Tra gli argomenti emersi dallo User Group Honeywell, in primo piano le gigafactory. Il contributo dell’azienda in favore di produttività e sostenibilità
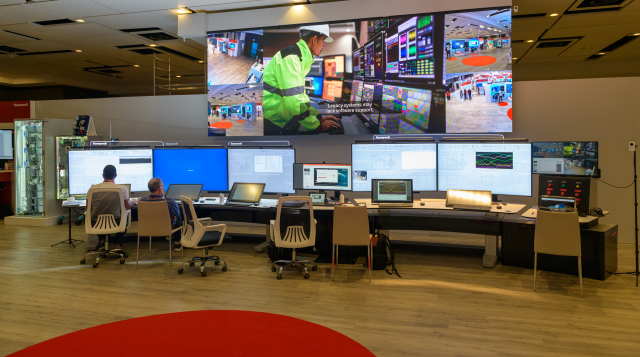
Nella transizione energetica e nelle relativa elettrificazione, la gigafactory occupa un ruolo fondamentale.
Ormai passata dalla singola realtà per la produzione di batterie al litio dedicate al modo Tesla a un concetto più generale di impianto produttivo di grandi dimensioni, la destinazione principale resta comunque quella rivolta al mondo della mobilità elettrica. Non a caso è stato uno degli argomenti al centro dell’Honeywell User Group 2024 di Madrid.
Ulteriore elemento sull’importanza di investire nel settore, quanto il tema sia protagonista anche a livello trasversale in buona parte delle pur tantissime soluzioni proposte dall’azienda e nel contesto dell’edizione numero 47 di un evento dove per definizione si combinano attualità, innovazione e competenze ad ampio raggio.
«La gestione di una gigafactory può essere paragonata al centro di controllo di una grande missione – spiega Srirama Hariharan, Principal Engineer for Gigafactories di Honeywell Industrial Automation -. Tante aree e altrettante mansioni, tutte chiamate a collaborare tra loro e da coordinare. Il traguardo di garantire una produzioni di alto volume e qualità deve partire anche da questo».
Analisi di una nuova dimensione
In pratica, un MES per come è concepito abitualmente, anche sulla base delle fabbriche di grandi dimensioni, oggi non basta più. Il salto di scala in termini di dimensioni è importante, così come le esigenze di analisi.
«Attualmente, fino al 70% dei dati raccolti non viene utilizzato come potrebbe – prosegue Hariharan -. Non vengono cioè trasformati in azioni utili e fino all’80% del tempo dedicato a gestirli viene perso».
Numeri utili anche per indicare il valore di un potenziale inespresso. La buona notizia però è che i presupporti, per raggiungere l’obiettivo di gestione con successo una gigafactory, non mancano, anche solo a partire da una migliore fase di avviamento. Nel primo anno di esercizio, gli analisti stimano infatti una produttività limitata al 60% del potenziale, con una media di 4 milioni di dollari in costi collegati alla risoluzione dei problemi.
Le dimensioni, tuttavia, rendono il compito non facile anche per il MES più evoluto. In genere, la produzione di una batteria agli ioni di litio, destinata all’autotrazione, utilizza circa duemila elementi da valutare e gestire a tutti i livelli, dall’approvvigionamento al magazzino, dalla messa in linea ai controlli qualità fino all’assemblaggio e stoccaggio finale, prima della consegna.
Una missione se non impossibile con gli strumenti attuali, sicuramente molto difficile e costosa. La visione Honeywell insegue un salto di qualità, puntando sulla tecnologia del momento. «La perfetta sintonia tra gli strumenti di un’orchestra è la chiave del successo per una sinfonia – rilancia Hariharan -. Lo stesso può essere in una gigafactory, con la possibilità di migliorare la visuale e il controllo sul ciclo produttivo per accelerare la produzione».
L’intelligenza MXP al servizio delle gigafactory
Battery Manufacturing Excellence Platform, o più brevemente Battery MXP, è la soluzione progettata per ottimizzare il funzionamento delle gigafactory accelerando anche i tempi di messa a punto e avvio di un impianto produttivo, intervenendo anche sulla qualità, a partire da una migliore resa per le celle delle batterie.
Un’evoluzione possibile grazie all’utilizzo dell’intelligenza artificiale in una veste forse meno popolare ma sicuramente più efficiente.
Le soluzioni attualmente disponibili, anche proprio perché non progettate su misura, faticano a garantire un supporto adeguato. Per esempio, il livello medio di scarti nella produzione è intorno al 30%, con picchi decisamente più alti nei primi periodi di attività.
Tradotto in cifre, considerando le dimensioni degli impianti in esame, si parla facilmente di milioni di dollari, sommando anche le conseguenze di una gestione non ottimale dell’energia.
«L’IA rende i processi più sicuri e diminuisce il tasso di errore. I dati raccolti in ogni punto dell’impianto e i relativi algoritmi sviluppati da noi, impediscono di fatto di compiere operazioni sbagliate su elementi sbagliati. Inoltre, interviene sulla logistica, garantendo le forniture e la disponibilità dei materiali al posto giusto nel momento giusto», afferma Hariharan.
Attraverso il cloud, il sistema è in grado di prelevare dati dall’impianto e dalla filiera, per raccoglierli in un centro operativo dove eventualmente distribuirli ai diretti interessati, macchinari o addetti.
Tra i risultati più rappresentativi, secondo i test effettuati da Honeywell, si arriva a ridurre fasi di test e verifica conseguenti a problemi di carica per una batteria da una decina di giorni a una questione di ore. La piena tracciabilità permette infatti di individuare il problema sin dai primi sintomi, per intervenire di conseguenza, dove possibile, in automatico.
«Dalle prime fasi i dati sono inviati al nostro cloud per le relative analisi. Subito dopo, rimandati all’impianto produttivo con le indicazioni utili a modificare i processi. Per ottimizzare l’attività, ma anche per prevenire problemi».
In dettaglio, grazie alla tracciabilità bidirezionale e alla genealogia, Battery MXP esegue un monitoraggio istantaneo delle celle delle batterie, dalla materia prima al prodotto, contribuendo a garantire la qualità in ogni sua fase. Da non trascurare, anche l’impatto sulla sicurezza operativa, con un controllo dei processi più approfondito, la gestione della forza lavoro e la prevenzione degli incendi da fuga termica delle batterie.
L’Europa pronta a recuperare terreno sulle gigafactory
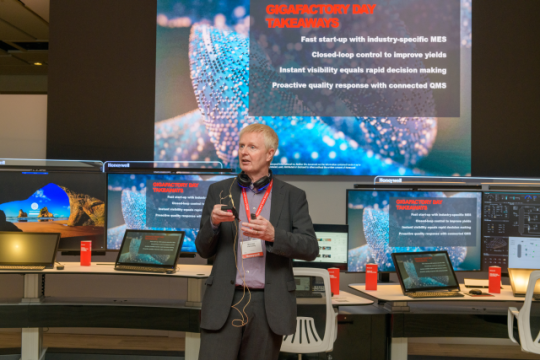
L’occasione di HUG 2024 si rivela utile anche per un’interessante analisi del potenziale mercato di riferimento. Al momento infatti, soluzioni come Battery MXP guardano soprattutto all’Asia e al Nord America.
Proprio per le prospettive di sviluppo però, anche in Europa è importante muoversi per tempo. «Lo spazio per l’automazione nella produzione di batterie è ancora molto ampio e il mercato delle gigafactory inizia a espandersi anche in Europa – conferma Michael Kennelly, Vertical Leader Sheet Manufacturing & Gigafactory dell’azienda -. Bisogna però pensare prima di tutto a trasferire anche le relative competenze, perché parliamo di una produzione dove si combinano diversi processi produttivi ai quali ispirarsi».
Gli stessi dai quali sono state ricavate le indicazioni utili a sviluppare Battery MXP e tutti i software precedenti, acquisendo e trasferendo una serie di competenze indispensabili per affrontare una sfida per tanti aspetti inedita.
«Una gigafactory non ha ancora abbastanza termini di riferimento a cui ispirarsi – prosegue Kennelly -. È qualcosa di nuovo, tutto da costruire anche sotto il profilo della gestione, con una enorme quantità di problemi da risolvere. Possiamo però contare su più dati, e individuare i pattern giusti da applicare alle analisi ci aiuta e mettere a fuoco i problemi e a risolverli».
La dimensione e la portata della sfida sono di quelle pronte a trasformarla in storica. Al momento, anche limitando la visuale all’Europa, l’Italia resta ancora svantaggiata di fronte a chi si è già mosso, a partire da Germania, Francia e Gran Bretagna prima di tutto, ma anche la Spagna. Piaccia o no, il mercato della mobilità elettrica cresce e anche a grande velocità. Continuare a esitare, è un rischio che l’Italia non può permettersi di correre. «L’Europa è sicuramente in grado di produrre batterie, ma è anche una grande sfida – conclude Kennelly -. Nella quale va coinvolta l’intera supply chain a partire dalla fasi di estrazione e lavorazione delle materie prime, fino alla consegna del prodotto finito».
di Giovanni Ticozzi
a cura di Redazione
Condividi l'articolo
Scegli su quale Social Network vuoi condividere