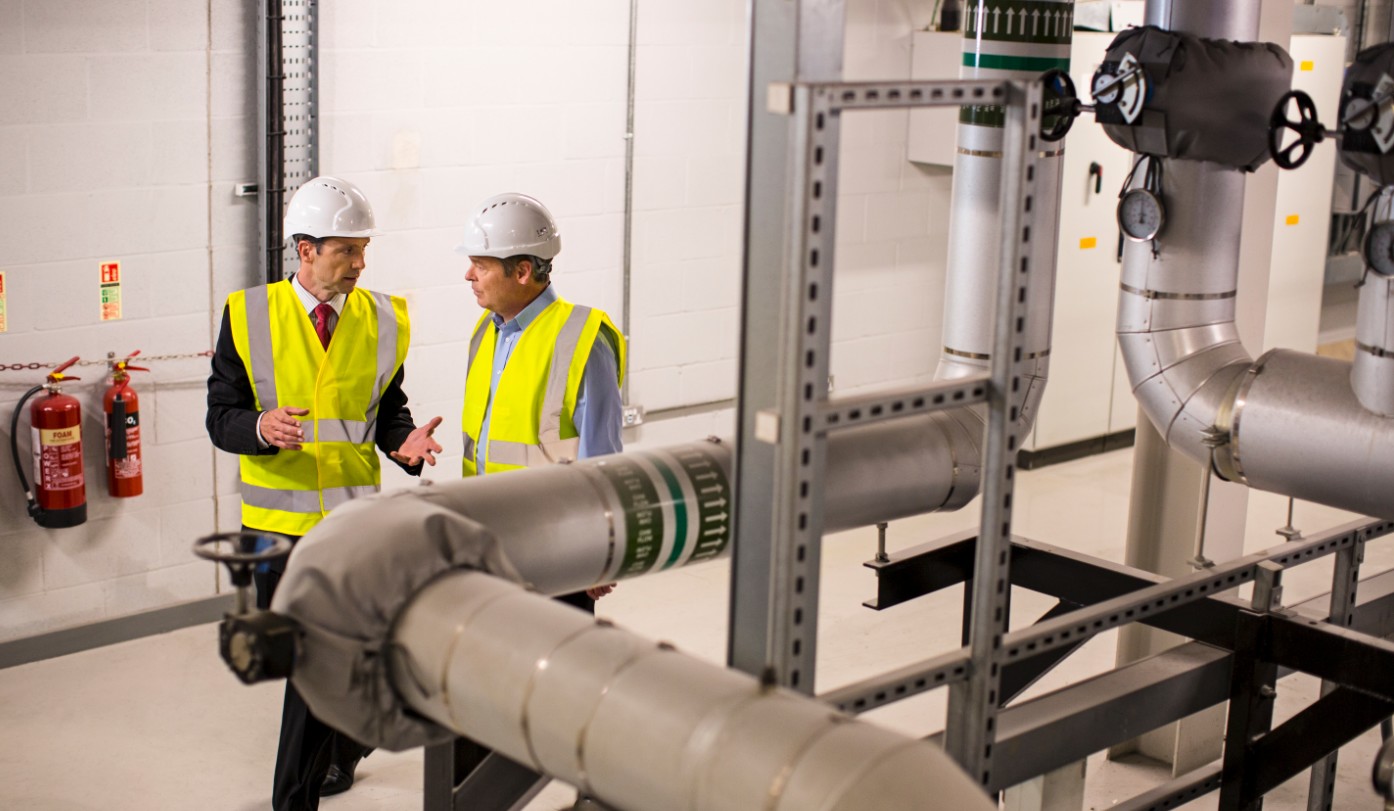
Dow Italia, consociata di The Dow Chemical Company ha scelto la cogenerazione come servizio, affidando a E.ON l’impianto di cogenerazione da 0,9 MW nello stabilimento di Correggio, dove si sviluppano e si producono sistemi poliuretanici destinati a una vasta gamma di applicazioni per importanti settori, quali costruzioni, automotive, calzature, arredamento e catena del freddo.
La cogenerazione come servizio
La corretta dicitura internazionale è BOO + PPA (Build Own Operate + Power Purchase Agreement), ma il concetto è quello della cogenerazione in modalità ESCo, secondo cui un’azienda industriale anziché acquistare un impianto di cogenerazione e assumersene l’onere di gestione, si affida a un operatore energetico specializzato che si occupa della progettazione e della realizzazione di un impianto di cogenerazione (Build), di cui è proprietario (Own) e si occupa della sua gestione operativa (Operate). L’accordo con il cliente è quindi completato da un PPA (Power Purchase Agreement) in base al quale l’operatore energetico si impegna a fornire al cliente, per un numero di anni concordato, l’energia elettrica e termica prodotta dall’impianto di cogenerazione e necessaria al funzionamento dello stabilimento.
Numerosi i vantaggi per i clienti, come la possibilità di liberare risorse economiche (che, anziché essere investite in un impianto energetico, possono essere destinate al core business aziendale) e l’assenza dei rischi derivanti dalla proprietà e dalla gestione dell’impianto, come quelli legati ai volumi di produzione, ai rendimenti, alle emissioni ed agli aspetti ambientali.
L’impianto di cogenerazione nello stabilimento Dow a Correggio (RE)
Dow Italia, consociata di The Dow Chemical Company, è presente in Italia dal 1960. Con attività di business diversificate in cui si integrano scienza e tecnologia, oggi Dow Italia produce o commercializza materie plastiche, prodotti chimici di base e specialità. In Italia, Dow può contare su una solida struttura di impianti industriali a Correggio (RE), Mozzanica (BG), Mozzate (CO) e Parona (PV).
L’azienda ha optato per la cogenerazione come servizio, affidando ad E.ON l’impianto di cogenerazione da 0,9 MW nello stabilimento di Correggio. L’impianto, produce 5,7 GWh/anno di energia elettrica e 5,1 GWh di energia termica ed è assistito in ogni momento dal servizio di gestione e assistenza di E.ON.
«Gli accordi presi con Dow – ha affermato Andrea Tomaselli, Head of Sales E.ON Business Solutions Italia – rappresentano un consolidamento del ruolo di E.ON nella fornitura di soluzioni energetiche, decentralizzate e a basso impatto ambientale, in un nuovo modello del mondo dell’energia sempre più distribuito e gestito da aziende in grado di operare su scala multi tecnologica».
«La scelta della cogenerazione – ha dichiarato Emily Marinelli, Sr. Climate Development Manager Energy per l’Europa – è in linea con il nostro impegno sulla sostenibilità ambientale. Abbiamo massima fiducia in E.ON, che ci affiancherà nel nostro percorso verso soluzioni energetiche innovative».
A fronte del contratto in essere sul tema della cogenerazione, sono nate nuove opportunità di collaborazione fra le aziende in ambito di efficientamento energetico.
Un algoritmo proprietario ottimizza l’impianto
Elemento fondamentale per la gestione del servizio da parte di E.ON è il sistema di ottimizzazione del regime di operatività dell’impianto basato su un algoritmo proprietario, che analizza 24 ore su 24, in tempo reale, i dati di funzionalità: produzione di elettricità, di energia termica e/o energia frigorifera, mettendola in relazione con le richieste dello stabilimento, con le condizioni della rete elettrica e con altri parametri quali ad esempio le previsioni meteo.
In un ciclo produttivo infatti, il fabbisogno di elettricità, di calore e/o di freddo non è costante, ma varia nel tempo: per questo è necessario, oltre al monitoraggio dei consumi, valutare le previsioni di fabbisogno di energia elettrica e termica nei giorni successivi, possibili attraverso sistemi di calcolo predittivo che analizzano i profili storici di consumo. La capacità di monitorare e gestire da remoto la correlazione fra produzione dei singoli vettori energetici e il fabbisogno puntuale e futuro dello stabilimento garantisce che l’impianto soddisfi in ogni momento le esigenze produttive e una gestione ottimale dello stesso.
a cura di Loris Cantarelli
Condividi l'articolo
Scegli su quale Social Network vuoi condividere