Da Ucimu – Sistemi per Produrre la fotografia dei sistemi di produzione installati nell’industria italiana.
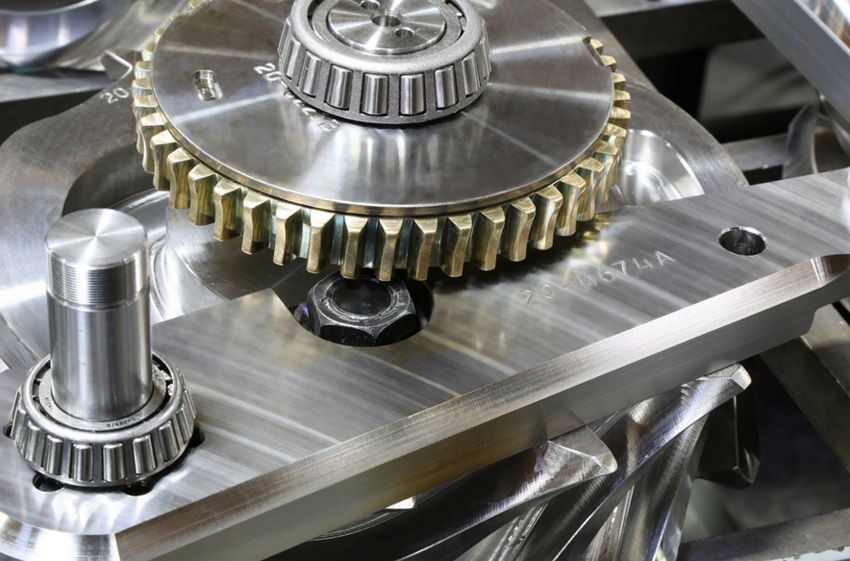
Da Ucimu – Sistemi per Produrre la fotografia dei sistemi di produzione installati nell’industria italiana.
Il parco macchine utensili e sistemi di produzione installato nell’industria italiana risulta più vecchio di quello di 5 anni fa. In particolare, nel 2019 l’età media dei macchinari di produzione presenti nelle imprese metalmeccaniche del paese è risultata la più alta mai registrata. Di contro cresce il grado di automazione e integrazione degli impianti, segno che le misure di incentivo alla competitività in materia 4.0 hanno avuto i primi effetti.
Questo, in sintesi, è quanto emerge dalla VI ricerca “Il Parco macchine utensili e sistemi di produzione dell’industria italiana”, ideata da Ucimu – Sistemi per Produrre, l’associazione dei costruttori italiani di macchine utensili, robot e automazione, in collaborazione con Fondazione Ucimu, realizzata con il contributo di Ministero degli Affari Esteri e della Cooperazione Internazionale, di ICE Agenzia e Unioncamere. L’indagine, effettuata con cadenza decennale e giunta alla VI edizione, arriva in realtà ad appena 5 anni dalla precedente, con l’obiettivo di misurare i primi effetti della politica industriale 4.0 adottata dal Paese.
I risultati dello studio sono stati presentati nel corso dell’incontro online cui sono intervenuti Barbara Colombo (Ucimu – Sistemi per Produrre), Marco Verna (responsabile Settore Meccanica Industriale di ICE Agenzia), Marco Fortis (economista), Stefania Pigozzi (responsabile Centro Studi Ucimu – Sistemi per Produrre) con a moderare Dario Di Vico, editorialista del Corriere della Sera.
Condotto su un campione rappresentativo di oltre 2 mila imprese (tutte con più di 20 addetti), lo studio fornisce il quadro su numerosità, età media, grado di automazione/integrazione, composizione e distribuzione (per settore, dimensione di impresa, aree territoriali) del parco macchine utensili e sistemi di produzione dell’industria del Paese al 31 dicembre 2019. In questo senso, l’indagine fotografa lo stato dell’industria manifatturiera (metalmeccanica) italiana, proponendo indicazioni in merito al grado di competitività dell’intero sistema economico nazionale. Le unità produttive censite sono pari al 15% dell’universo delle imprese del settore e danno occupazione al 17% degli addetti impiegati.
Per meglio contestualizzare i dati emersi dall’indagine, è bene considerare alcuni numeri di scenario. Secondo i dati dell’ultimo censimento effettuato da Istat nel 2017, l’industria metalmeccanica del paese ha subito un ulteriore ridimensionamento rispetto a quanto già rilevato nel censimento precedente (2011). È diminuito il numero delle fabbriche, risultate 15.241 nel 2017 (–3,7%) ed è calato anche il numero degli addetti impiegati, scesi sotto 1.150.000 unità (–3,1%).
I risultati dell’indagine
1 – Sono 371.664 le macchine utensili installate nelle imprese censite dall’indagine, in crescita del 21,6% rispetto al 2014 (anno della precedente rilevazione) quando erano oltre 305.520 le macchine presenti. Il dato sottende diverse considerazioni:
a) la crescita risulta notevole nonostante il settore metalmeccanico registri da tempo un progressivo ridimensionamento nel numero di fabbriche.
b) le fabbriche del settore sono tornate ad investire in nuove macchine invertendo il trend che aveva caratterizzato il periodo della precedente rilevazione, profondamente segnato dalla crisi.
c) l’acquisizione di nuove macchine non è coincisa con una massiccia dismissione dei vecchi sistemi. Per cui vi è stato un ampliamento del parco macchine e solo una parziale sostituzione di sistemi produttivi già installati.
2 – L’età media del parco macchine installato nelle fabbriche del paese è risultata pari a 14 anni e 5 mesi, in crescita di 1 anno e 9 mesi rispetto alla precedente rilevazione quando il dato era risultato già decisamente poco brillante. Si tratta dell’età più alta mai registrata dal 1975. Questo dato dimostra che l’industria italiana non riesce ad abbassare l’età media del suo parco macchine e ciò desta evidente preoccupazione. Questo fenomeno si può spiegare:
a) con il fatto che è ancora ampia la platea di imprese che non ha fatto investimenti nonostante gli incentivi 4.0. Per queste aziende si può ipotizzare che, costrette a mantenere in servizio macchine vetuste, anche per lavorazioni strategiche, si sia investito in interventi di retrofitting.
b) con la volontà delle imprese di mantenere in funzione, per certi tipi di lavorazioni (marginali e non strategiche) macchinari datati che svolgono comunque alla loro funzione.
c) con il fatto che la sostituzione dei macchinari è un fenomeno ancora piuttosto circoscritto a determinate categorie di aziende che dettaglieremo meglio in seguito.
3 – Rispetto alle due rilevazioni precedenti (2005 e 2014), cresce nettamente la quota di macchine utensili con un’età superiore ai 20 anni, risultata pari al 48% del totale installato, contro il 27% della rilevazione del 2014. Cresce però anche la quota di macchine recenti (con età inferiore ai 5 anni) risultate il 16,1% del totale, contro il 13,1% della rilevazione precedente. Questa quota è riconducibile a investimenti in macchine digitalizzate e interconnesse e documenta quindi l’avvio della transizione 4.0, sostenuto certamente dagli incentivi resi disponibili dalle autorità di governo.
4 – Sono le macchine tradizionali (asportazione e deformazione) ad avere l’età più avanzata, pari a 14 anni e nove mesi e a 14 anni e 7 mesi, dunque superiore alla media del parco. Relativamente più giovani sono i robot e le macchine lavoranti con tecnologie non convenzionali (laser, plasma, waterjet, additive manufacturing) che presentano un’età media pari a 12 anni e 5 mesi.
5 – Negli ultimi vent’anni si è assistito a una progressiva trasformazione del parco macchine installato nelle imprese italiane determinato dalla riduzione degli acquisti di nuove macchine con tecnologie tradizionali in favore di quelle con tecnologie di ultima generazione. In particolare, nel 1999, l’83% delle macchine utensili presenti nelle fabbriche era rappresentato da macchine utensili a asportazione e deformazione. Nel 2019, questa quota scende al 73%, in favore di quella delle tecnologie innovative (in particolare robot e tecnologie non convenzionali) che rappresentano il restante 27%.
6 – Osservando, per ciascuna tipologia di macchina il dettaglio delle nuove installazioni, relativo all’ultimo quinquennio (2015-2019), emerge che:
a) le macchine utensili tradizionali (sia ad asportazione che a deformazione) con età non superiore a 5 anni rappresentano appena il 15% del totale delle macchine tradizionali installate nelle fabbriche.
b) le macchine utensili a tecnologie non convenzionali di recente installazione rappresentano oltre il 20% del totale installato.
c) i robot con età non superiore a 5 anni rappresentano circa il 30% del totale presente nelle fabbriche.
7 – Il livello tecnologico del parco macchine, rilevato, in prima istanza, dall’incidenza di macchine a controllo numerico sul totale del parco installato, risulta decisamente soddisfacente perché riguarda il 54% delle tecnologie presenti nelle fabbriche. Nel 2014, anno della precedente rilevazione, la quota di macchine a controllo numerico era risultata pari a solo il 32% del totale. Pur immaginando vi sia stato un incremento tra questa e la precedente rilevazione (come dimostrano i dati complessivi della ricerca), occorre considerare che probabilmente la quota di tecnologie con controllo numerico sia stata allora sottostimata, a causa della difficoltà di tracciamento della presenza di CNC in particolare sulle macchine a deformazione che, in occasione di questa edizione dello studio, è stato invece possibile effettuare in modo più puntuale.
8 – Cresce il grado di automazione/integrazione degli impianti produttivi. L’incremento riguarda tutti e tre i livelli di automazione/integrazione ma è più deciso per i sistemi di integrazione informatica, evidente effetto delle politiche 4.0 attuate dalle autorità di governo.
a) Primo livello. L’automazione di macchine singole risulta presente sul 13,5% del totale installato, contro il 12,5% della rilevazione precedente.
b) Secondo livello. Linee di produzione (macchine integrate con altre macchine o impianti attraverso la gestione automatica di utensili, attrezzature e/o movimentazione dei materiali) la cui quota risulta pari al 12,6% del totale delle macchine presenti, più del doppio della rilevazione precedente (5,8%).
c) Terzo livello. Sistemi 4.0 (interconnessione digitale dei sistemi di controllo e gestione) risultati pari al 5,6% del totale, più del doppio del dato relativo alla rilevazione precedente (2,5%).
9 – Rispetto alla classe dimensionale delle imprese, al di là della fotografia della distribuzione del parco, interessante è lo studio dell’evoluzione della stessa nel corso dell’ultimo periodo. In particolare:
a) sebbene le piccole unità produttive restino al primo posto per numero di macchine installate, la quota detenuta si riduce notevolmente fermandosi al 39%, rispetto al 45% della rilevazione 2014 (quando già era risultata in forte calo rispetto al 53% della rilevazione 2005).
b) risulta in calo, anche se più contenuto, la quota detenuta dalle imprese con 50-99 addetti, scesa al 21% contro il 22% della rilevazione 2014.
c) cresce la quota presente nelle imprese con 100-199 addetti che sale al 14,5%, dal 13% del 2014.
d) meglio di tutti fanno le imprese di grandi dimensioni che vedono crescere la quota di oltre il 5% a più del 25%, contro il 20% rilevato nel 2014.
Questa analisi suggerisce due considerazioni: la prima – evidente – che le grandi imprese hanno più di un quarto del totale del parco macchine installato e sono le realtà che attualmente investono di più in nuovi sistemi di produzione; la seconda più “sottile” è che vi è una ideale spaccatura tra le aziende con meno di 100 addetti e quelle più grandi. Il fenomeno di redistribuzione delle quote di parco macchine rispetto alle classi dimensionali documentato da questa indagine mostra, infatti, (come, d’altra parte, fanno anche altri indicatori non legati a questa ricerca) che le aziende con più di 100 addetti performano meglio di quelle di dimensione inferiore.
10 – Dall’analisi dei dati ripartiti per settore emerge che la distribuzione del parco macchine rispetto agli utilizzatori risulta molto più frammentata che in passato.
I costruttori di macchine e materiale meccanico sono i principali utilizzatori di macchine utensili con il 35% del totale del parco.
Seguono i costruttori di prodotti in metallo che assorbono il 26% del totale. Nella precedente rilevazione questo settore occupava di gran lunga il primo posto con il 49% del totale del parco.
Terzo per utilizzo di macchine utensili è il settore dei mezzi di trasporto, pari al 21%.
Cresce poi il peso dei settori “a minor utilizzo di macchine utensili”: materiale elettrico ed elettronico (8%); produzione e prima trasformazione dei metalli (6,5%); strumenti di precisione e elettromedicale (3%).
11 – Riguardo la distribuzione geografica del parco macchine, dall’indagine emerge che la Lombardia è, ancora una volta, la regione con il maggior numero di macchine installate (28%); segue il Triveneto (18,4%), l’Emilia-Romagna (15%), Sud e Isole (13,4%), Piemonte (13%); Centro (12%).
Alcune considerazioni finali
L’incremento dell’età media del parco a 14 anni e 5 mesi, pari a 1 anno e 9 mesi in più rispetto alla rilevazione precedente, è determinato dalla ancora ampia presenza all’interno degli stabilimenti, di macchine vetuste, risultate pari a circa la metà del parco installato.
D’altro canto, il livello tecnologico del parco macchine è decisamente cresciuto grazie ai nuovi investimenti effettuati nell’ultimo periodo, investimenti che riguardano tecnologie dotate di più alti livelli di automazione e integrazione, certamente stimolati dalle misure di incentivo 4.0.
«Dai risultati della ricerca – ha rilevato Barbara Colombo – emerge la tendenza all’allargamento della forbice tra imprese che investono e crescono in competitività e imprese che restano ferme. I provvedimenti per sostenere l’ammodernamento del parco macchine e per incentivare la transizione 4.0 del manifatturiero del paese hanno prodotto effetti interessanti ma non ancora sufficienti ad assicurare la trasformazione digitale del metalmeccanico. Per questa ragione occorre che le misure attualmente operative, quali il credito di imposta per gli acquisti in nuove macchine tradizionali e con tecnologia 4.0, proseguano oltre il 2022. Anche in considerazione del crescente gap tra imprese innovative, per lo più realtà con almeno 100 addetti, e imprese ferme alle tecnologie di vecchia concezione, tipicamente di dimensione ridotta chiediamo alle autorità di governo di rendere queste misure strutturali, così da permettere alle aziende di fare piani di investimento di medio lungo-termine, attraverso i quali cadenzare i programmi di acquisto. Inoltre, in parallelo a questo chiediamo che sia allungata anche l’operatività della misura del credito di imposta per la formazione (che oggi, nel calcolo, contempla anche il costo del formatore) così da assicurare alle imprese un corretto supporto per l’aggiornamento del personale. Solo così gli investimenti in tecnologie di nuova generazione potranno realmente assicurare all’impresa miglioramento della produttività e l’efficienza necessaria a vincere la sfida della competitività nello scenario internazionale».
a cura di Loris Cantarelli
Condividi l'articolo
Scegli su quale Social Network vuoi condividere