Le tecnologie additive non sono una soluzione produttiva a sé stante, ma un processo complementare e sinergico alle tecnologie sottrattive per produzione di un pezzo.
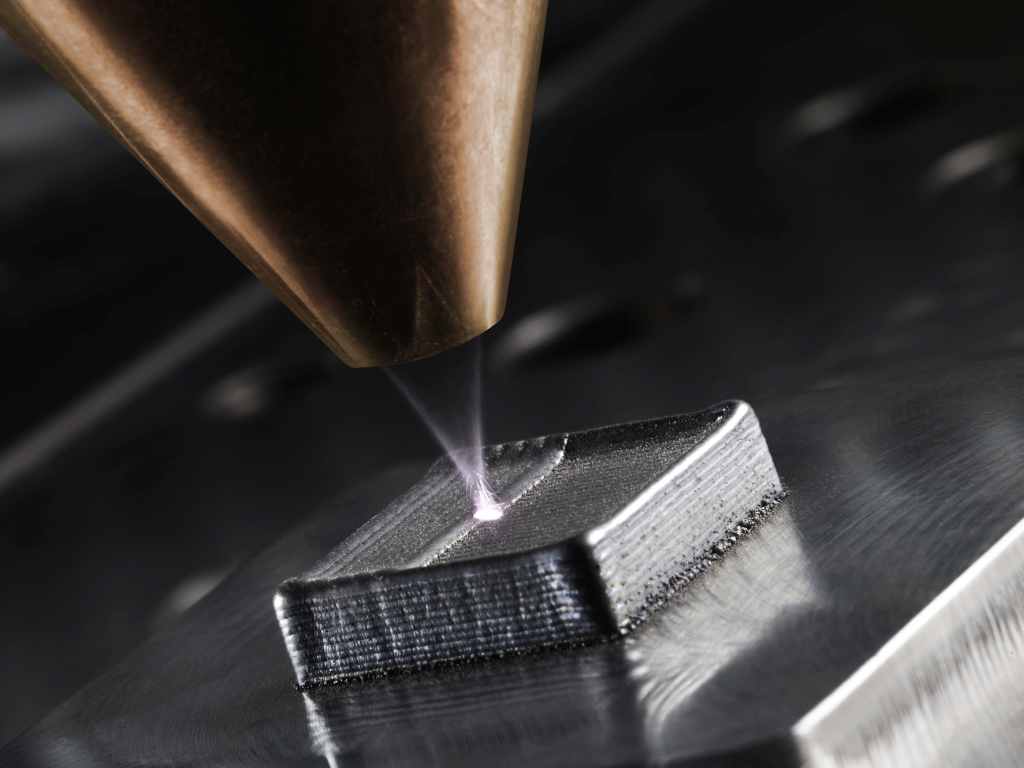
Le tecnologie additive non sono una soluzione produttiva a sé stante, ma un processo complementare e sinergico alle tecnologie sottrattive per produzione di un pezzo.
Negli ultimi anni, la produzione di componenti in materiale metallico è stata rivoluzionata dallo sviluppo delle tecnologie additive. Tali tecnologie innovative, che rendono possibile la fabbricazione di un oggetto strato dopo strato, hanno oggi raggiunto un certo grado di maturità e sono, per loro stessa natura, contrapposte alle tecnologie tradizionali per asportazione di materiale. Le tecnologie di fabbricazione additiva consentono la produzione di componenti a partire da polveri metalliche senza l’utilizzo di utensili ed attrezzature. Si possono dunque produrre pezzi di geometria complessa, la cui progettazione può focalizzarsi sulla funzionalità del componente.
Tuttavia la produzione di componenti di qualità in materiale metallico mediante le tecnologie additive richiede un certo numero di operazioni di finitura. La fabbricazione per strati deve essere intesa come uno dei molti processi che possono essere utilizzati per produrre un pezzo, non come una soluzione a sé stante. I processi additivi più utilizzati per la fabbricazione di componenti in metallo sono la fusione su letto di polvere (Powder Bed Fusion) e il laser cladding (Direct Energy Deposition secondo la nomenclatura definita dallo standard americano ASTM F42).
Considerate le tolleranze dimensionali e le rugosità superficiali che, allo stato attuale, tali processi sono in grado di garantire (Figura 1), la fabbricazione per strati va valutata in analogia alle tecniche di fusione o di stampaggio per la produzione di semilavorati. Per migliorare la qualità superficiale dei componenti, si rende necessaria la finitura degli stessi mediante i processi sottrattivi convenzionali, che consentono di rispettare i requisiti dimensionali, estetici e tribologici. È dunque necessaria un’attenta progettazione e pianificazione dell’intero ciclo produttivo del pezzo, che richiede molteplici competenze per considerare le implicazioni dei processi sottrattivi sul processo additivo, sia a disegno che nelle fasi di definizione del ciclo di lavoro. L’approccio progettuale e le azioni coinvolte nel processo iterativo di pianificazione e preparazione della produzione saranno leggermente diverse a seconda del materiale impiegato (acciaio, alluminio o titanio).
In generale, nel ciclo produttivo, si possono identificare le seguenti fasi (Figura 2):
- Preparazione del modello 3D: la geometria CAD del componente finale va trasformata in un modello per la produzione. Tale trasformazione comporta l’aggiunta di sovrametallo sulle superfici che dovranno essere finite e l’aggiunta di riferimenti per le successive operazioni di elettroerosione e fresatura. Occorre inoltre tenere conto del ritiro che il materiale può subire durante la produzione per strati, a seguito dei passaggi di fase e dei gradienti termici.
- Fabbricazione per strati: il modello 3D modificato nella fase precedente va orientato nel volume di lavoro del sistema additivo. In funzione dell’orientamento devono essere aggiunte le strutture di supporto per le superfici aggettanti e non sostenute dal materiale degli strati sottostanti. Occorre inoltre definire i parametri di processo specifici per il materiale metallico impiegato. Si fabbricano infine i pezzi per deposizione e fusione di strati successivi di materiale sulla piattaforma di costruzione.
- Trattamento termico di distensione: viene realizzato prima di rimuovere i pezzi dalla piattaforma al fine di ridurre le tensioni residue ed evitare che i pezzi si deformino durante l’azione di taglio.
- Elettroerosione a filo: è la lavorazione comunemente impiegata per la separazione dei pezzi dalla piattaforma di costruzione.
- Rimozione dei supporti: le strutture di supporto, aggiunte per la corretta fabbricazione del pezzo, possono essere rimosse manualmente oppure di macchina.
- Trattamento termico di ricottura: il rapido raffreddamento, che il materiale subisce durante il processo di fabbricazione additiva, produce una microstruttura molto fine. La ricottura ha lo scopo di aumentare la dimensione dei grani cristallini e migliorare la lavorabilità del materiale.
- Sabbiatura: serve ad uniformare la rugosità sulle superfici non lavorate alle macchine utensili.
- Fresatura: le superfici di accoppiamento e i fori devono essere lavorati per ottenere le tolleranze dimensionali e di rugosità richieste da disegno. I set-up e i percorsi di lavorazione devono essere programmati in funzione della complessità del componente e dei riferimenti aggiunti nella prima fase di definizione del modello 3D. Per finiture particolari si può procedere successivamente alla rettificatura o alla lucidatura.
Problematiche relative allo staffaggio e al posizionamento sulle macchine utensili derivano dalla complessità geometrica dei pezzi prodotti in maniera additiva. L’esigenza di semplificare le operazioni di finitura ha portato alla nascita di macchinari ibridi, in grado sia di depositare il materiale sia di asportarlo. Si tratta di soluzioni che offrono un elevato livello di automazione e consentono la fabbricazione additiva e la contestuale finitura dei pezzi nello stesso posizionamento sulla macchina. Attualmente sul mercato sono disponibili i sistemi di produttori giapponesi: LUMEX Avance-25 di Matsuura e OPM250L di Sodick basati sulla tecnologia di fusione a letto di polvere e i sistemi LASERTEC65 3D di DMG Mori e INTEGREX i-400AM di Mazak che sfruttano la tecnologia laser cladding. Lo scorso anno il premio internazionale per la miglior innovazione in ambito tecnologie additive (International Additive Manufacturing Award – IAMA) è stato vinto dall’azienda anglosassone Hybrid Manufacturing Technologies con il progetto AMBITTM, un sistema automatico di cambio utensile che consente in pochi secondi di attrezzare un centro di lavoro con utensili da taglio, con una testa per la deposizione di materiale o con un tastatore per il collaudo dimensionale.
In conclusione le tecnologie additive e sottrattive non sono in competizione, ma sono fra loro complementari e sinergiche. Le aziende meccaniche che vorranno mantenere un vantaggio competitivo, se non sceglieranno di integrare i propri reparti di lavorazione con tecnologie additive o ibride, dovranno quantomeno dominare l’asportazione di materiale su geometrie complesse e di nuove leghe inter‑metalliche, che in futuro verranno sviluppate miscelando le polveri per la fabbricazione additiva.
a cura di Paolo Minetola
Condividi l'articolo
Scegli su quale Social Network vuoi condividere