Capiamo come declinare i principi lean in ambito logistico per un’azienda che lavora su commessa
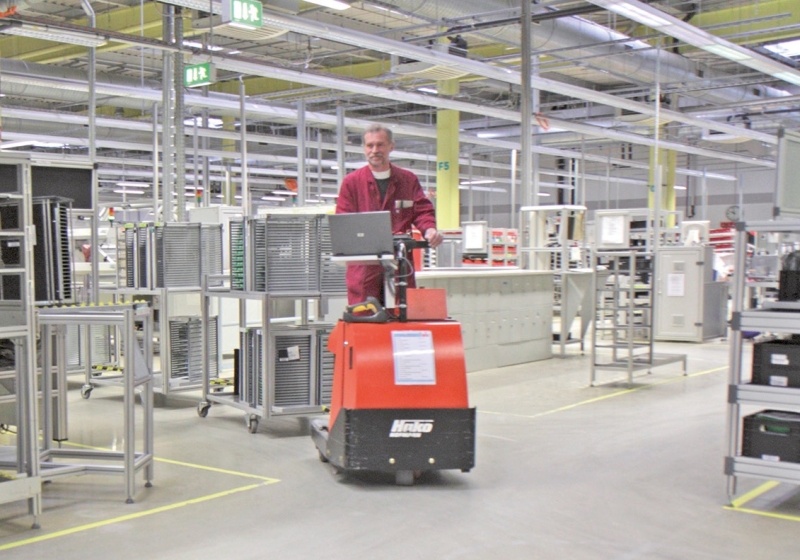
Molte aziende stanno applicando i principi del lean thinking (eliminazione degli sprechi, focalizzazione sul valore aggiunto, aumento della produttività riduzione del tempo di attraversamento). La Lean Logistic è la declinazione di questi principi in ambito logistico. Il principio fondamentale è il raggiungimento delle 5G:
1. il giusto pezzo,
2. la giusta qualità,
3. la giusta quantità,
4. al momento giusto
5. e al posto giusto
La lean Logistic comprende due aspetti differenti:
· la programmazione della produzione e dell’approvvigionamento con l’abbandono delle tecniche Push e l’adozione del Pull;
· la gestione del flusso dei materiali con un elevato impegno alla sincronizzazione dei flussi di materiali per evitare sprechi nel processo.
Lean Logistic: la programmazione
In un’azienda che produce su commessa ed in genere con tempi di risposta al cliente medio-lunghi, dovrebbe essere semplice ordinare a fronte del fabbisogno solo ciò che è necessario, nella realtà spesso le cose non stanno così. Accorciamento dei tempi di consegna richiesti dai clienti, lunghi tempi di approvvigionamento di alcuni componenti e ritardi durante lo sviluppo tecnico della commessa, a volte dovuti anche ad incertezze nelle specifiche cliente, fanno sì che spesso il tempo residuo per l’approvvigionamento materiali sia inferiore ai normali lead-time di consegna con il conseguente rischio di mettere a rischio la data di consegna finale.
Le soluzioni da mettere in atto sono:
· Semplificare e standardizzare. Definendo sottogruppi o componenti che possano essere acquisiti indipendentemente dal processo di sviluppo e concordando con fornitori preventivamente individuati tempi di approvvigionamento brevi. Trattandosi di prodotti standard può essere concordato un piano di consegne da ritarare con le esigenze produttive. Un’ulteriore semplificazione è quella di gestire “a scorta” i componenti più comuni riservando gli sforzi di gestione degli approvvigionamenti ai componenti più critici.
· Definire le milestones per l’approvvigionamento e controllare i tempi di sviluppo. Nelle prime fasi di pianificazione di una commessa devono essere subito coinvolti gli enti preposti all’approvvigionamento dei materiali e devono essere chiariti quali sono i limiti per il rilascio delle informazioni necessarie alla corretta gestione degli approvvigionamenti. Il project management dovrà quindi verificare il rispetto di queste milestones per garantire il corretto sviluppo del processo di approvvigionamento.
· Ritardare le personalizzazioni. Per quanto possibile ogni sottogruppo o componente dovrebbe essere sviluppato da una soluzione standard con personalizzazioni da apportare nelle ultime fasi. In questo modo si può cominciare l’acquisizione definendo successivamente i dettagli per la personalizzazione.
· Definire il flusso del valore . Per ogni sottogruppo e componente deve essere noto il processo di realizzazione affinché sia chiaro con quale anticipo devono essere fornite le diverse informazioni per l’approvvigionamento: spesso non è necessario avere subito a disposizione i disegni definitivi per iniziare il processo di acquisizione. Tali informazioni andranno poi utilizzate per definire correttamente le milestones di commessa.
· Dare visibilità ai fornitori. I fornitori andrebbero coinvolti il più presto possibile affinché possano iniziare le attività di acquisizione dei materiali anche se non sono ancora completamente definite le specifiche finali, in alcuni casi è utile condividere anche le previsioni di vendita e concordare un piano di approvvigionamento che garantisca anche i materiali a lunghissimo lead-time, fatta salva la condizione che si tratti di materiali non sviluppati specificatamente per la commessa. na volta messe in atto queste misure dovrebbe essere possibile far sì che tutto il processo di approvvigionamento sia “tirato” dai fabbisogni derivanti dallo sviluppo dei requisiti cliente, garantendo il rispetto dei tempi di consegna ed evitando il rischio di materiale a scorta non utilizzabile.
Lean Logistic: come gestire il flusso di materiali
L’obiettivo principale per la Lean Logistic è la separazione del Valore Aggiunto dallo Spreco e la riduzione o eliminazione di quest’ultimo. Lo stoccaggio, la movimentazione, la ricerca dei componenti sono spreco, vanno quindi minimizzati e in ogni modo separati dalle attività a valore aggiunto di lavorazione e montaggio.
Il sistema di gestione del flusso dei materiali va quindi studiato in particolare per:
· Sincronizzare le attività di preparazione. Definita una sequenza di fasi di lavorazione e montaggio per ogni commessa, ed associato a ciascuna fase una lista di prelievo o meglio un kit di componenti, le attività di preparazione dovranno seguire la medesima sequenza pilotate da un segnale proveniente dall’area di montaggio. Una modalità per fare questo è la cosiddetta Supply Chain Action Board dove sono elencate le diverse commesse e per ognuna di queste sono apposti cartellini indicanti i kit legati alla sequenza produttiva, raggiunta una fase della sequenza il cartellino viene staccato ed inviato al magazzino per la preparazione.
· Sincronizzare i fornitori. La sincronizzazione dei materiali dovrà possibilmente estendersi ai fornitori, dove, anche a fronte di un ordine per un componente personalizzato emesso in anticipo, il segnale per la consegna sarà generato dall’avanzamento produttivo. In una condizione ideale il fornitore possibilmente responsabile della fornitura di un kit di componenti o sottogruppi, sarà già in possesso della sequenza produttiva e dovrà mantenere sempre disponibile una coda di kit pronti per la spedizione, al momento del ricevimento di un cartellino staccato dalla Supply Chain Action Board, consegnerà il relativo kit e sarà autorizzato a predisporre un nuovo kit da inserire nella sequenza.
· Progettare il sistema di trasporto e deposito dei materiali dal magazzino ai posti di lavoro. Al fine di evitare sprechi per ricerche attese e movimentazioni, i materiali dovranno arrivare sul posto di lavoro al momento giusto, nella quantità giusta e possibilmente sistemati nel modo corretto per facilitarne la presa e il montaggio. Il sistema di alimentazione dei materiali alle linee non può quindi essere improvvisato, ma deve essere preventivamente progettato ed organizzato con l’adozione se necessario di contenitori o carrelli specifici ove il materiale sarà disposto nel modo ottimale per il prelievo secondo la sequenza di montaggio. In un’azienda che produce su commessa, vista la bassa ripetitività, non è sempre facile studiare preventivamente il sistema di alimentazione, ma in ogni caso è da evitare la situazione, spesso presente, in cui i materiali arrivano sulle piazzole di montaggio con largo anticipo direttamente dall’ingresso merci generando confusione, perdite di tempo, saturazione delle aree e possibilità di smarrimenti.
Lo sforzo di progettazione del sistema sarà ampiamente ripagato dai vantaggi in termine di riduzione degli sprechi, delle possibilità di errore e dei tempi di attraversamento della commessa in produzione.
L’articolo è realizzato da Paolo Naj, Senior Expert e Partner Staufen Italia, società di consulenza internazionale specializzata nei metodi di Lean Management e del Turnaround e Interim Management
a cura di Redazione
Condividi l'articolo
Scegli su quale Social Network vuoi condividere