Dradura Italia lancia il progetto di ricerca GD 4.0, sviluppato con l’Università di Padova e Azzurro Digitale, cofinanziato con il bando SMACT.
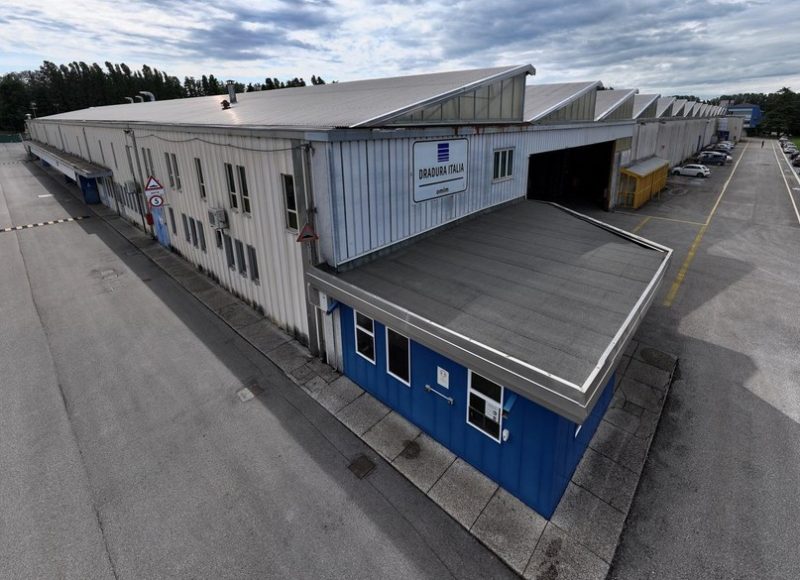
Sviluppare un approccio basato sui dati per monitorare e ottimizzare i processi di galvanizzazione, puntando a mantenere elevati standard qualitativi e a ridurre i margini di errore, e diminuendo al contempo l’impatto ambientale dei processi produttivi.
È questo l’obiettivo di Dradura, filiale italiana a San Donà di Piave (VE) del gruppo tedesco Dradura GmbH, attivo nella produzione di articoli in filo metallico, che ha sviluppato GD 4.0, un progetto di ricerca sperimentale che ha ottenuto un cofinanziamento di 170mila euro nell’ambito del Bando IRISS promosso da SMACT Competence Center.
Un progetto efficace e sostenibile
Il progetto è in collaborazione con l’Università di Padova e Azzurro Digitale, società padovana specializzata nella digital transformation delle aziende nell’ambito operations.
Attraverso una serie di algoritmi di Machine Learning e modelli di Intelligenza Artificiale, GD 4.0 implementa un sistema di manutenzione predittiva e preventiva per gli impianti galvanici, riducendo gli errori di qualità di almeno il 10% e individuando in tempo reale eventuali anomalie di processo.
Questa tecnologia consente, inoltre, di ridurre di circa l’80% il tempo di apprendimento e di onboarding degli addetti alle galvaniche e dei responsabili di produzione.
A tutto questo si aggiunge la significativa riduzione dell’impatto ambientale dei processi produttivi, diminuendo la necessità di rilavorare i prodotti e ottimizzando l’allocazione delle risorse.
La piattaforma digitale predittiva
Il progetto prevede lo sviluppo di una piattaforma digitale finalizzata al tracciamento e monitoraggio di tutte le attività svolte nell’impianto galvanico e durante il relativo processo da parte degli operatori.
Il tool digitale guida l’operatore nell’esecuzione delle attività e nella manutenzione programmata, permettendogli di ottenere la generazione automatica dei task quotidiani da svolgere e di registrare in modo semplice i risultati.
Grazie a sistemi di allerta provenienti dall’impianto, l’operatore può visualizzare direttamente sulla piattaforma le modalità per una risoluzione tempestiva degli stessi.
In aggiunta alla piattaforma, sarà disponibile un’applicazione di carico e scarico, che consentirà un tracciamento completo dei pezzi durante il ciclo di lavorazione, l’individuazione e la segnalazione dei difetti in real time.
I dati raccolti permetteranno quindi di guidare un miglioramento continuo del servizio in ottica predittiva, grazie ai modelli di Machine Learning e Intelligenza Artificiale.
a cura di Redazione
Condividi l'articolo
Scegli su quale Social Network vuoi condividere