L’integrazione di KeMotion in RoboDK semplifica il ciclo di vita di una soluzione di processo con robotica integrata, fino al post-vendita.
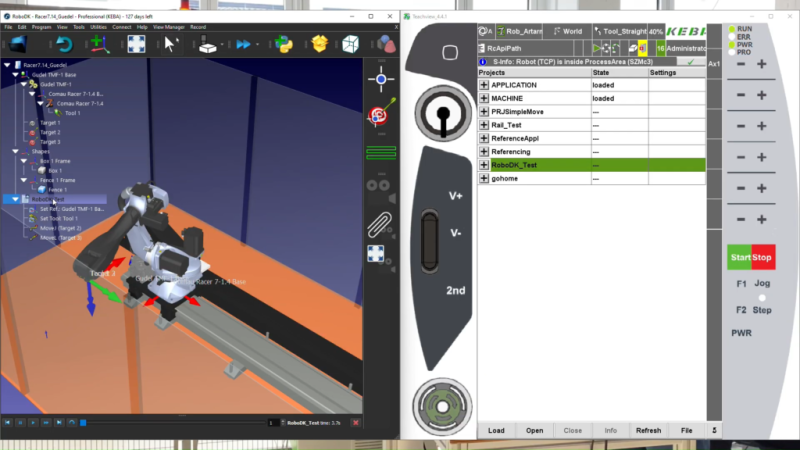
RoboDK e Keba hanno annunciato una collaborazione: l’azienda canadese ha sviluppato un driver KeMotion che si basa sulle nuove API (Application Programming Interfaces) web sicure e potenti dell’azienda di robotica industriale, consentendo flussi di lavoro appropriati. Anche i clienti Keba ne traggono vantaggio, avendo già a disposizione la RoboDK Robot Library.
I vantaggi di due piattaforme open
Gli sviluppatori OEM possono ora combinare i vantaggi della piattaforma di automazione Kemro X e di RoboDK. Le due piattaforme open consentono di creare e testare dal desktop diversi scenari di celle robotizzate e di impostare solo successivamente la cella di produzione reale. In questo modo è possibile determinare il posizionamento ottimale del robot prima del suo effettivo utilizzo. I tempi ciclo sono ridotti al minimo, si evitano le singolarità e si garantisce l’accessibilità. Questo porta a tempi di messa in servizio più brevi, a risparmiare risorse umane e preparare rapidamente un accurato preventivo per il cliente.
Trasferimento semplice all’unità di controllo Keba
La funzionalità attualmente disponibile consente di creare programmi robotici nel linguaggio Kairo di Keba nell’ambiente RoboDK sulla base di modelli 3D di parti e sistemi. È disponibile anche una semplice opzione per il trasferimento ai controller Keba. L’esecuzione del movimento del robot può essere monitorata sia in ambiente digitale sia con il controller del robot stesso all’interno di RoboDK.
Funzionalità avanzate di simulazione e programmazione
La connessione fra Kemro X e RoboDK offre agli utenti Keba funzionalità avanzate di simulazione e programmazione, tra cui funzioni CAD-to-path, OLP (Off-Line Programming), funzioni di digital twin, controllo delle collisioni, CAM per robot e altro ancora.
Manutenzione semplice dal digital twin
Anche dopo che la cella di produzione è stata impostata e messa in funzione, si può facilmente mantenere o modificare con il digital twin. I dati registrati permettono di identificare rapidamente i problemi e fornire un efficiente supporto e assistenza ai clienti. Ciò riduce al minimo i tempi di inattività in caso di modifiche al prodotto e garantisce un servizio e un’assistenza efficienti grazie alla rapida identificazione dei problemi.
a cura di Redazione
Condividi l'articolo
Scegli su quale Social Network vuoi condividere