Rigoni di Asiago è un’azienda di alto livello qualitativo che da oltre 15 anni possiede una propria filiera, grazie ad accordi pluriennali siglati con agricoltori e apicoltori bio, e controlla quindi tutti i processi di lavorazione, dalla coltivazione della materia prima fino all’imballaggio del prodotto finito. Nel sito produttivo di Foza, sull’Altopiano di Asiago, vengono lavorate ogni anno circa 6 mila t di frutta, con una capacità di invasatura corrispondente a circa 8 mila unità l’ora. La società dispone anche di un centro logistico ad Albaredo d’Adige, nei pressi di Verona, nel quale viene stoccato il prodotto finito. Rigoni di Asiago possiede inoltre, in Bulgaria, 2.000 ettari di terreni interamente dedicati all’agricoltura biologica dove coltiva e raccoglie molta della frutta utilizzata nella preparazione dei propri prodotti. La produzione annuale è di circa 3.000 tonnellate tra fragole, frutti di bosco, more, prugne, ciliegie, visciole, lamponi, ribes, uva spina, mele, mirtilli e prugnole.
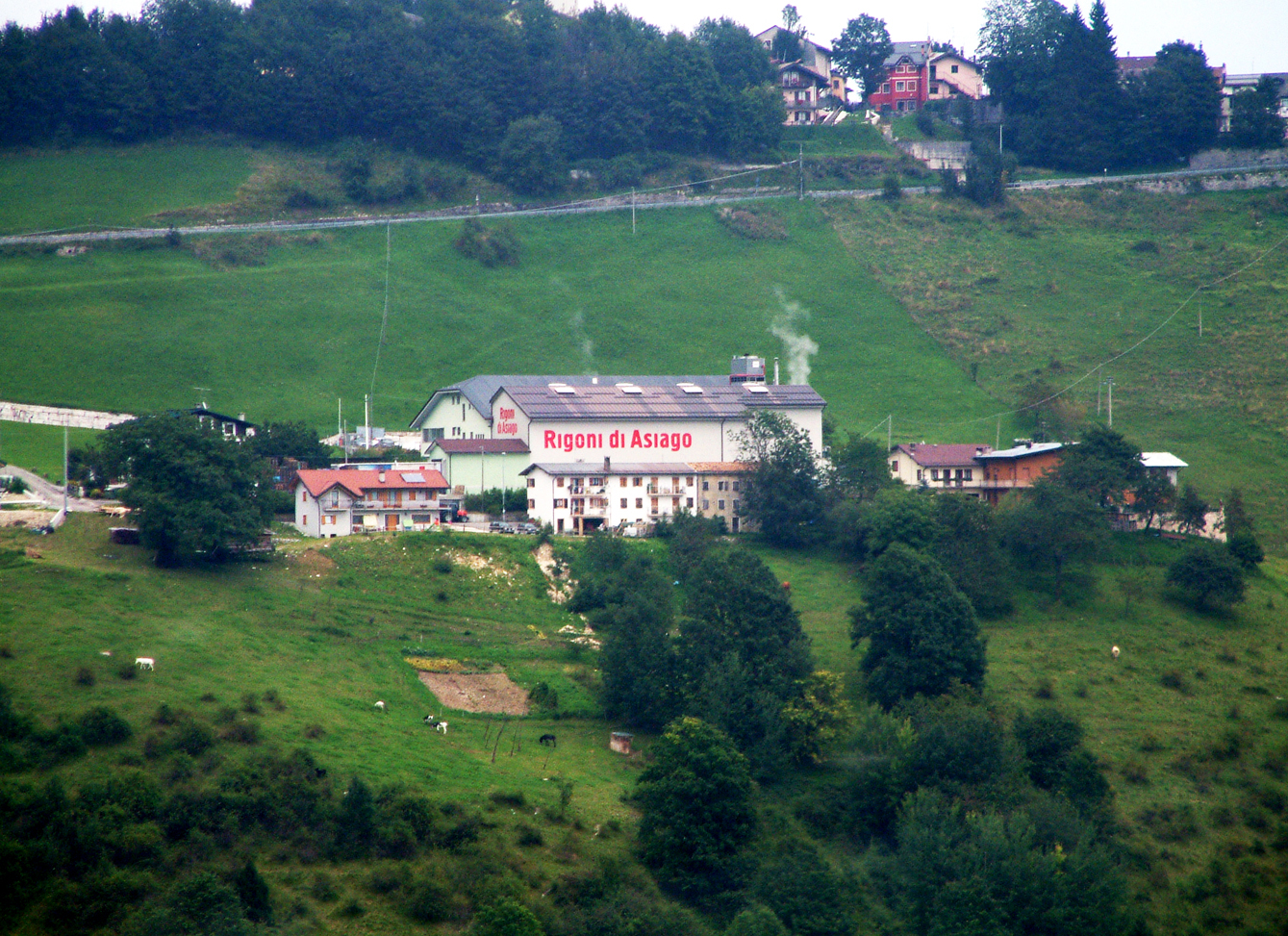
Rigoni di Asiago ha portato a termine il suo progetto pionieristico di fabbrica intelligente. Tutti gli obiettivi sono stati raggiunti con importanti, e a volte inattesi, vantaggi economici.
di Ernesto Imperio
«Mi piacerebbe avere un sistema di produzione in grado di controllare i processi di produzione, gestire la tracciabilità, fornire i dati alla contabilità per avere i costi di produzione, organizzare la pianificazione, controllare le manutenzioni, avere il monitoraggio energetico, il controllo del personale sulle linee di produzione, l’interfaccia con l’ERP e un’avanzata automazione industriale». Con queste parole Andrea Rigoni, amministratore delegato della società alimentare Rigoni di Asiago, aveva incaricato la FB Engineering di implementare soluzioni di automazione, hardware e software, per realizzare una fabbrica intelligente; una richiesta lungimirante, quella dell’amministratore delegato, che anticipava di qualche anno quello che oggi potrebbe essere contestualizzato nell’attuale domanda di tecnologie Industria 4.0.
Partner nel progetto è stata FB Engineering, società che vanta una pluriennale esperienza nel settore alimentare e si rivolge alla media e grande azienda con un proprio prodotto, denominato Sussidiario, che si configura come un software gestionale con decine di applicazioni nelle più importanti aziende italiane del settore. L’obiettivo di FB Engineering, sfruttando le grandi possibilità del proprio software, è proprio quello di aiutare i clienti nel potenziare e facilitare la produzione intervenendo su tutta la filiera produttiva, migliorando altresì l’interazione con clienti, partner, fornitori e dipendenti. Questo obiettivo è stato raggiunto anche in Rigoni di Asiago, azienda vicentina che svolge attività di produzione e commercio nel mercato alimentare proponendo prodotti esclusivamente provenienti da agricoltura biologica. Alla tradizionale produzione di miele, l’azienda ha affiancato con successo marmellate, dolcificanti naturali e creme al cacao e nocciole, tutti prodotti di alta qualità che hanno conquistato i primi posti nei dati di vendita nazionali.
Biologico, sostenibile, etico
Il progetto “Fabbrica Intelligente – Processo di acquisizione dati in un impianto di produzione marmellata” di recente portato a termine negli stabilimenti della Rigoni di Asiago ha restituito al mercato una solida realtà produttiva, finanziariamente e commercialmente in crescita, che ha saputo ottimizzare tutte le attività aziendale, dalla produzione alla logistica, dalla contabilità alla gestione del personale, salvaguardando rigorosamente i suoi valori che attengono alla produzione biologica e sostenibile e all’impegno etico e sociale, inteso come rispetto e valorizzazione di ogni singolo lavoratore, riponendo massima attenzione in materia di salute e sicurezza sul luogo di lavoro. L’azienda vicentina, che si avvale di 100 dipendenti e che ha registrato nel 2015 un ulteriore aumento di fatturato attestandosi sui 116 milioni di euro, opera dedicando costante attenzione alla riduzione dell’impatto della produzione sull’ambiente, a riguardo specialmente del consumo di combustibile fossile e dell’emissione di gas serra, ma anche alla riduzione dei consumi di acqua e dell’uso intensivo dei terreni. In quest’ottica si inseriscono alcuni importanti investimenti come il sistema di cogenerazione installato nel sito produttivo di Foza (VI) che produce acqua calda ed energia elettrica partendo dal metano, riducendo il consumo di combustibile. L’intera produzione opera con un basso consumo energetico; tutta l’energia utilizzata negli stabilimenti e negli uffici proviene infatti da fonti rinnovabili.
Dall’architettura all’implementazione
In questo virtuoso scenario industriale, s’inserisce il progetto già citato che ha visto un lavoro di quasi tre anni di analisi, studio e implementazione a partire dalla definizione dell’architettura del sistema. Questa si basava su una serie di macchine già presenti nello stabilimento, tutte dotate di PLC, di set-up automatico e di collegamento Internet, quindi predisposte all’interconnessione, che dovevano comunicare con un’intelligenza centrale che riuscisse a ricevere e inviare dati dalle/alle macchine stesse relativamente allo specifico ciclo di produzione e di prodotto da realizzare, allo scopo di poterle programmare e controllare. Inoltre, serviva un sistema che garantisse la raccolta di tutti quei dati di campo che non finivano all’interno delle macchine e dei dati sui consumi energetici. Il tutto, poi, doveva essere interfacciato con il sistema ERP di cui l’azienda era dotata.
«Per dare una risposta a tutte le richieste del signor Rigoni – ha spiegato Fabio Bulgarelli di FB Engineering – abbiamo ritenuto necessario preparare una soluzione integrata che prevedesse: uno specifico MES per il mondo alimentare che è il nostro prodotto Sussidiario; un supervisore che garantisse il controllo dell’energia, in particolare il prodotto Aprol EnMon, una soluzione integrata completa per il monitoraggio dei consumi energetici che viene fornita preinstallata su un pc industriale B&R Automation. Aprol EnMon ha solo pochi parametri da impostare prima di iniziare la raccolta dei dati. Una volta configurata è poi possibile usufruire, in modo semplice e affidabile, delle numerose opzioni per l’analisi dei consumi. Oltre all’effettiva riduzione dei costi energetici, ottenuta attivando i cicli di produzione e le relative macchine in base alle fasce di costo orarie previste dal fornitore di energia, un altro dei benefici ottenuti dall’utilizzo di questo sistema di monitoraggio energetico è stato quello di potere differenziare i costi dell’energia in base al tipo di prodotto realizzato. Con questa nuova e più precisa modalità di rilevazione dei costi energetici l’azienda ha rivisto anche le politiche produttive. In passato, la soluzione era quella di spalmare la bolletta elettrica complessiva su tutta la produzione, senza alcuna differenziazione rispetto al prodotto». In questa nuova architettura un ruolo importante è stato affidato al pacchetto Sussidiario, che ricordiamo è stato sviluppato appositamente per gestire impianti di lavorazione di conserve, marmellate, frutta, verdura e altri prodotti della filiera agroalimentare e per interfacciarsi in produzione con le linee di lavorazione con le pesoprezzatrici e le bilance in genere, con le etichettatrici e i marcatori a inchiostro, con i magazzini automatici e altro ancora.
«Nello stabilimento Rigoni di Foza, inoltre, abbiamo installato 21 PC industriali – ha aggiunto Bulgarelli – che sono stati posti nelle aree ritenute fondamentali per la programmazione delle macchine e per la raccolta dei dati. Così facendo siamo riusciti a fare sì che l’azienda potesse avere, in tempo reale, dei riferimenti per sapere un’ampia serie di informazione: il grado di produttività, il grado di efficienza, l’overfilling, cioè il sovrappeso di ogni confezione di prodotto, le informazioni sui fermi macchina, le informazioni sui capi linea e sul personale presente su ogni linea attraverso sistemi automatici di identificazione, informazioni sul ciclo pianificato, sulla ricetta, sul prodotto che si sta producendo, il numero di pezzi passati, il numero di pezzi controllati, di quelli accettati e di quelli scartati e altri dati ancora. In sostanza, siamo riusciti a monitorare in tempo reale tutto quello che succede sulle linee, consentendo così eventuali interventi correttivi in maniera più o meno immediata».
Conoscere per migliorare
Una serie di cruscotti, attivati nel sistema di interconnessione di tutte le risorse di fabbrica per monitorare una molteplicità di dati, ha consentito di rilevare alcune inefficienze congenite degli impianti produttivi favorendo così adeguati interventi correttivi.
Tra questi, particolarmente interessante è stato il dato sull’efficienza del sistema produttivo che, prima del progetto Fabbrica Intelligente, era ritenuta adeguata; ciò era dovuto al fatto che i fermi macchina inferiori ai 5 minuti non venivano segnalati. Con il nuovo sistema, che acquisisce in tempo reale i dati di tutte le macchine e registra i fermi macchina superiori ai 10 secondi, si è visto che l’efficienza effettiva era di circa il 69%. Conoscendo puntualmente le cause dei fermi macchina è stato facile intervenire sulle macchine stesse e ovviare alle cause che li generavano, migliorando sensibilmente la capacità produttiva dello stabilimento.
In definitiva, la Rigoni di Asiago può considerarsi a tutti gli effetti un’Industria 4.0 che ha saputo sfruttare le potenzialità delle attuali tecnologie disponibili sul mercato e giovarsi delle competenze della FB Engineering per ottenere una serie di vantaggi sia economici che produttivi e commerciali; questi si possono sintetizzare in capacità di produzione aumentata del 40% con lo stesso numero di persone, ottenimento delle più importanti certificazioni per l’esportazione dei prodotti, forte riduzione del consumo energetico, riduzione dell’overfilling (eccessivo riempimento delle confezioni) del 4%, incremento della produttività dell’8%, riduzione delle inefficienze del 6%, possibilità di valutare i costi per materia prima, personale ed energia di ogni singolo lotto di produzione dopo due ore dalla fine della lavorazione.
Filiera completa con prodotti biologici
Rigoni di Asiago è un’azienda di alto livello qualitativo che da oltre 15 anni possiede una propria filiera, grazie ad accordi pluriennali siglati con agricoltori e apicoltori bio, e controlla quindi tutti i processi di lavorazione, dalla coltivazione della materia prima fino all’imballaggio del prodotto finito. Nel sito produttivo di Foza, sull’Altopiano di Asiago, vengono lavorate ogni anno circa 6 mila t di frutta, con una capacità di invasatura corrispondente a circa 8 mila unità l’ora. La società dispone anche di un centro logistico ad Albaredo d’Adige, nei pressi di Verona, nel quale viene stoccato il prodotto finito. Rigoni di Asiago possiede inoltre, in Bulgaria, 2.000 ettari di terreni interamente dedicati all’agricoltura biologica dove coltiva e raccoglie molta della frutta utilizzata nella preparazione dei propri prodotti. La produzione annuale è di circa 3.000 tonnellate tra fragole, frutti di bosco, more, prugne, ciliegie, visciole, lamponi, ribes, uva spina, mele, mirtilli e prugnole.
a cura di Redazione
Condividi l'articolo
Scegli su quale Social Network vuoi condividere