La collaborazione tra Hexagon e Nikon SLM per realizzare un prototipo di separatore aria-carburante AM A330, con un alleggerimento di peso del 75%.
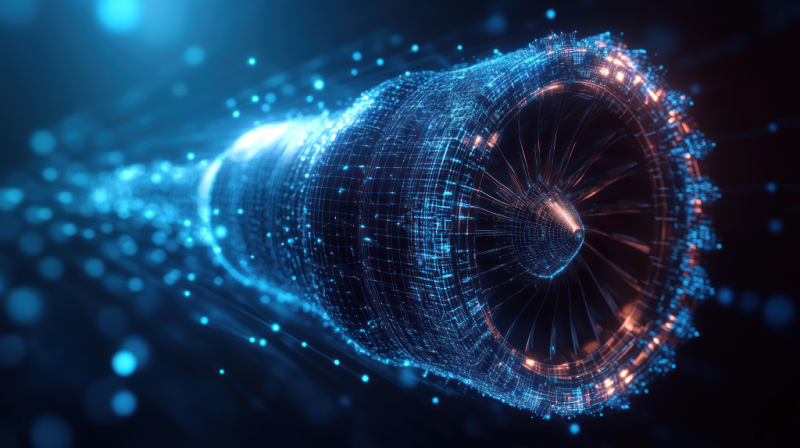
La divisione Manufacturing Intelligence di Hexagon e Nikon SLM hanno collaborato alla riprogettazione di un componente di grandi dimensioni del sistema di alimentazione degli aerei, sfruttando tutte le potenzialità della produzione additiva.
Grazie alla suite DfAM (Design for Additive Manufacturing) di Hexagon basata sulla simulazione e alla tecnologia di produzione additiva in metallo multi-laser di Nikon SLM, è stato possibile ottenere una significativa riduzione del peso, consolidamento dei componenti e tolleranze geometriche estremamente precise.
La collaborazione per il prototipo
Airbus Operations ha collaborato con i due partner per riprogettare il separatore aria-carburante, un componente essenziale per alimentare l’APU (Auxiliary Power Unit) dell’Airbus A330.
Grazie alla combinazione del software avanzato di Hexagon e della tecnologia di produzione additiva di Nikon SLM è stato possibile realizzare un prototipo semplificato e più efficiente con una riduzione del peso del 75%, passando da 35 a meno di 8,8 kg. Tale innovazione apre nuove strade all’utilizzo della produzione additiva e della progettazione basata sulla simulazione nell’industria aerospaziale.
Il separatore aria-carburante è un componente complesso e di grandi dimensioni, che rimuove l’aria dal sistema di alimentazione a carburante dell’APU, garantendo che quest’ultimo possa alimentare i sistemi essenziali dell’aeromobile quando i motori principali sono spenti.
Il componente tradizionale è composto da oltre 30 parti, che richiedono saldatura e assemblaggio manuali. Questo processo è laborioso e limita le possibilità di miglioramento del design.
Airbus Operations e Nikon SLM hanno avviato uno studio per ottimizzare la produzione e le prestazioni del separatore d’aria, creando un processo innovativo che utilizza il sistema NXG XII 600 di Nikon SLM – una stampante 3D multi-laser per grandi formati – che ha permesso di semplificare la produzione, ridurre i tempi di consegna e ottimizzare l’installazione.
La riprogettazione basata sulla simulazione
Il team si è rivolto a Hexagon per riprogettare il componente, utilizzando il workflow DfAM per ottimizzare il sistema avanzato di stampa 3D. Grazie al software MSC Apex Generative Design di Hexagon sono stati consolidate 30 parti in un unico componente leggero, rispettando tutti gli standard strutturali e prestazionali richiesti.
Gli strumenti di simulazione Simufact di Hexagon sono stati poi impiegati per ottimizzare il processo di stampa e prevedere eventuali deformazioni, garantendo tolleranze geometriche precise. Le tolleranze globali sono state mantenute entro ±5 mm mentre quelle delle superfici funzionali critiche sono state raffinate fino a ±0,5 mm, assicurando una perfetta integrazione con il sistema di alimentazione dell’aereo.
La produzione avanzata promuove l’innovazione sostenibile
La riduzione del peso della parte, la diminuzione dei tempi di produzione e l’aumento dell’efficienza ottenuti attraverso il processo di produzione, contribuiscono a un minore consumo di carburante.
La collaborazione tra questi leader di settore ha permesso di semplificare la produzione, migliorare le prestazioni e stabilire nuovi standard in termini di efficienza. Questo progetto è la dimostrazione della potente combinazione tra produzione additiva e progettazione basata sulla simulazione, e permetterà ad Airbus di estendere l’utilizzo di queste tecnologie nei futuri progetti aeronautici.
Il case study e il relativo video sono disponibili a questo link.
Clicca qui per vedere e ascoltare la videointervista a Luca Ruggiero, Managing Director Sales Italy di Hexagon Manufacturing Intelligence
a cura di Redazione
Condividi l'articolo
Scegli su quale Social Network vuoi condividere