Confrontiamo dal punto di vista economico la fabbrica additiva laser di componenti metallici complessi con pressofusione e lavorazioni per asportazione.
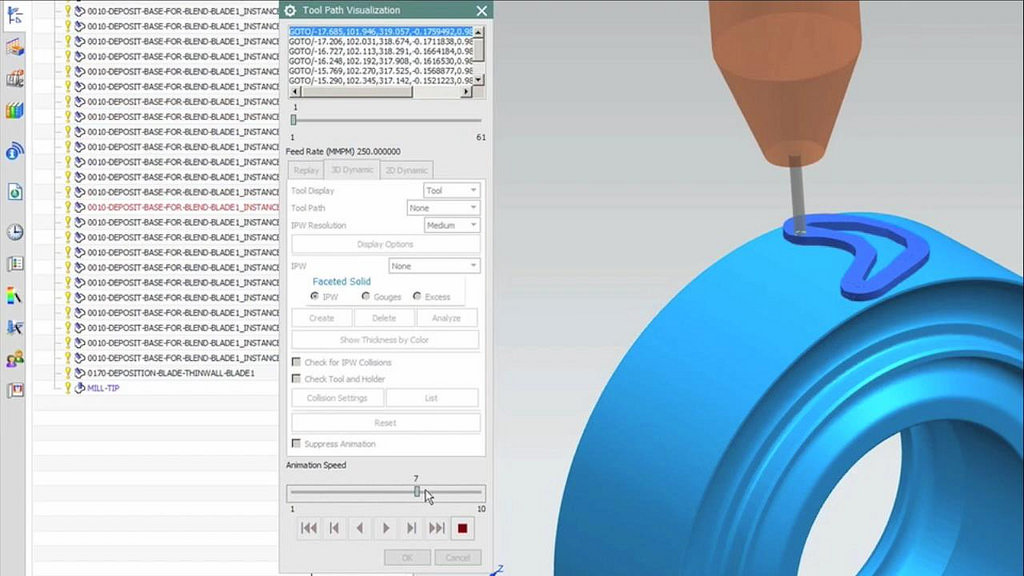
Confrontiamo dal punto di vista economico la fabbrica additiva laser di componenti metallici complessi con pressofusione e lavorazioni per asportazione.
di Alessandro Salmi
I più recenti sviluppi delle tecnologie di Fabbricazione Additiva (FA) per la produzione di componenti metallici permettono sempre più il loro impiego da parte delle industrie ad alto livello tecnologico. la libertà geometrica, peculiarità della FA, consente infatti di produrre componenti ottimizzati per la loro funzionalità, trascurando le limitazioni imposte dai processi di fabbricazione convenzionali. In questo articolo si pone l’attenzione sui costi. La fabbricazione additiva laser (SLM) viene considerata come alternativa alla pressofusione (HPDC) o alle lavorazioni per asportazione di truciolo (CNC) nella produzione di componenti ad elevata complessità e con elevate richieste dal punto di vista delle proprietà meccaniche. Occorre tuttavia un confronto tra le diverse tecnologie produttive in termini economici.
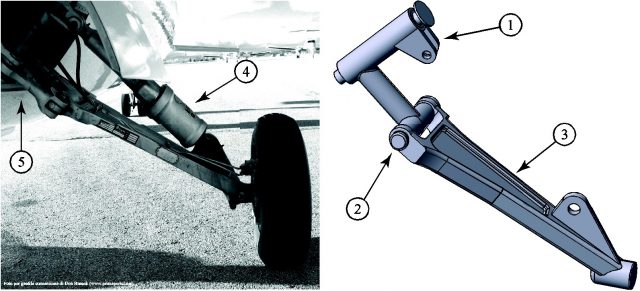
Tale confronto è stato effettuato dal gruppo di tecnologie avanzate (AMTech) del Politecnico di Torino, considerando un componente aeronautico che presenta forme complesse ed è caratterizzato da importanti prestazioni meccaniche: un modello in scala 1:5 di un carrello di atterraggio principale del velivolo italiano P180 Avant II di Piaggio Aero Industries S.p.A. Gli elementi di base del carrello principale sono mostrati in Fig. 1. Nel dettaglio, il carrello di atterraggio si compone di cinque parti, tuttavia sono stati presi in considerazione solamente il supporto principale e il braccetto. Per ridurre il peso pur garantendo elevate proprietà di resistenza, la struttura è realizzata in una lega alluminio: in particolare si è considerata la lega AlSi10Mg.
Le voci di costo prese in esame
Si premette che, poiché si tratta di una valutazione comparativa tra più processi tecnologici, l’analisi è effettuata concentrandosi sulla sola variazione dei costi direttamente connessi alle diverse tecnologie. In particolare le voci di costo prese in considerazione sono: il costo del materiale, i costi di trasformazione e il costo dell’attrezzatura. Nello specifico, i costi di trasformazione includono l’ammortamento del sistema produttivo, la (ri)progettazione del componente, le operazioni preparatorie e di finitura e il collaudo. Mentre i costi amministrativi, dell’energia, dell’area occupata dai sistemi produttivi, dalle apparecchiature ausiliarie e delle operazioni di montaggio non sono stati presi in considerazione poiché approssimativamente analoghi tra i diversi processi tecnologici. Inoltre, poiché il costo del lavoro è fortemente influenzato dalla localizzazione dello stabilimento di produzione, in questo studio si è presunto che l’impianto di produzione si trovi in Europa occidentale.
Le modalità tradizionali
Nel caso della pressocolata (HPDC), la valutazione del costo del carrello principale sinistro si basa su un preventivo fornito da un produttore locale di stampi. La stima dei costi tiene conto della geometria del pezzo e dell’indicazione di un basso volume di produzione (stampo a doppia impronta). Si è sfruttata la possibilità di produrre nello stesso stampo sia il supporto principale che il braccetto. Lo stampo è caratterizzato anche da elementi mobili per poter risolvere i sottosquadri.
Relativamente alla lavorazione per asportazione di truciolo si è considerato un centro di lavoro a 5 assi. Per valutare il costo del supporto principale e del braccetto sono state considerate le operazioni di sgrossatura, semifinitura e finitura. Il grezzo di partenza è un blocco parallelepipedo di alluminio e l’operazione di sgrossatura viene eseguita utilizzando una fresa dal diametro di 10 mm. A questa segue l’operazione di semifinitura utilizzando una fresa semisferica dal diametro di 6 mm con una strategia di taglio a piani paralleli. Infine, la finitura è realizzata con la stessa tipologia di fresa ma con una strategia di contornitura a 5 assi.
L’opzione della fabbricazione additiva
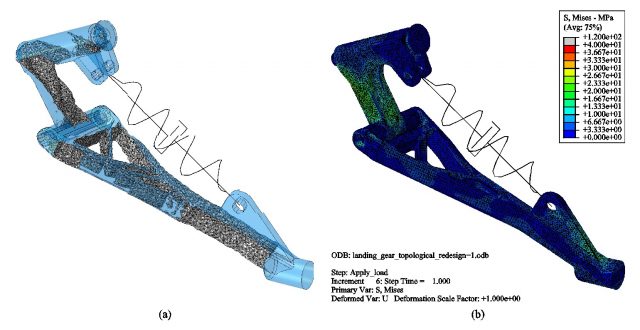
Per quanto riguarda la fabbricazione additiva si è previsto di fabbricare il carrello utilizzando un sistema EOSINT M270 a fusione selettiva laser (SLM) di polvere prodotto da EOS. In tal caso si è dapprima proceduto con la rimozione dal design del componente di un certo numero di limitazioni associate alle tecnologie di produzione tradizionali. Pertanto il carrello è stato riprogettato e adattato per la FA secondo le linee guida della progettazione per la FA, preservandone la funzionalità. Inoltre, il componente è stato alleggerito mediante l’uso dell’ottimizzazione topologica e di forma eseguita mediante il software TOSCA all’interno dell’ambiente SIMULIA Abaqus (Fig. 2a). Tuttavia, non essendo il modulo di ottimizzazione topologica specifico per la produzione additiva, è stato necessario modificare la geometria fornita dal software per rispettare le regole di progettazione per la FA. In particolare, la geometria è stata rimodellata per ridurre al minimo la necessità di supporti interni alla struttura, che risulterebbero di difficile rimozione a seguito del processo di fabbricazione. Infine, il carrello riprogettato è stato verificato staticamente in ambiente FEM (Fig. 2b). Per riempire quanto più possibile il volume di costruzione, il supporto principale ed il braccetto sono stati opportunamente orientati rispetto alla direzione di costruzione e disposti a 5 mm di distanza gli uni dagli altri: in tal modo è possibile costruire quattro strutture complete per ogni job.
Tre tecnologie a confronto
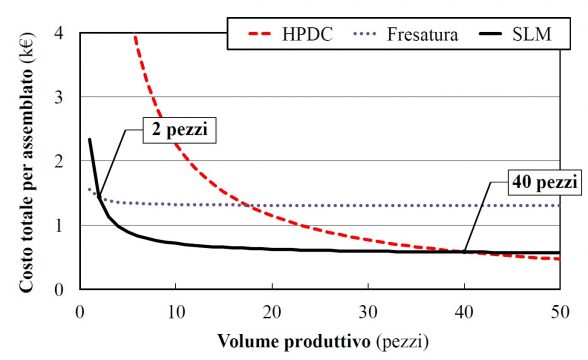
Come si vede con chiarezza, la Fig. 3 illustra l’analisi del punto di pareggio per le tre tecnologie selezionate. Il punto di pareggio tra SLM e HPDC è di circa 40 strutture complete. La lavorazione a 5 assi risulta conveniente solo per la produzione di un paio di assemblati. Se si considera che per l’intero modello di aeromobile è necessario produrre sia una struttura destra che una sinistra, i costi raddoppiano nel caso di pressocolata, mentre si mantiene pressoché inalterato il costo dell’assemblato nel caso della FA. Inoltre è bene tenere in considerazione anche un altro aspetto: il tempo di produzione. Con la FA è possibile produrre due coppie di assemblati in circa 2,5 giorni mentre il tempo per produrre gli stampi per pressocolata e per iniziare la produzione è dell’ordine di alcune settimane.
I risultati di questo studio dimostrano come la FA, abbinata a una (ri)progettazione per la FA, è una valida alternativa per lotti di piccole e medie dimensioni anche nel caso di componenti metallici finali. Non appena le tecnologie additive si diffonderanno ulteriormente e diventeranno processi produttivi consolidati, sarà logico supporre una diminuzione del costo orario dei sistemi di FA e di conseguenza, nel prossimo futuro, il punto di pareggio si sposterà verso volumi produttivi maggiori di quelli indicati in questo studio.
Alessandro Salmi è Ricercatore confermato e Professore Aggregato presso il DIGEP (Dip. Di ingegneria Gestionale e della Produzione) del Politecnico di Torino
a cura di Redazione
Condividi l'articolo
Scegli su quale Social Network vuoi condividere