Nell’ambito della fabbricazione additiva, i Processi a Deposizione Diretta (DED) differiscono da quelli a Letto di Polveri (PBF) sotto molteplici aspetti. I più evidenti…
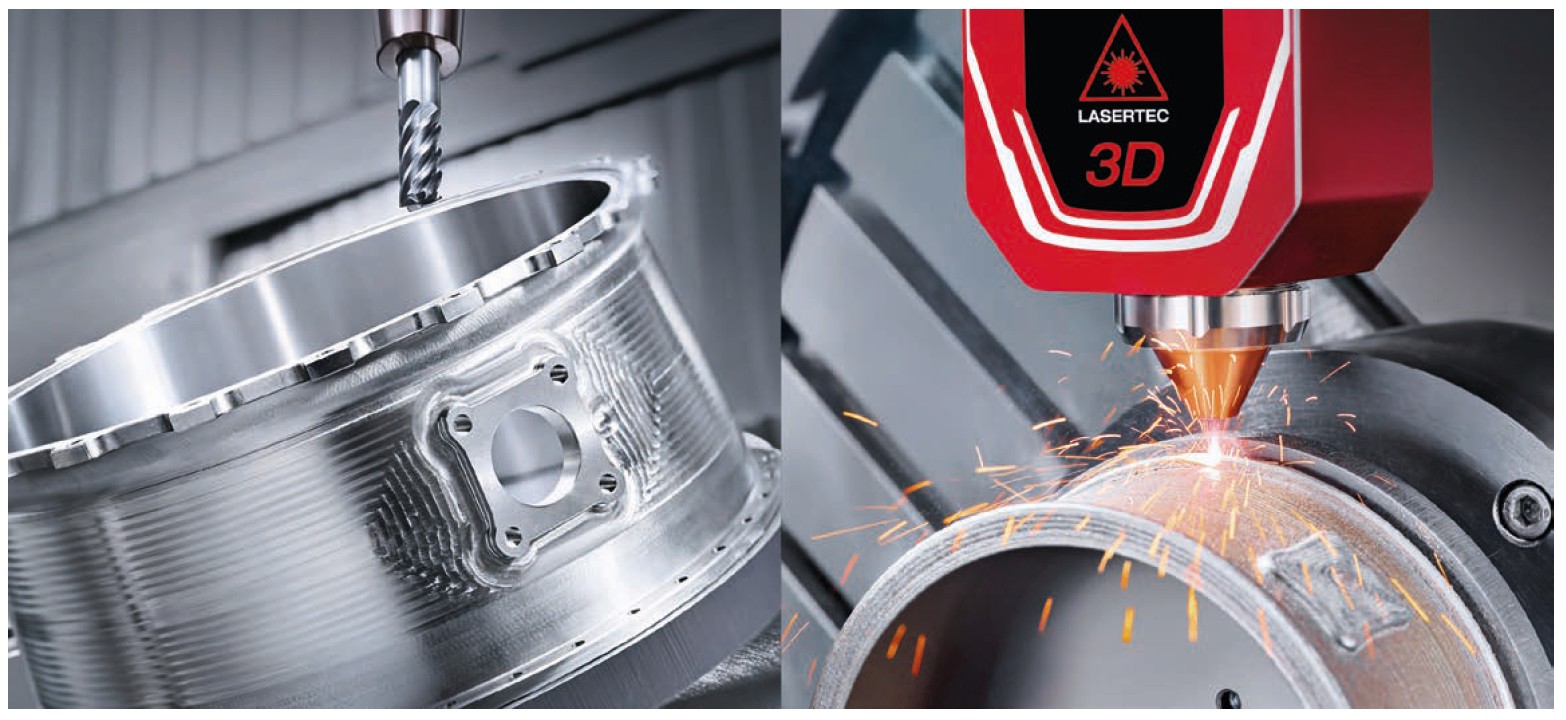
Nell’ambito della fabbricazione additiva, i Processi a Deposizione Diretta (DED) differiscono da quelli a Letto di Polveri (PBF) sotto molteplici aspetti. I più evidenti riguardano le prestazioni in termini di produttività e qualità superficiale del componente prodotto
di Alessandro Salmi *
* Professore Associato in Tecnologie e Sistemi di lavorazione, Digep (Dipartimento di Ingegneria Gestionale e della Produzione) del Politecnico di Torino
I processi di deposizione diretta o DED (Directed Energy Deposition) sono una classe di tecnologie di FA (Fabbricazione Additiva) per componenti metallici che sta suscitando un crescente interesse nel mondo scientifico e industriale, poiché permettono di rimuovere alcune limitazioni tipiche delle tecniche additive attualmente consolidate. La principale differenza riscontrabile rispetto ai processi a letto di polvere o PBF (Powder Bed Fusion) risiede nella modalità con cui il materiale viene deposto. Nei processi PBF la polvere metallica è stesa sulla piattaforma di costruzione in modo da formare uno strato omogeneo, che verrà successivamente fuso selettivamente. I processi DED, al contrario, depositano il materiale metallico soltanto dove necessario tramite l’uso di uno specifico ugello montato su un sistema di movimentazione oppure su di un braccio robotico; il materiale depositato sarà simultaneamente fuso grazie all’uso di una sorgente di energia, come nella figura in basso: il materiale di base può essere sotto forma di (a) filo o (b) polvere.
Diverse applicazioni
Analogamente alle altre tecnologie di FA, i componenti sono costruiti strato per strato. I sistemi DED a due o tre assi hanno una piastra di costruzione fissa, quindi è l’ugello a spostarsi verso l’alto dopo la deposizione di ogni singolo strato. Esistono anche sistemi DED a 4-5 assi, che muovono in contemporanea l’ugello e la piastra di costruzione indipendentemente l’uno dall’altro, consentendo di costruire geometrie di forma più complessa. Un’interessante peculiarità dei processi DED è la possibilità di costruire una geometria partendo da una superficie non planare. Ne consegue che i processi DED sono estremamente convenienti per applicazioni in cui si vuole aggiungere a parti esistenti nuovo materiale, eventualmente diverso rispetto al materiale base, o per la riparazione di componenti, essendo possibile depositare nuovo materiale sulle parti danneggiate. Applicazioni tipiche dei processi DED sono proprio la riparazione di componenti danneggiati delle turbine e/o l’aggiunta di geometrie, anche complesse, su componenti di grandi dimensioni. Oltre alle applicazioni MRO (Maintenance, Repair and Operations) i processi DED permettono anche la costruzione ex novo di componenti. Nella maggior parte dei casi, i componenti prodotti hanno una forma quasi finale (near net shape) e in genere richiedono soltanto alcune lavorazioni di finitura in accordo con le tolleranze richieste.
Polvere o filo
Il materiale di partenza è in genere un metallo, che viene depositato nella zona da costruire e simultaneamente fuso mediante una sorgente di energia, tipicamente un fascio laser o un fascio di elettroni. I sistemi DED basati su fascio laser utilizzano il materiale sottoforma di polvere o filo e, tipicamente, richiedono una camera completamente inerte se si lavora con metalli reattivi oppure, nell’ottica di una riduzione dei costi, una copertura locale con gas di protezione nel caso di metalli non reattivi (utilizzando un approccio simile a quello utilizzato in saldatura). I sistemi DED alimentati a polvere richiedono inoltre un flusso di gas inerte di trasporto (argon o elio) per assistere e controllare il flusso di polvere attraverso l’ugello. Per i sistemi DED a filo, l’alimentazione è assicurata da una bobina e il filo viene spinto verso l’ugello tramite un sistema meccanico di trasporto. I sistemi DED basati su fascio di elettroni utilizzano unicamente un’alimentazione a filo metallico e il processo deve essere eseguito nel vuoto. I tassi di deposizione per i processi DED sono significativamente più alti rispetto a quelli dei processi PBF. I sistemi DED ba sati su laser e polveri metalliche possono raggiungere un tasso di deposizione fino a 3 kg/h, laddove i sistemi PBF tipicamente si assestano su 0,2 kg/h. Ancora più produttivi sono i sistemi DED a fascio elettronico, che possono raggiungere valori di deposizione fino a 9 kg/h. Di conseguenza, i sistemi DED tendono ad avere volumi di costruzione molto più ampi rispetto ai sistemi PBF, poiché gli alti tassi di deposizione si prestano alla produzione di componenti decisamente più grandi, fino a circa 0,5 m3 o più. Tuttavia, si deve considerare che la minore produttività dei sistemi PBF è correlata al minore spessore dello strato utilizzato per costruire i componenti. Pertanto, l’elevata precisione e il dettaglio ottenibili con i processi PBF sono fuori dalla portata dei processi DED, che sono quindi adatti a componenti sicuramente più voluminosi ma meno dettagliati. In analogia con i processi PBF, durante la costruzione si ha la generazione di tensioni residue causate dal rapido riscaldamento e raffreddamento della zona di fusione. Le strategie di scansione, ovvero la modalità utilizzata per depositare e fondere il materiale, possono essere ottimizzate per aiutare a ridurre questi tensionamenti, tuttavia nella maggior parte dei casi sarà necessario, al termine della costruzione, un trattamento termico di distensione per poi eseguire ogni ulteriore processo di finitura.
È inoltre interessante segnalare che sono presenti sul mercato dei sistemi ibridi di fabbricazione (come nell’immagine in alto di fresatura a 5 assi), che combinano in un unico sistema i processi DED e le tecnologie CNC di asportazione di truciolo. Questi sistemi, estremamente flessibili, sono in grado di costruire componenti in modalità additiva utilizzando un ugello laser alimentato a polvere, ed eseguire simultaneamente i processi di finitura per asportazione di truciolo. Si può quindi costruire e ottenere le tolleranze richieste, il tutto in un’unica macchina e in modalità completamente autonoma.
In breve
In conclusione, è possibile identificare per i processi DED i seguenti vantaggi:
– non richiedono una superficie piana di partenza, quindi sono adatti alla riparazione e alla costruzione su componenti esistenti nonché per la costruzione di parti completamente nuove;
– è una tecnologia di FA relativamente veloce rispetto alle tecnologie PBF;
– i sistemi ibridi possono combinare sia la lavorazione additiva che quella sottrattiva in un’unica macchina, rendendo possibile la fabbricazione e la successiva finitura in unico ambiente completamente automatizzato.
Tuttavia, è necessario mettere in luce che sono presenti anche alcuni svantaggi:
– per i materiali reattivi è richiesta una camera (in genere di grandi dimensioni) completamente inerte; ciò comporta l’utilizzo di elevati volumi di gas inerti e la necessità di attendere tempi relativamente lunghi per raggiungere i livelli di ossigeno richiesti;
– la forma prodotta è caratterizzata da tolleranze e finitura superficiali spesso non compatibili con l’applicazione finale e quindi necessita di una fase di post-processamento per raggiungere le finiture richieste;
– non tutta la polvere spruzzata dall’ugello viene fusa tuttavia, a differenza delle tecnologie PBF, generalmente è poco conveniente recuperare tale polvere; pertanto è necessario smaltirla come rifiuto dopo la costruzione, riducendo l’efficienza complessiva del processo.
a cura di Loris Cantarelli
Condividi l'articolo
Scegli su quale Social Network vuoi condividere