Affrontiamo il tema del Lean Management applicato alle produzioni su commessa che caratterizzano molte delle aziende del settore della meccanica
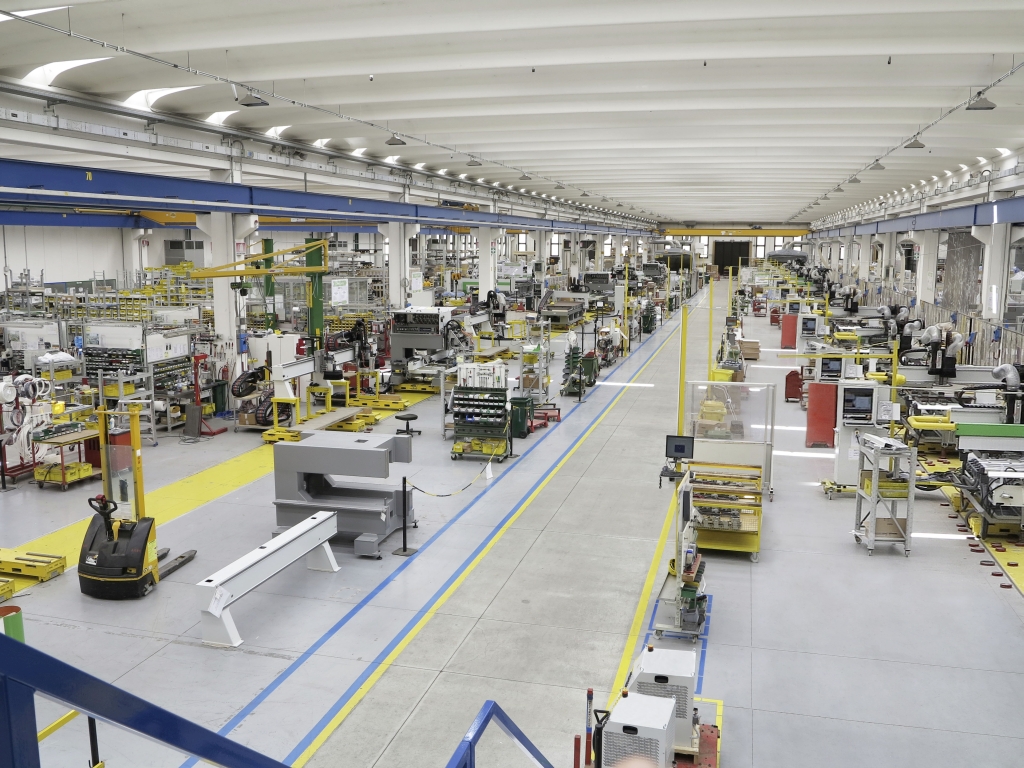
Affrontiamo il tema del Lean Management applicato alle produzioni su commessa che caratterizzano molte delle aziende del settore della meccanica
La filosofia Lean è oggi molto di moda. Non esiste o quasi azienda che non dica di applicare il Lean. Dubito che ciò sia vero in senso pieno. Ma, al di là di questo, va subito chiarito che, seppure la filosofia Lean consista di una serie di principi manageriali che si applicano allo stesso modo, indipendentemente dal settore industriale e dalla collocazione geografica, è pur vero che essa, negli aspetti operativi, va adattata ai contesti specifici. Produrre automobili non è la stessa cosa che produrre macchine utensili, o linee di imbottigliamento, o altri prodotti realizzati e personalizzati su richiesta del cliente. Muoversi nel contesto degli alti volumi e della ripetitività non è la stessa cosa che muoversi nel contesto dei bassi volumi e dell’alta varietà, nonché della forte personalizzazione per il cliente.
Cosa vuol dire allora cogliere il potenziale del Lean Thinking nella produzione su commessa, anzi, per essere più precisi, dell’Engineering to Order?
Il grafico illustra un processo di evasione ordine, ed evidenzia il contributo dell’applicazione della logica Lean alle varie fasi.
Commerciale
Vanno comprese a fondo le richieste del cliente forzando il “front loading”. Non si deve partire in fretta accettando che certe informazioni all’inizio siano ignote, e lasciando a dopo la soluzione di certe ambiguità. Dopo è troppo tardi e costoso. Bisogna insistere perché il cliente, tramite la sua interfaccia (il commerciale) fornisca tutte le informazioni che può ragionevolmente fornire. Vanno definite delle informazioni di minima, senza le quali il processo non può partire, tramite semplici strumenti quali le check list. Si possono inserire dei veri e propri “Quality Gate”, cioè dei punti di controllo sufficientemente rigorosi atti a verificare il livello di definizione dell’ordine prima della partenza operativa. A questo punto ci vuole disciplina: evitare di partire se mancano le informazioni di minima, invece che “buttare il cuore al di là dell’ostacolo”.
Nell’ufficio commerciale si dovrebbero inserire riunioni giornaliere, analoghe a quelle che si usano da tempo in produzione, con lo scopo di verificare lo stato di definizione del progetto. La visualizzazione delle informazioni necessarie all’avvio del progetto, con responsabilità e scadenze, cartellini rossi o quant’altro serva ad evidenziare le urgenze, è un sistema per tenere sotto controllo le prime fasi della commessa, che contrariamene a quanto molti pensano, sono decisive per il successo, soprattutto in termini di margini, del progetto.
Progettazione
La progettazione deve cambiare approccio. Non si tratta di progettare il prodotto “perfetto”, in cui ogni parte ha un elevato livello di specializzazione e personalizzazione. Il lean nasce in progettazione, con il “design to lean”: bisogna personalizzare (certamente, è un nostro punto di forza) ma senza appesantire inutilmente il sistema. L’ufficio progettazione deve perseguire logiche di modularizzazione e di standardizzazione, che alleggeriscano il sistema logistico-produttivo.
Pianificazione
Bisogna individuare il punto di disaccoppiamento per semplificare la pianificazione e ridurre i tempi di consegna. Quando il prodotto diventa veramente unico e personalizzato? Dalla prima fase, o dopo? Posso individuare delle “macchine base”, dei gruppi, dei componenti, che sono presenti in tutti i prodotti consegnati al cliente (fermo restando che, come detto sopra, la progettazione può portare un forte contributo)? Questo vuol dire disegnare un flusso produttivo, in cui solo ciò che è veramente personalizzato viene gestito “a fabbisogno”, il resto può essere gestito con sistemi più semplici (punti di disaccoppiamento, supermercati, ecc.)
Produzione e Logistica
Produzione e Logistica devono passare attraverso processi di miglioramento che seguano la classica sequenza lean “stabilizzazione – flusso – ritmo – pull”, pur con i dovuti accomodamenti.
Stabilizzazione
La stabilizzazione del processo, che dà la possibilità di avere chiare aspettative nei confronti dell’output del processo produttivo e di non farci scoprire solo a fine periodo che cosa si è prodotto, può essere migliorata tramite la creazione di postazioni di lavoro che applichino i principi delle 5S, e tramite la standardizzazione di operazioni, attrezzature e impianti usati per il montaggio. Non è mai vero che si tratti di operazioni artigianali, non standardizzabili in qualche misura. E’ vero il contrario: che la non abitudine a standardizzare porta all’arte di arrangiarsi.
Flusso
Si devono creare le condizioni per cui un processo di montaggio fluisca senza interruzioni, garantendo le risorse necessarie al momento opportuno. Considerare adeguato lo spostamento delle risorse dal montaggio di una macchina ad un altro è sintomatico di un orientamento alla saturazione delle risorse. Per il Lean questo non basta: bisogna garantire il fluire delle operazioni di montaggio, riducendo al minimo il materiale in fabbrica e il numero di macchine contemporaneamente al montaggio. L’implementazione di un nuovo layout in linea (quando possibile) forza questo approccio.
Ritmo
Bisogna dare cadenza alla fabbrica, producendo secondo il takt time. Si può definire una sequenza di montaggio standardizzata, pensata apposta per rispettare un certo takt time. Si dovrebbero definire standard diversi per diversi takt time, in modo da essere pronti a modificare l’organizzazione quando si prevede un aumento o una diminuzione della domanda.
Pull
A parte per minuterie e parti ripetitive, è difficile realizzare un vero sistema pull basato su kanban e supermercati per la produzione su commessa. L’obiettivo deve allora essere la sincronizzazione, per garantire il flusso del montaggio e la minore occupazione possibile degli spazi (ed anche il miglior flusso di cassa possibile). Un modo per sincronizzare la logistica con le fasi di montaggio è la “supply chain action board”, dove l’arrivo del materiale viene organizzato sulla base delle fasi di montaggio previste nel periodo successivo (il giorno o la settimana).
Anche il ricorso al kitting da parte dei fornitori può dare ottimi risultati, in quanto consente di sincronizzare l’arrivo dei materiali e di semplificare la logistica interna. Riducendo il numero di fornitori e instaurando un rapporto win-win di partnership con essi, ci si può far recapitare il materiale già organizzato per fasi di montaggio. La logistica deve solo immagazzinare il kit e recapitarlo al montaggio quando la scheda del supply chain action board glielo chiede. In un caso aziendale l’introduzione di questo sistema ha ridotto i fornitori da 32 a 12 e gli item gestiti da 172 a 35 (i microkit).
Un aspetto determinante per il funzionamento del sistema è la frequenza di controllo: la disponibilità dei materiali viene verificata “sul campo” con alta frequenza, e in maniera anticipata (controllo oggi che ci sia quello che serve nel periodo successivo, non in quello corrente, perché sarebbe troppo tardi).
a cura di Giancarlo Oriani
Condividi l'articolo
Scegli su quale Social Network vuoi condividere