Le differenti strategie di manutenzione per i sistemi produttivi nei contesti industriali: affrontiamo questo tema analizzando gli obiettivi della manutenzione, le tipologie di guasto e le principali strategie manutentive normalmente impiegate negli impianti industriali.
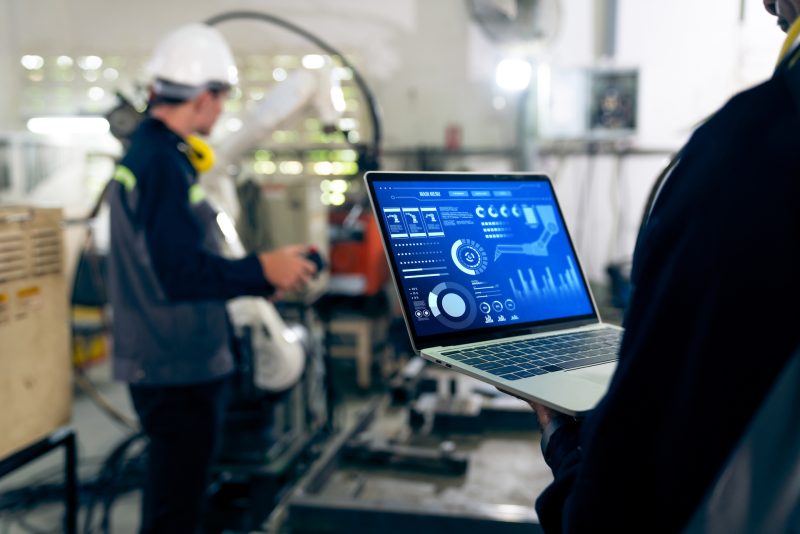
Quali sono le differenti strategie di manutenzione per i sistemi produttivi? Innanzitutto, il termine manutenzione deriva dal latino “manu tenere”, ovvero “tenere con la mano”. Nonostante si tratti di un concetto comunemente utilizzato nella vita di tutti i giorni, assume una connotazione ben specifica se configurato nella gestione delle risorse produttive nei contesti industriali.
In sintesi, le risorse produttive come ad esempio attrezzature, macchine e impianti sono normalmente soggette a un inevitabile calo di prestazioni nel tempo e possono quindi operare con condizioni ridotte rispetto a quelle nominali. Questo decadimento è dovuto principalmente a fenomeni di usura e invecchiamento che degradano l’efficienza, la sicurezza e il valore di tali risorse.
Secondo la definizione data dalla norma UNI EN 13306, per manutenzione si intende una combinazione di azioni tecniche, amministrative e manageriali, effettuate durante il ciclo di vita di un’entità, e volte a mantenerla o a riportarla a uno stato tale per cui essa possa svolgere la funzione richiesta.
Le differenti strategie di manutenzione per i sistemi produttivi
Nella pratica, l’obiettivo principale della manutenzione è quello di garantire il funzionamento nominale dell’entità e di ridurre al minimo i tempi di inattività dovuti a guasti e alle conseguenti riparazioni.
Questo significa implementare delle azioni correttive, basate su di una certa strategia manutentiva, necessarie a mitigare l’effetto del decadimento delle risorse produttive al fine di riportare, qualora necessario, le prestazioni all’interno di un determinato intervallo di accettabilità.
Questo implica la sostituzione o riparazione di quei componenti che non operano secondo le specifiche progettuali e sono quindi considerabili come “guasti”. Chiaramente, una corretta manutenzione impatterà positivamente sull’affidabilità dei sistemi produttivi in termini sociali (mantenendo elevati livelli di sicurezza), tecnologici (garantendo adeguata efficienza e qualità dei processi), ed economici (estendendo la vita utile delle risorse e minimizzando i fermi impianto).
Le tipologie di guasto
I moderni impianti produttivi sono caratterizzati da macchine avanzate e configurabili come sistemi meccatronici, ovvero composti da parti meccaniche, elettriche ed elettroniche, oltre che dal software. Questo implica che un potenziale guasto possa inficiare le componenti meccaniche, come anche quelle di azionamento e controllo.
Da un punto di vista dell’affidabilità, vi sono delle sostanziali differenze.
I componenti meccanici hanno la funzione di sopportare o trasmettere carichi e sono quindi sottoposti a sollecitazioni. Questi presentano un “effetto memoria”, ovvero sono caratterizzati da un tasso di guasto non costante che dipende dalla durata della missione del componente.
Questa proprietà deriva dalla natura non casuale del meccanismo di guasto, che varia in funzione di fenomeni di degradazione come usura, corrosione, fatica, ecc. I componenti elettronici sono considerati sistemi complessi composti da un numero elevato di elementi diversi e interconnessi. Questa condizione rende l’analisi del guasto più complessa rispetto a un componente meccanico.
Elettrico o meccanico
In prima approssimazione, il profilo di guasto di un componente elettronico può essere considerato costante poiché esso è composto da una moltitudine di sottocomponenti, ognuno caratterizzato da un proprio profilo di guasto individuale e specifico.
Di conseguenza, a differenza dei componenti meccanici, quelli elettronici non hanno un “effetto memoria”, ovvero il tasso di guasto non dipende dalla durata della missione del componente.
Il software non è soggetto a una degradazione delle proprietà nel tempo e/o a guasti causati da condizioni ambientali o operative. Inoltre, la frequenza di utilizzo non influisce sulla probabilità di guasto.
Pertanto, un guasto può essere interpretato come la probabilità di manifestazione di un errore derivante da una certa combinazione di input che porta a un output non previsto e pericoloso. La massima affidabilità viene raggiunta dopo un periodo di rodaggio che permette la graduale individuazione e correzione degli errori tramite aggiornamenti.
La manutenzione correttiva
Essenzialmente, è possibile classificare le strategie manutentive in due grandi famiglie: quella correttiva e quella preventiva.
La manutenzione correttiva si effettua a posteriori, ovvero dopo che è avvenuto un guasto, con lo scopo di sostituire o ripristinare il componente interessato al fine di permettere all’entità di svolgere correttamente la funzione richiesta. Non sono quindi previste attività di pianificazione per ottimizzare la manutenzione e fornire supporto decisionale.
La manutenzione correttiva può essere vantaggiosa in situazioni in cui il profilo di guasto è caratterizzato da mortalità infantile, ovvero per i componenti caratterizzati da tassi di guasto decrescenti, oltre che nel caso in cui i guasti siano facilmente riparabili e non influenzino la capacità produttiva.
Tuttavia, questo approccio può comportare perdite economiche dovute a fermi macchinata prolungati, complessità tecniche e organizzative legate all’imprevedibilità dei guasti, oltre che l’aumento dei costi di riparazione causato da guasti non gestiti tempestivamente e capaci di danneggiare conseguentemente altri componenti del sistema.
La manutenzione preventiva
La manutenzione preventiva viene eseguita a intervalli pianificati o sulla base dell’analisi di criteri predefiniti con lo scopo di ridurre la probabilità di guasto. Semplificando, questo approccio è implementabile in tre modi.
Nel caso della “Manutenzione preventiva basata sull’affidabilità” è prevista l’analisi di dati storici al fine di attivare azioni preventive basate sull’utilizzo del componente, ovvero che considerano le effettive ore di funzionamento, oppure sul tempo, ovvero che seguono una schedulazione a calendario.
Nel caso della “Manutenzione preventiva basata sulle condizioni” è previsto il monitoraggio continuo delle condizioni e delle prestazioni dell’entità. Si analizzano i parametri delle funzioni del sistema per rilevare qualsiasi deterioramento delle prestazioni al fine di intervenire di conseguenza.
Infine, nel caso della “Manutenzione predittiva”, viene avviata un’azione correttiva solamente a seguito della rilevazione ed elaborazione di uno o più parametri utilizzando simulazioni (basate su modelli matematici avanzati) allo scopo di stimare la vita residua del componente prima del guasto.
L’importanza del contesto operativo
In sintesi, sia la manutenzione preventiva basata sull’ affidabilità che quella predittiva mirano a ottimizzare le attività di manutenzione concentrandosi sull’analisi delle condizioni dell’entità.
Ciò nonostante, la prima prevede un monitoraggio al fine di avviare azioni correttive basate sul confronto dello stato attuale con determinate soglie di intervento, mentre la seconda utilizza analisi previsionali per stimare l’insorgenza di guasti e pianificare azioni correttive in modo proattivo.
In generale, non esiste una strategia di manutenzione migliore di altre. L’efficacia dipende dal contesto operativo, dagli obiettivi aziendali, dalla disponibilità di risorse tecniche ed organizzative, oltre che chiaramente dalle condizioni del sistema produttivo.
È quindi spesso richiesta una bilanciata combinazione di diversi approcci di tipo correttivo e preventivo al fine di gestire e preservare al meglio le risorse produttive.
(a cura di Luca Gualtieri)
a cura di Simona Recanatini
Condividi l'articolo
Scegli su quale Social Network vuoi condividere