I robot collaborativi come sistemi di assistenza a supporto delle attività di produzione e come l’interazione uomo-robot può contribuire alla riduzione del sovraccarico biomeccanico nelle attività di assemblaggio. Un esempio concreto delle potenzialità di tale tecnologia nel migliorare le condizioni di lavoro degli operatori e le prestazioni produttive nel settore automotive.
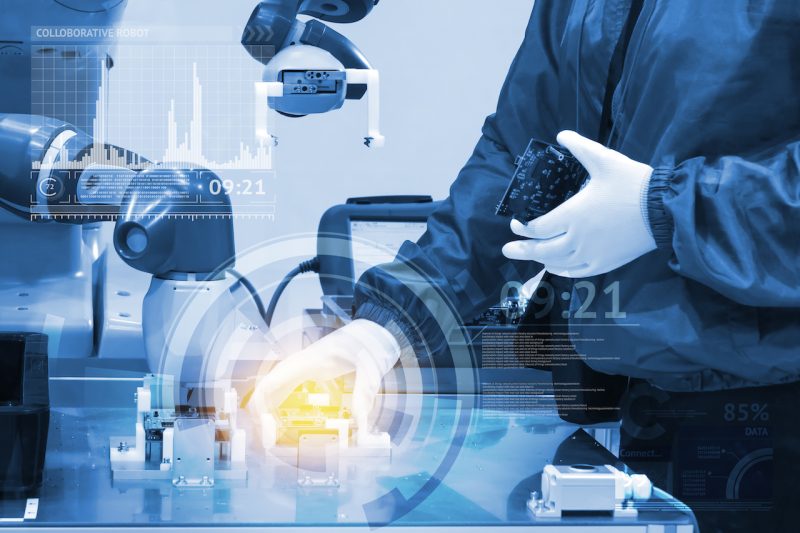
I robot collaborativi come sistemi di assistenza? Possibile. Al pari di qualsiasi altra soluzione tecnica o organizzativa, l’applicazione di una certa tecnologia per ridurre il sovraccarico biomeccanico in una postazione di lavoro manuale dipende dall’analisi dei principali fattori di rischio.
In tale contesto, la ISO TR 12295:2014 fornisce le indicazioni di massima per la corretta applicazione delle relative norme, introducendo inoltre alcuni valori di soglia per prevenire i rischi per la salute degli operatori.
In particolare, la normativa guida tecnici e progettisti nell’identificare i fattori di rischio associabili a movimentazione manuale dei carichi (intesa come sollevamento e trasporto, traino e spinta, movimentazione di bassi carichi ad alta frequenza) e posture di lavoro statiche.
I robot collaborativi come sistemi di assistenza a supporto della produzione
Qualora vengano riscontrate situazioni potenzialmente a rischio, l’automazione di processo può essere impiegata per ridurre il sovraccarico a cui l’operatore viene sottoposto.
Nel caso in cui vi siano ulteriori esigenze relative a flessibilità e riconfigurabilità di produzione, oltre che l’impossibilità di svincolarsi totalmente dalle capacità prettamente umane ottenibili solamente tramite lavoro manuale, la robotica collaborativa può rappresentare una valida opzione rispetto ad automazioni più rigide e costose.
Inoltre, la capacità di un sistema robotizzato avanzato di adattarsi efficacemente a diverse condizioni dell’operatore (ad esempio, statura o mano dominante) e del ciclo produttivo (volumi o varietà di prodotto) permette l’implementazione di un sistema produttivo realmente antropocentrico.
Un esempio pratico: il progetto “Wire cobots”
“Wire cobots” (www.wirecobots.com) è uno dei progetti finanziati dall’Unione Europea con l’obiettivo di potenziare l’innovazione robotica nelle piccole e medie imprese Europee.
Nasce dalla collaborazione tra l’azienda Carretta s.r.l e il Laboratorio Smart Mini Factory della Libera Università di Bozen-Bolzano. Partendo da un processo manuale, il progetto ha portato allo sviluppo di una postazione di lavoro antropocentrica per l’assemblaggio co-operativo di cablaggi elettrici per il settore automotive.
La soluzione proposta ha previsto l’utilizzo di un sistema robotizzato capace di assistere l’operatore nelle attività più sovraccaricanti al fine di migliorare l’ergonomia (soprattutto in termini posturali) e aumentare al contempo l’efficienza produttiva.
La possibilità di riconfigurare la cella di lavoro, come anche quella di riutilizzare il sistema robotizzato in caso di modifiche alla produzione, sono le ragioni principali per cui si è preferita una soluzione collaborativa piuttosto che una macchina completamente automatica.
Gli aspetti posturali
Il processo di assemblaggio manuale è stato inizialmente valutato per mezzo del metodo per l’analisi del sovraccarico biomeccanico “Rapid Upper Limb Assessment” (RULA), focalizzandosi maggiormente sugli aspetti posturali.
In funzione dei risultati ottenuti, è stato definito un ciclo di assemblaggio co-operativo tale da allocare al sistema robotizzato le attività potenzialmente rischiose per la salute dell’operatore.
Queste si sono rivelate principalmente quelle di nastratura dei cablaggi, motivo per cui la pistola di nastratura è stata opportunamente integrata nel sistema robotizzato (si veda figura qui sotto).
Inoltre, al fine di migliorare ulteriormente l’ergonomia della postazione, gli spazi di lavoro previsti per le attività manuali sono stati riprogettati in considerazione della “golden zone” secondo le linee guida indicate dalla ISO 14738:2002.
Incrementare la produttività
Oltre al miglioramento delle condizioni di lavoro dell’operatore, un altro importante obiettivo è stato quello di incrementare la produttività.
Al fine di conciliare i vincoli progettuali di natura ergonomica con quelli di efficienza, è stata concepita una postazione a doppio pannello con lo scopo di minimizzare il tempo ciclo attraverso la parallelizzazione delle attività tra operatore e sistema robotizzato.
Fondamentalmente, mentre l’operatore preleva e sistema i cablaggi su di un pannello, il sistema robotizzato procede in parallelo sull’altro (nastrando insieme i vari componenti), e viceversa.
Ridurre lo spazio condiviso
Inoltre, per ragioni di funzionalità e sicurezza, è stato previsto che l’operatore debba lavorare sul lato frontale della postazione mentre il robot possa operare simultaneamente dalla parte posteriore, approcciando i luoghi di nastratura dal pavimento sul quale è posizionato.
Tale configurazione ha permesso di ridurre allo stretto necessario lo spazio condiviso, utilizzando i pannelli come “barriere” fisiche utili a separare quanto più possibile le due risorse.
Così facendo, il sistema robotizzato può operare ad elevate prestazioni (non collaborative) durante i movimenti necessari per raggiungere i luoghi di nastratura, oltre che negli spostamenti da un pannello all’altro.
Miglioramenti tangibili
La soluzione proposta è stata preliminarmente validata per mezzo di un software di simulazione 3D al fine di individuare e correggere eventuali criticità a livello di ergonomia, tempo ciclo e (parzialmente) rischio meccanico.
Questo strumento ha permesso al gruppo di progetto di ottimizzare in modo flessibile ed iterativo diversi aspetti relativi alle posture dell’operatore, alla posizione e traiettorie del sistema robotizzato, e all’organizzazione del ciclo di assemblaggio co-operativo (si veda Fig. 1).
Il prototipo sviluppato ha permesso di verificare sperimentalmente i miglioramenti ottenibili con la soluzione proposta. In particolare, rispetto all’assemblaggio manuale, risulta ottenibile una riduzione degli indici RULA del 57% per la parte sinistra del corpo e del 50% per quella destra.
Riduzione della frequenza delle operazioni di assemblaggio (e non solo)
Sono stati inoltre ottenuti ottimi risultati in termini di riduzione della frequenza delle operazioni di assemblaggio, comportando un ulteriore vantaggio dal punto di vista del sovraccarico biomeccanico.
Al contempo, è stata stimata una riduzione del tempo ciclo del 12% e un relativo ritorno dell’investimento molto interessante.
I risultati hanno quindi dimostrando come sia possibile impiegare soluzioni di robotica collaborativa per ottenere un beneficio sia in termini di salute e benessere dell’operatore, che di prestazioni produttive.
Maggiori dettagli sullo sviluppo e sulla realizzazione della soluzione descritta possono essere trovati nei seguenti articoli:
- Gualtieri, L.; Palomba, I.; Merati, F.A.; Rauch, E.; Vidoni, R.: Design of human-centered collaborative assembly workstations for the improvement of operators’ physical ergonomics and production efficiency: A case study. Sustainability, 2020, 12(9), 3606. DOI: 10.3390/su12093606.
- Palomba, I.; Gualtieri, L.; Rojas, R.; Rauch, E.; Vidoni, R.; Ghedin, A.: Mechatronic re-design of a manual assembly workstation into a collaborative one for wire harness assemblies. Robotics, 2021, 10(1), 43. DOI: 10.3390/robotics10010043.
(a cura di Luca Gualtieri)
a cura di Simona Recanatini
Condividi l'articolo
Scegli su quale Social Network vuoi condividere