Oltre al driver economico, l’applicazione di soluzioni collaborative all’interno del processo produttivo può dare importanti vantaggi anche a livello ergonomico e di semplificazione del lay-out produttivo.
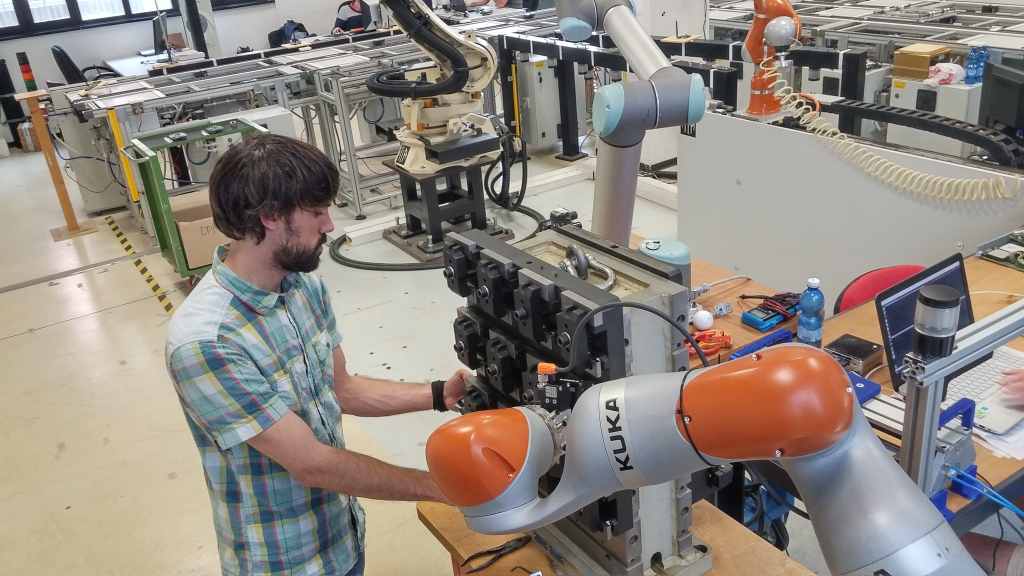
Oltre al driver economico, l’applicazione di soluzioni collaborative all’interno del processo produttivo può dare importanti vantaggi anche a livello ergonomico e di semplificazione del lay-out produttivo
In aggiunta ai costi diretti e ai costi fissi del macchinario da calcolare per un’analisi sull’opportunità di adottare soluzioni collaborative, esistono costi meno facilmente identificabili, tra i quali si possono annoverare quelli dovuti a eventuali danni, puntuali o cronici, associati alla salute o alla diminuzione di capacità operative degli addetti nelle operazioni manuali. Il fattore ergonomico e di usabilità rappresenta un punto di forza della robotica collaborativa. Esempi di miglioramento delle condizioni includono il supporto per la movimentazione e il posizionamento di tool pesanti o complessi o pericolosi, le operazioni di montaggio in posizioni scomode o difficilmente raggiungibili, la riduzione della ripetizione prolungata degli stessi gesti: in tutti i casi si verifica un alleggerimento del carico di lavoro fisico sull’operatore, a parità di produttività o con output addirittura maggiore.
Semplificare il lay-out produttivo
Un altro elemento di considerazione per la scelta di soluzioni collaborative riguarda la semplificazione del layout di impianto. Grazie alla possibilità di avvicinare in modalità collaborativa (e sicura) il sistema robotizzato all’operatore, lo spazio viene condiviso in maniera più efficiente. La separazione fisica (ripari fissi) viene meno e si possono adottare le dovute strategie di sicurezza occupando meno spazio. Le soluzioni di safety automation, che fungono da requisito per la robotica collaborativa, consentono infatti di occupare lo stesso spazio del robot in due modalità di base: prevenendo contatti all’avvicinamento (adatto a robot massivi, rigidi e veloci o a condizioni applicative in cui la pericolosità esclude qualsiasi contatto) o consentendo contatti accidentali di piccola entità. Nella strategia di prevenzione contatti in movimento, il robot in cella aperta è gestito in velocità in modo da rallentare/fermarsi all’effettiva necessità e non essere bloccato anche in aree di lavoro occupate solo occasionalmente. Nella strategia di limitazione dell’entità del contatto, qualora avvenga accidentalmente, lo spazio è condiviso non solo occasionalmente ma in modo continuo. La modalità di sicurezza di base consente questa coesistenza ravvicinata in completa protezione per l’operatore [NdA: Gli aspetti di sicurezza delle modalità collaborative sono moderatamente articolati nel modo di impiego e sempre regolati da una analisi e ponderazione dei rischi: la sicurezza in robotica collaborativa sarà pertanto oggetto delle rubriche successive]
Le prime applicazioni
La robotica collaborativa si trova in una fase iniziale di introduzione nelle pratiche produttive, pertanto gli esempi applicativi sono ancora in numero limitato nonostante la percezione generalizzata del carattere di opportunità dei robot collaborativi. Tali macchine sono, infatti, disponibili da tempo relativamente breve. Anche la capacità di integrazione di sistemi robotizzati collaborativi sicuri è in fase altrettanto iniziale. Sono richieste alcune competenze particolari da utilizzare, gradualmente introdotte da integratori ed utilizzatori. Ad oggi, gli esempi di robotica collaborativa sono spesso legati all’assemblaggio. In relazione ai fattori decisionali precedentemente illustrati, alcuni ambiti molto strutturati, ad esempio l’automotive, hanno beneficiato di condizioni favorevoli: in aziende dotate di processi molto organizzati, con precedente esperienza o favorevolmente inclini all’uso della robotica in termini puramente automatizzati, è più facile espandere le modalità di uso dei robot a soluzioni ibride con gli operatori. In aggiunta, le maggiori attrattività per le applicazioni collaborative si verificano laddove è maggiore la sensibilità ai criteri di ergonomia, di benessere dei propri operatori, o dove si crea molto valore aggiunto, o dove la modifica del processo di lavorazione libera spazio e risorse. Ad esempio, ipotizzando un compito manuale di avvitatura ripetuta in verticale o in posizioni scomode, si possono riscontrare benefici in termini di alleggerimento dello sforzo, l’azzeramento degli errori, magari proprio dovuti alla posizione sfavorevole o agli effetti di usura nell’esecuzione del compito a fine turno o effetti di calo dell’attenzione se eseguiti manualmente. Il sollievo dall’avvitatura lascia all’operatore una maggiore concentrazione sui compiti più critici da eseguire nel medesimo spazio, quali ad esempio il pre-posizionamento, la verifica dei riscontri, il troubleshooting, gli aggiustaggi, con la possibilità di supervisionare più di una operazione in esecuzione in parallelo nello stesso spazio. Un ulteriore esempio consiste nell’infilatura, gravosa, dei cavi all’interno di vani o dell’abitacolo di un veicolo, in cui l’uso del robot in spazi molto ristretti funge da “terza mano”. L’esecuzione del compito non può prescindere da un’azione coordinata sullo stesso oggetto (cavi e connettori) da parte sia del robot che dell’operatore. Un esempio simile di “terza mano” è legato all’assemblaggio o disassemblaggio di componenti elettronici o meccatronici (connettori, inserti, contatti), in cui l’operazione prevede spesso un movimento di posizionamento combinato con uno di inserimento/rimozione di componenti sul pezzo in posizionamento.
Una classe di esempi di grande importanza comprende, infine, le operazioni di ispezione e collaudo, in cui più che l’operazione coordinata sugli stessi componenti, prevale la compresenza nello stesso spazio per eseguire meglio e più rapidamente i compiti di prova di un prodotto a fine linea. I collaudi sono spesso caratterizzati da sequenze di test predeterminate, applicazione di sollecitazioni controllate (meccaniche, termiche, elettriche) di cui essenziale è il rispetto delle specifiche. Nel caso, ad esempio, l’operatore fallisse nell’esercitare completamente/correttamente tali sollecitazioni, le strumentazioni di collaudo rileverebbero la violazione della procedura, imponendo una ripetizione. L’integrità del collaudo non verrebbe compromessa, tuttavia il tempo ciclo subirebbe gravi ritardi. Attraverso soluzioni di robotica collaborativa, le fasi di collaudo maggiormente e criticamente ripetitive possono essere efficacemente assegnate al robot, mentre in contemporanea, sullo stesso prodotto, l’operatore esegue controlli funzionali esclusivamente umani per destrezza (interazione con una interfaccia) o per caratteristiche qualitative. Un sistema robotizzato sarebbe difficilmente in grado di competere con un operatore esperto in velocità di scansione visiva, elaborazione e giudizio, a meno della necessità di sensoristica speciale. Lo scopo quindi è quello di non gravare l’operatore con controlli più adeguati ad un robot, limitando la probabilità di errori.
Altri esempi sono riportabili, tutti accomunati dall’esecuzione di compiti a stretto contatto e da operazioni magari semplici per il sistema robotizzato ma di grande impatto sull’efficienza ed ergonomia di tali compiti. Questi aspetti non sono affatto secondari nel mantenimento di competitività ed efficacia per un periodo più lungo nella vita lavorativa, soprattutto in considerazione dell’aumento dell’età media degli addetti in molti settori. Usabilità, semplicità ed ergonomia sono gli aspetti esteriori di maggiore attrattività nell’utilizzo di robot collaborativi. Dietro le quinte, spesso neppure percepiti dagli utilizzatori ultimi, si snodano i fondamentali aspetti di sicurezza che fanno fronte ai nuovi rischi associati alle nuove opportunità dei robot collaborativi. Nei prossimi numeri, le applicazioni collaborative sono approfondite secondo le caratteristiche e i requisiti di sicurezza proposti dalle recenti revisioni normative.
a cura di Federico Vicentini
Condividi l'articolo
Scegli su quale Social Network vuoi condividere