Gli incentivi fiscali non sono più validi soltanto per chi acquista macchine e impianti 4.0, ma anche per chi progetta e ne realizza digitali e sostenibili: un Innovation Talk in streaming di Schneider Electric ha spiegato come.
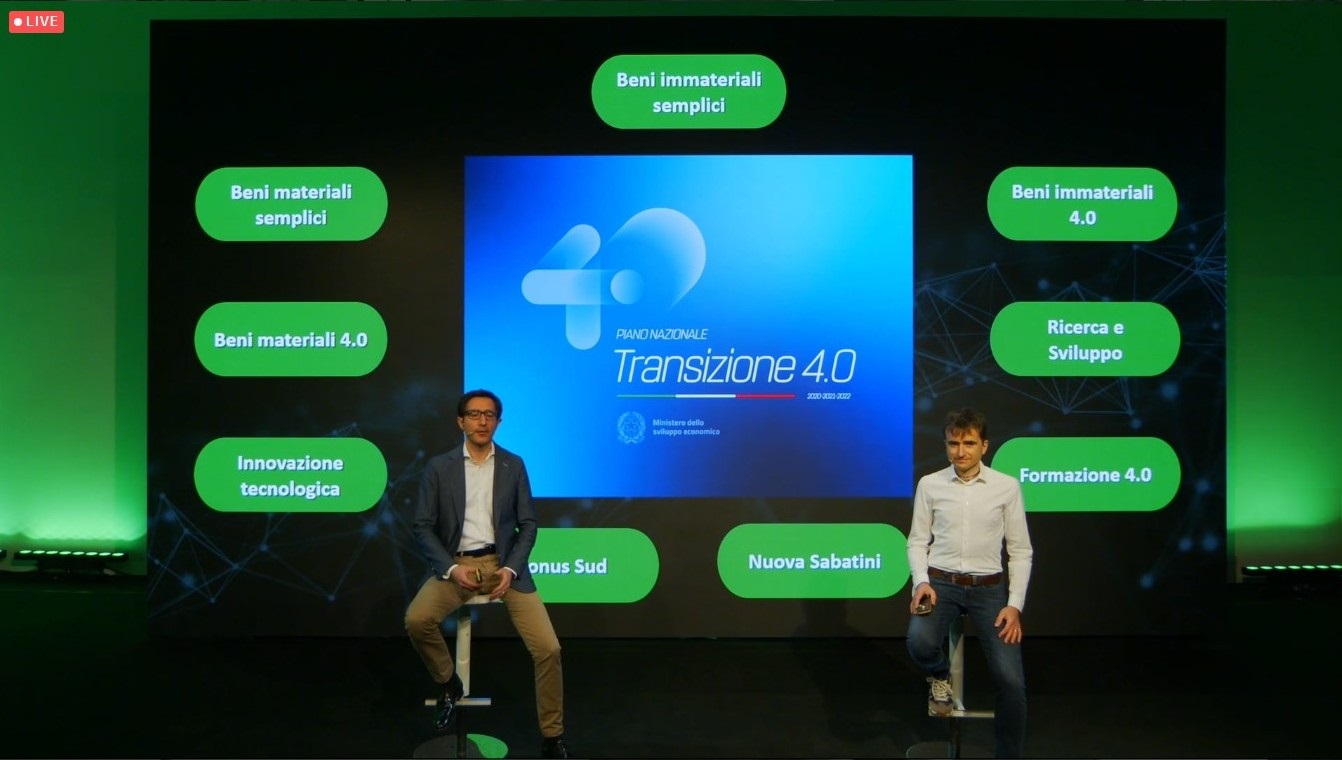
Gli incentivi fiscali non sono più validi soltanto per chi acquista macchine e impianti 4.0, ma anche per chi progetta e ne realizza digitali e sostenibili: un Innovation Talk in streaming di Schneider Electric ha spiegato come.
Tutte le aziende che hanno reddito d’impresa e in regola con l’erario (escluse le aziende pubbliche) possono accedere agli incentivi del Piano Transizione 4.0, l’evoluzione dell’originario Piano Industria 4.0 che nella primavera 2017 ha rilanciato la produzione industriale in Italia. Nella versione attuale gli incentivi fiscali non valgono soltanto per chi acquista macchine o impianti 4.0, ma anche chi progetta e ne realizza di digitali e sostenibili. Un costruttore di macchine può quindi beneficiarne in diversi modi, aumentando fino al 50% la competitività e rientrando velocemente dagli investimenti realizzati in R&S e attività d’innovazione tecnologica e sostenibile (come smaltimento, LCA e riciclo), logistica, produzione e manutenzione post-vendita. Schneider Electric ha riassunto la situazione in un Innovation Talk lo scorso 19 maggio 2021 in streaming dalla propria sede.
Dopo il saluto e l’introduzione di Marco Gamba che ha moderato gli interventi della giornata, Andrea Titi di Layton Italia (società che opera nella finanza agevolata per le imprese) ha ricostruito il percorso della politica industriale italiana, dall’iper-ammortamento ideato a fine 2016 per dare certezze alle aziende con misure pluriennali e aiutarle a rinnovare il parco tecnologico in ottica 4.0, all’estensione nel tempo sotto certe condizioni fino al 30 giugno 2023, riunendo in un unico piano le agevolazioni per le imprese.
Il Ministero per lo Sviluppo Economico ha in particolare definito 9 tecnologie abilitanti di riferimento: l’Advanced Manufacturing (come la robotica collaborativa), l’Additive Manufacturing (stampa 3D), la realtà aumentata e virtuale, la simulazione per ottimizzare i processi, l’integrazione bidirezionale orizzontale/verticale delle informazioni lungo la catena del valore, l’Internet industriale (la comunicazione multidirezionale tra processi produttivi e prodotti), le piattaforme in cloud (per gestire elevate quantità di dati su sistemi aperti e monitorare da remoto), la cyber-security industriale, i Big Data & Analytics (per ottimizzare ulteriormente i processi ed estrarre ancora più valore). Oltre alle agevolazioni per beni materiali semplici e per l’Industria 4.0, nonché per quelli immateriali semplici e per 4.0, si sono ora aggiunti la R&S e l’innovazione tecnologica, ma anche la Formazione 4.0 (poco utilizzato ma valido fino al 2022) e cumulabili con altri incentivi come Nuova Sabatini e Bonus Sud.
Per beni materiali e immateriali semplici si parla di credito d’imposta con diverse aliquote, ma il cardine sono gli investimenti dei beni materiali 4.0 altamente tecnologici (divisi in 3 categorie: quelli il cui funzionamento è controllato da sistemi computerizzati o gestito da opportuni sensori e azionamenti; sistemi per l’assicurazione di qualità e sostenibilità; dispositivi per l’interazione uomo-macchina e miglioramento di ergonomia e sicurezza nel posto di lavoro in ottica 4.0) oltre che dei beni immateriali 4.0 (ad esempio per sistemi MES intermedi tra gestionali ERP e sistemi Scada a contatto con le macchine; protezione dati; software per le cartelle cliniche).
Poi ci sono le agevolazioni della Nuova Sabatini per facilitare l’accesso al credito delle PMI (tanto apprezzato da segnare ad aprile 2021 un utilizzo del 92% delle risorse), per acquisire in leasing macchinari e attrezzature, beni strumentali e software. In più dal 2015 si facilita il credito d’imposta per R&S e dal 2020 anche l’innovazione tecnologica, ad esempio nella ricerca di personale, nella quota d’ammortamento per attrezzature di laboratorio, in consulenze esterne con università ed enti di ricerca, verso competenze tecniche e certificazione contabile (peraltro non più con approccio incrementale bensì volumetrico, dal 2020 in poi per ogni anno). Inoltre si è ampliato il perimetro oggetto dell’indagine: ai famosi 5 criteri del “Manuale di Frascati” (il documento sull’R&S nei Paesi dell’Ocse giunto alla sesta edizione nel 2002) si sono aggiunte 2 attività ad alto livello seppur a minor valor aggiunto (per aziende e non per settori di mercato), più il design e innovazione estetica (con aliquote differenziate).
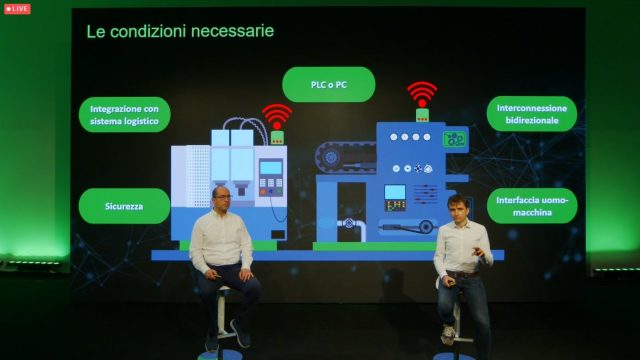
È toccato poi a Danilo Ponzio approfondire le soluzioni tecnologiche “incentivabili” (come si dice con brutto termine seppur efficace), con 5+2 condizioni: le 5 di base (PLC o PC, interconnessione bidirezionale, integrazione con sistema logistico della fabbrica, avere un HMI e soddisfare gli standard di sicurezza) e 2 fra le 3 ulteriori (teleassistenza, monitoraggio continuo, sistema cyber-fisico).
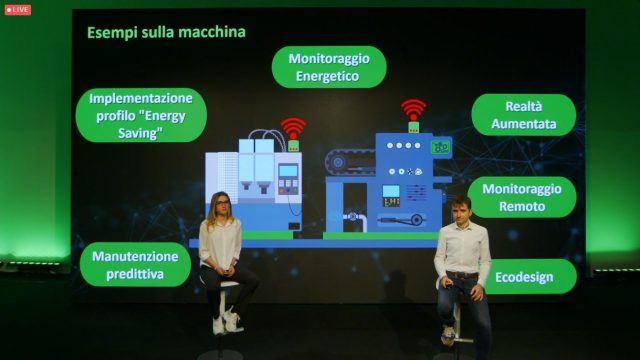
A seguire, Irina Prepelita ha spiegato gli incentivi alla sostenibilità, ormai uno dei fattori trainanti nelle strategie delle aziende, che riguarda anche l’ambito sociale ed economico, perché oltre a maggior efficienza può spingere a ridefinire il proprio modello di business e di gestione del personale (opportunamente rendicontato). Un OEM può allora ottimizzare la propria linea produttiva misurandone la sostenibilità, con un’analisi LCA che valuti l’impatto in tutto il ciclo di vita, per fotografare la situazione e stilare un programma di azioni migliorative (come il monitoraggio energetico, l’implementazione di un profilo “energy saving” con HMI lungo il percorso, algoritmi di manutenzione predittiva), per poi rifare l’analisi e avere risultati concreti e tangibili. Fra gli strumenti digitali, la realtà aumentata aiuta la gestione della manutenzione con interventi più rapidi, mentre il monitoraggio remoto con software di elaborazione dati in tempo reale controlla le variabili di efficienza e produttività. È utile anche il monitoraggio energetico del sito produttivo (per ottimizzarlo con il lean manufacturing che elimina gli sprechi e snellisce i processi), digitalizzare i collaudi (per innestare un circolo virtuoso di crescita della filiera) e guardare ai 17 obiettivi di sostenibilità definiti dall’ONU (per assicurare piena tracciabilità e visibilità ai materiali e la loro provenienza). Schneider Electric ha investito nel programma Green Premium (un passaporto ecosostenibile con tutti i dati lungo il ciclo di vita), oltre a supportare i clienti come Trusted Advisor (proponendo soluzioni digitali sostenibili) e attuando analisi LCA che rientrano nelle norme UNI EN ISO 14040 e 14044 (con certificazioni ad esempio del sistema internazionale EPD che danno un vantaggio competitivo in più). Tutti questi incentivi possono portare a risparmi del 15% per l’innovazione green e digitale, che diventano il 20% per la R&S e 50% per la Formazione 4.0.
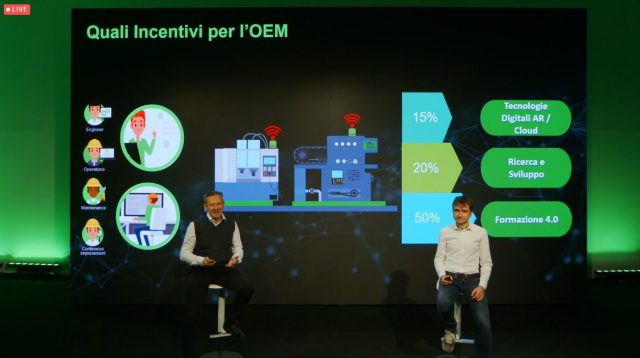
A questo punto Andrea Ariano si è concentrato sull’innovazione tecnologica per la digitalizzazione, un traguardo essenziale per la sostenibilità ma anche per fornire soluzioni flessibili che oggi diventa un’esigenza sempre più stringente, oltre che per rendere più efficienti i processi e i rapporti tra OEM e utilizzatori finali, dalla progettazione alla messa in servizio fino alle applicazioni, coinvolgendo a 360 gradi tutti gli operatori. Dopo l’impulso degli incentivi, in Italia il 34% delle aziende è già digitalizzato e l’11% sta applicando la digital transformation: ma resta un 55% di imprese che ancora devono sfruttare l’opportunità epocale. Dalle tecnologie più di base come cloud, teleassistenza e realtà aumentata ci si può evolvere a soluzioni più complesse per macchine più evolute come AI, ML, digital twin, sensori IoT, automazione, analisi dati, stampa 3D. Con una control room si può monitorare 24 ore per 7 giorni la flotta del parco installato, basandosi sul database storico del PLC accessibile in tempo reale per intervenire tempestivamente.
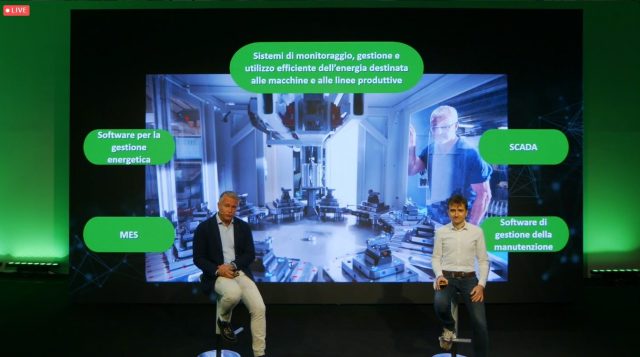
A conclusione della mattinata, l’esperto Giovanni Malaguti ha infine fatto il punto sugli incentivi per l’ammodernamento e la riqualifica degli impianti produttivi per renderli più efficienti e sostenibili: una gestione software e un utilizzo più efficiente dell’energia destinata in particolare a macchine e linee produttive, senza dimenticare il MES, tutti i sistemi Scada e di monitoraggio per la produzione e soprattutto la manutenzione. In realtà nei nostri quadri elettrici le possibilità di misurare e la logica distribuita possono già intervenire in automatico senza essere presidiati, quindi basta connetterli al sistema informativo di fabbrica e il più è fatto.
a cura di Loris Cantarelli
Condividi l'articolo
Scegli su quale Social Network vuoi condividere